Технология производства арболита своими руками
Дата: 11 января 2018
Просмотров: 4042
Коментариев: 0

Для возведения домов строители применяют различные виды блоков, обеспечивающих устойчивость и экологическую чистоту строений. Желая уменьшить сметную стоимость строительства, некоторые блочные материалы застройщики изготавливают самостоятельно. Один из таких стройматериалов – арболитовые блоки, основой которых являются древесные отходы и портландцемент. Технология производства арболита в бытовых условиях требует подготовки и соблюдения определенных условий для обеспечения гидратации цемента. Остановимся детально на нюансах изготовления.
Особенности арболитовых блоков
На эксплуатационные свойства и область использования арболита влияют:
- состав материала;
- используемая рецептура;
- технология производства.
Изготовленный из качественного сырья и с соблюдением технологии, арболит обладает комплексом серьезных достоинств:
- прочностью. Прочностные характеристики материала позволяют ему сохранять целостность, воспринимая действующие нагрузки от элементов строения;
- морозостойкостью. Арболитовые блоки способны сохранять свойства после многократных циклов замораживания с дальнейшим отстаиванием;

Арболит – строительный материал, изготовленный из древесных опилок, стружек, портландцемента и химических добавок
- пониженной теплопроводностью. Стены, изготовленные из арболита, поддерживают комфортную температуру жилого помещения, снижают потери тепла;
- звукоизоляционными характеристиками. Арболитовый массив поглощает внешние шумы, обеспечивая звукоизоляцию помещения;
- легкостью. Благодаря уменьшенному весу снижаются нагрузки на основание здания, что повышает продолжительность его эксплуатации;
- безвредностью для окружающих. Стройматериал изготавливается из экологически чистого сырья, не оказывает отрицательного влияния на здоровье людей;
- продолжительным ресурсом использования. Здания могут безопасно эксплуатироваться на протяжении 4–5 десятилетий;
- удобством применения. Стройматериал легко сверлится, режется, а также штукатурится без применения дополнительных сеток доля армирования;
- дешевизной. Легкие блоки производятся из недорогих ингредиентов, позволяют существенно сэкономить на заливке основания.
Кроме того, из-за древесной щепы, являющейся главным ингредиентом, материал легко обрабатывается. В него легко завинчивать шурупы и забивать гвозди. Благодаря указанным преимуществам, материал пользуется популярностью у застройщиков.
Для полного представления о свойствах стройматериала, рассмотрим слабые стороны. Недостатки арболита:
- значительные отклонения габаритов. Они обусловлены повышенными допусками. Изготовители используют литформы, отличающиеся размерами. Из-за разных размеров изделий возрастает расход штукатурной смеси;

Материал, благодаря гармоничному сочетанию лучших свойств камня и древесины, прослужит верой и правдой многие годы
- нарушение структуры при повышенной температуре. При возникновении пожароопасной ситуации арболит ограниченное время не возгорается, но при нагреве щепа тлеет, и материал постепенно теряет целостность;
- повышенная гигроскопичность. Неоштукатуренные арболитовые стены быстро насыщаются влагой. Для применения блоков следует тщательно гидроизолировать основу здания, а также выполнить внешнюю отделку.
Нарушение состава и технологии изготовления арболита сказывается на качестве продукции. При пониженном содержании извести развиваются микроорганизмы, а уменьшение концентрации цемента влияет на прочность. Строители также отмечают продуваемость стройматериала, который требует дополнительной теплоизоляции. К недостаткам следует отнести возможность появления своеобразного запаха, вызванного минерализаторами и химическими реагентами, входящими в состав арболитового массива.
Арболит – состав и технология изготовления
Для самостоятельного изготовления продукции следует правильно подобрать состав, а также тщательно изучить технологию. Несмотря на доступность применяемых ингредиентов и простоту рецептуры, имеются определенные тонкости. Рассмотрим их подробно.
Применяемый наполнитель
В качестве основы блоков применяется древесная щепа, стружка или опилки, образующиеся при обработке древесины.

Арболит безупречен для возведения жилых домов, бань, гаражей и прочих хозяйственных сооружений. Как видите, область использования довольно широка
Заполнитель следует тщательно подготовить:
- очистить от включений инородного происхождения;
- измельчить до размера, не превышающего 5х10х40 мм;
- тщательно высушить на протяжении трех-четырех месяцев;
- обработать известковым раствором, чтобы предотвратить гниение.
Однозначно квартира! Комфорт, уют и тепло, вокруг люди и инфраструктура 828 ( 7.63 % )
Только частный дом! Вокруг тишина, покой, много места и мало людей! 4946 ( 45.56 % )
Зачем выбирать что-то одно? В городе квартира, а за городом — частный дом. 4602 ( 42.39 % )
Я — свободный Гражданин Планеты Земля! Мне не нужна рукотворная клетка! 481 ( 4.43 % )
Назад
На кубический метр щепы потребуется 0,5 т 15-процентного раствора извести. Древесные отходы вымачивают на протяжении 3–5 дней с периодическим перемешиванием. При этом снижается концентрация входящего в древесину сахара, создающего благоприятные условия для развития гнили. Можно использовать покупной материал или самостоятельно измельченный в домашних условиях на щепорезе или дробилке.
Используемые компоненты
Изготовление качественного арболита возможно при обеспечении входного контроля сырья и соблюдении проверенной рецептуры.
Для производства блоков применяются следующие компоненты:
- портландцемент, являющийся вяжущим веществом. Его содержание составляет 12–16%. Такой концентрации достаточно для связывания ингредиентов и обеспечения прочности изделий после извлечения из форм;
- минерализаторы, снижающие водопоглощение и повышающие биологическую устойчивость. Используется известь после гашения и отстаивания, кальциевый хлорид, жидкое стекло, а также глинозем.

Арболит — это хороший, тёплый, экологически чистый и долговечный материал
Обеспечение необходимой консистенции арболитового состава достигается путем добавления воды, которая впитывается заполнителем, насыщая его входящими в состав смеси минеральными веществами. В зависимости от марки арболитового состава, ингредиенты вводятся в различных соотношениях. При этом удельный вес блоков изменяется от 0,3 до 1,3 т/м3.
Технология производства арболита
Стандартный технологический процесс предусматривает выполнение следующих операций:
- Подготовку заполнителя необходимых размеров.
- Дозирование и смешивание компонентов.
- Заливку готового состава в формы и уплотнение.
- Сушку в естественных условиях.
- Извлечение продукции из форм.
- Отстаивание в течение 14–20 суток.
Готовые изделия имеют форму параллелепипеда квадратного сечения со стороной 0,25 м и длиной 0,5 м. Увеличенные размеры блоков позволяют быстро производить кладку стен.
Оборудование
Для изготовления арболита необходимо следующее оборудование:
- подающий конвейер. Представляет собой шнек, обеспечивающий ускоренную подачу заполнителя при изготовлении арболита в увеличенных объемах;
- магнитный сепаратор. Он устанавливается после шнека, отделяет из непрерывного потока подаваемой на дробление щепы различные металлические включения;

Технология изготовления арболита предусматривает его изготовление также, как и фибролита, посредством смешения портландцемента с низкосортной древесной стружкой
- рубильная установка. Предназначена для предварительного измельчения щепы до требуемых размеров с помощью ротора, оснащенного ножами для резки крупного сырья;
- сепарирующее устройство. Сортирует предварительно измельченную щепу на фракции. Кондиционный материал подается в бункер, а крупный – на дополнительное дробление;
- дробилки. Применяются агрегаты, в которых повторное измельчение осуществляется специальными молотками. Они шарнирно закреплены на вращающемся роторе;
- дозирующее устройство. Обеспечивает порционную подачу в смешивающий агрегат компонентов, предусмотренных рецептурой. Производит объемное дозирование;
- механизм для смешивания. Используется обычный бетоносмеситель циклического действия, в котором исходные компоненты смешиваются на протяжении 10–15 минут;
- специальные формы. Представляют собой конструкцию, изготовленную из древесины или стали. После твердения блоков, легко разбираются для повторного использования;
- ручная трамбовка. Позволяет быстро уплотнить залитую в формы арболитовую смесь. В процессе трамбования из массива выходит воздух, и повышается плотность.
Для производства блоков в промышленных масштабах используется вибрационный станок или вибростол. Они позволяют получить продукцию повышенной плотности и отличного качества. Ускоренная подача исходного сырья в формы при промышленном методе производства осуществляется специальными бетонораздатчиками.
Изготовление арболита собственными силами

Важный этап, которым обладает технология изготовления арболита, является правильное дозирование всех компонентов
Изготовить блоки в домашних условиях можно, имея необходимое оборудование. Последовательность действий:
- Подготовьте отходы древесины. Высушите используемый материал в закрытом помещении на протяжении месяца.
- Измельчите сырье. Дробление производите в два этапа – вначале на рубильном устройстве, затем на дробилке.
- Замочите дробленку в специальной емкости с целью удаления сахара. Добавьте кальциевый хлорид.
- Заполните бетоносмеситель предварительно взвешенными компонентами. Произведите смешивание на протяжении 10 минут.
- Заполните смесью формы. Тщательно утрамбуйте состав с помощью ручного оборудования или вибростанка.
- Произведите отстаивание арболита на протяжении 5–6 суток. За это время блоки приобретут первоначальную прочность.
- Извлеките готовую продукцию на поддон, отправьте на хранение. До использования изделий должно пройти две–три недели.
При выполнении работ следует обмазать внутреннюю поверхность формы известковым молочком, облегчающим извлечение изделий.
Подводим итоги
Технология производства арболита позволяет осуществлять самостоятельное изготовление блоков только с применением специального оборудования. Важно использовать качественное сырье, а также правильно подобрать рецептуру. Готовая продукция, обладающая высокой прочностью, обеспечит устойчивость возводимых зданий.

На сайте: Автор и редактор статей на сайте pobetony.ru
Образование и опыт работы: Высшее техническое образование. Опыт работы на различных производствах и стройках – 12 лет, из них 8 лет – за рубежом.
Другие умения и навыки: Имеет 4-ю группу допуска по электробезопасности. Выполнение расчетов с использованием больших массивов данных.
Текущая занятость: Последние 4 года выступает в роли независимого консультанта в ряде строительных компаний.
технология, станок для блоков, оборудование
Производство арболита — особенная технология изготовления стройматериала, который по своим свойствам приближен к натуральной древесине. Деревобетон отличается низким уровнем теплопроводности и достаточно доступной стоимостью. Блоки из арболита обладают рядом положительных качеств, главное из которых – это пригодность к возведению стен любых зданий. Особенности производства были популярны еще во времена Советского Союза, потом схему изготовления заменили другие технологии. Популярность этих плит возвращается на современный строительный рынок.
Оборудование для производства арболита позволяет изготовить доступный и практичный строительный материал, который отвечает требованиям ГОСТ 54854-2011. Легкие бетоны на органических наполнителях растительного происхождения имеют множество достоинств:
- стойкость к биологическим воздействиям;
- материал обладает паропроницаемостью;
- хорошая звукоизоляция;
- блоки из арболита устойчивы к огню;
- простота монтажа и легкая обработка поверхности.
Состав
Компонентная составляющая арболита – это важный этап технологии производства, который нуждается во внимательном соотношении всех компонентов. При изготовлении древоблоков важно чтобы качество приобретаемых материалов было высоким. Любой бетон включает в себя вяжущие элементы, песок, наполнитель (может быть легким либо тяжелым).
Важно! При замесе щепы ее следует смочить таким образом, чтобы не выделялась лишняя влага, а сам слой игольчатой структуры был покрыт цементным составом. При процессе трамбовки цемент послужит связующим звеном, наружные поры у блоков закроются, таким образом, изделие станет не продуваемым.
Размеры щепы влияют на количество цемента, который будет использоваться при приготовлении одного кубометра арболита. Когда щепа изготовлена из сухого дерева, получается мелкая фракция. Игольчатая структура для скрепления между собой требует большего количества цемента. Необходимый объем материалов для изготовления одного кубометра арболита:
- 8-10 кг химических препаратов;
- 250 кг цемента;
- примерно 200-250 кг щепы.
В щепу добавляют такие материалы:
- гашеную известь;
- раствор жидкого стекла;
- портландцемент;
- хлористый калий;
- алюминиевую и сернокислую кальциевую смесь.
Технология
Изготовление блоков из арболита организовывают как в домашних условиях, так и налаживают масштабное производство, как прибыльный бизнес. Для этого учитывают все аспекты и стадии изготовления, руководствуются нормативными документами.
Технологию производства арболита по ГОСТУ необходимо начать с подготовки нужных ингредиентов, из которых 85 % составляет деревянные компоненты. Применяется древесная щепа, опилки, стружка. Наиболее подходящие породы древесины: сосна, пихта, ель, тополь, осина, береза. Допускается присутствие коры, листьев и хвои – не больше 5 % от общего объема. Заготовки пропускаются через станок для щепы и измельчаются. Рекомендуемый размер частичек 5х25 мм. Разнофракционный состав будет обеспечивать нужную плотность арболита.
Производство плит из арболита крупных габаритов требует дополнительное армирование изделия. В форму, заполненную на половину, следует поместить арматурный каркас из арматуры и далее заполнить деревобетонным составом.
Технология подготовки древесного сырья в домашних условиях производится различными методами – сооружение щепореза своими руками либо заключение договора с лесопилкой о поставке отходов деревообработки.
В промышленном производстве в сырье добавляют химические реагенты – хлористый кальций, сернокислый алюминий, жидкое стекло. При домашнем изготовлении рекомендуется выдерживать щепу три месяца на улице при этом опилки следует периодически перемешивать. Чтобы ускорить процесс в насыпь добавляют окись кальция – на один кубометр идет 200 литров 1.5 % раствора.
В роли вяжущего элемента подойдет портландцемент 400 – 600 марки. Смесь состоит на 10-15 % из цемента и не более 1% пластификаторов и деминерализаторов. Перед смешиванием составляющих частей, древесный компонент заливают 10 % раствором извести, потребуется выдержать 3 часа. На промышленных предприятиях такая методика вымачивания в технической емкости занимает до 3 дней.
Все компоненты смешиваются в бетономешалке. В итоге получится однородная масса без комков. Состав воды-щепы-цемента равен 4:3:3. Смесь должна быть немного рассыпчатой по консистенции и при сжатии держать форму.
Процесс получения древоблоков
На стадии формовки используются лотки, которые придают изделиям стандартные размеры. Если требуется сделать блоки нестандартных габаритов, в формы вставляются пластины, которые увеличивают размер и массу изделия. Плита может быть треугольной или трапециевидной.
Для ускорения затвердевания в раствор добавляют сухую хлористо-кальциевую смесь. Заливание раствора делают слоями в три этапа в заранее обработанные формы известью. Далее смесь потребуется утрамбовать.
Верхнюю поверхность блоков рекомендуется выровнять шпателем или правилом. После залить штукатурной смесью, примерно на 20 мм.
Когда образовалась у стройматериала форма, его уплотняют при помощи деревянного приспособления обитого металлической рамой. Наиболее прочным и надежным является стройматериал, который выстоял и затвердел на протяжении 10 суток при температуре +150 градусов Цельсия. Чтобы блоки не пересыхали, их периодически поливают водой.
Оборудование
Нужные агрегаты по изготовлению арболита продаются в сборе и включают в себя все циклы обработки и приготовления. Передовые технологии позволяют делать различные объемы стройматериала с разными размерами. Для сооружения станка своими руками, понадобятся такие агрегаты:
- щепорез, который также можно сконструировать своими руками;
- бетонорастворомешалка либо смесительный аппарат;
- пресс-формы;
- вибростанок.
Производить арболит можно самостоятельно организовав выпуск блоков, и при этом минимизировать затраты на нужную технику. Станок для дробления щепы также изготавливается своими руками при помощи использования подручных устройств. Для экономии средств вибросито заменяют на ручной метод просеивания.
Агрегат для изготовления рабочего раствора рекомендуется заменить автобетономешалкой. Ручной способ замешивания в методике недопустим, так как имеется риск образования в растворе комков и сгустков.
Формы требуемой величины делают из обычных деревянных ящиков. Дно и бока рекомендуется, заслать линолеумом либо пленкой из полиэтилена, это позволит составу не влипать в стенки.
Когда формы будут залиты по технологии, смесь уплотняют. Для этого понадобится молоток для простукивания стенок в емкости и дрель, которой делают вибропресс. Также используют самостоятельно сделанный вибростол. Этот аппарат уменьшит время изготовления и повысит производительность.
Если условия для сушки материала не подходят, рекомендуется воспользоваться сушильной камерой. Такой метод сушки увеличит затраты на производство и сделает прочность блоков выше.
Станок для блоков арболита своими руками чертеж
- Вибропресс с механизмом фиксации формы.
- Форма с функцией самозапечатывания.
- Подъемно-поворотный бункер с механической подвеской.
- Лебедка для управления бункером.
- Смеситель.
- Лебедка для подъема дозаторов с подвеской.
- Тележка с дозатором для щепы.
- Дозатор для цемента на тележке.
- Емкость для приготовления древесного консерванта.
- Платформа наклонная.
- Поддон.
- Рокла.
- Металлическая конструкция.
Производство своими руками
Технология самостоятельного изготовления арболита не сложная при наличии необходимого инструмента и устройств. Если соблюдать все правила и критерии изготовления, правильно рассчитать компоненты продукт будет иметь высокое качество и прочность.
Материалы и приспособления:
- Специальная емкость для компонентов.
- Вибрирующий стол.
- Поверхность с ударно встряхивающими функциями.
- Металлические поддоны.
- Для того чтобы получить качественный раствор необходима автобетономешалка. Если смешивать собственноручно, то для получения раствора нужной консистенции понадобится много времени и сил.
- Специальные пластиковые формы необходимых размеров. Арболитовые блоки имеют прямоугольную форму, стандартные размеры – 500х189х300 мм и 500х188х200 мм.
- Специальный станок профессионально измельчит щепу.
- При помощи пресса получается высокая плотность материала. При процессе трамбовки из материала по максимуму убирается воздух.
- Камера для сушки блоков из арболита превращает структуру в твердый однокомпонентный материал.
- Лопаты для того чтобы загрузить смесь в формы.
- Армирующая сетка применяется для скрепления древоблоков.
При наличии таких приспособлений в среднем производится за месяц от 400 до 500 кубометров строительной смеси. Рекомендуемая минимальная величина производственного помещения 500 м2. Расходы электроэнергии составят 15-45 кВт?ч. При подготовительных работах органические компоненты заливают жидким цементом до образования однородной массы. Соблюдая пропорции и расчеты, получившаяся смесь должна быть сыпучей.
Бункеры и формы имеют стандартный размер 20х40х60 см их можно сварить или сделать наборными из раскроенных листов металла. Рекомендуется блоки при изготовлении располагать вертикально, это упростит трамбовку при малой площади пресса.
Отзывы и рекомендации специалистов при самостоятельном производстве блоков
Эксперты и частные строители, практикующие изготовление арболитовых блоков оставляют отзывы, в которых советуют следовать правилам, помогающим достичь высокого качества продукции.
- В технологии производства рекомендуется применять не только щепу больших размеров, но и применять опилки и деревянную стружку.
- Консистенцию древесины обрабатывают таким образом, чтобы из нее удалился сахар. Методика позволит предотвратить дальнейшее вспучивание готового материала, что категорически недопустимо в постройке домов.
- В процессе изготовления раствор нужно тщательно перемешать и проследить, чтобы все части были в цементном растворе. Этот момент важен для качественного и прочного скрепления древесных и прочих материалов в блоках.
- При изготовлении важно добавлять алюминий, гашеную известь и прочие компоненты. Например, добавленное в состав жидкое стекло не будет позволять впитывать влагу готовому стройматериалу, а гашеная известь обладает антисептическими свойствами.
- Хлористый калий не позволит образоваться в структуре микроорганизмам и прочим веществам, влияющим неблагоприятно на материал.
- При смешивании компонентов рекомендуется следить за пропорциональностью, чтобы приготовленная смесь соответствовала требованиям производства блоков из арболита.
Технология изготовления арболита. Арболит: технология производства, состав
Производство строительных материалов на сегодняшний день — довольно прибыльная отрасль. Обусловлено это высоким спросом на все, что связано с возведением зданий. Все застройщики стараются применять и проверенные материалы и внедрять новые технологии, которые будут менее затратными в себестоимости и более практичными в применении.
Несмотря на огромный ассортимент строительных блоков, огромной популярностью стал пользоваться и арболит. Технология производства его зависит от того, в каких условиях он изготавливается. Сам материал обладает отличными эксплуатационными свойствами и характеристиками.
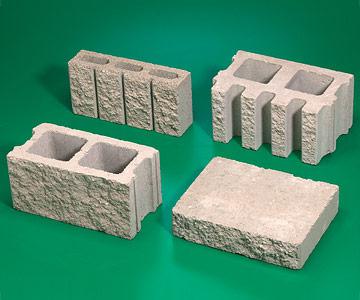
Что такое арболит?
Это строительный материал, который выпускается в виде блоков. Они имеют определенные размеры и состав. Благодаря тому, что в его производстве используется натуральное сырье, он обладает отличными техническими характеристиками.
Способы производства арболитовых блоков
Технология изготовления арболита может быть применена:
- в заводском производстве;
- при домашнем изготовлении.
Сырье для производства арболита
Технология изготовления арболита характеризуется применением определенных материалов:
- бетон марки 400 или 500;
- химическая добавка;
- органический заполнитель.
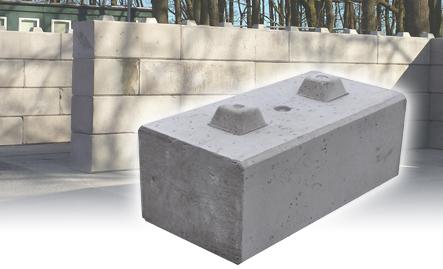
Есть некоторые рекомендации по выбору сырья. Например, бетон нужно покупать тот, который изготавливается на основе вяжущего вещества. Также можно применять бетон более высокой прочности. В качестве химической добавки используют жидкое стекло, хлорид или нитрат кальция. Органические наполнители: древесная стружка, дробленые стебли хлопчатника, дробленая рисовая соломка и многое другое.
Арболит, технология производства которого отличается применением определенных средств, может иметь различный удельный вес. Например, блоки, имеющие плотность менее 500 кг/м3 относят к группе теплоизоляционного арболита. А те, которые имеют плотность более 500 кг/м3, принадлежат уже к группе конструкционных блоков.
Соответственно, первый вариант арболита наиболее часто используется для сооружения межкомнатных перегородок, а вот из второго выстраиваются несущие арболитовые конструкции.
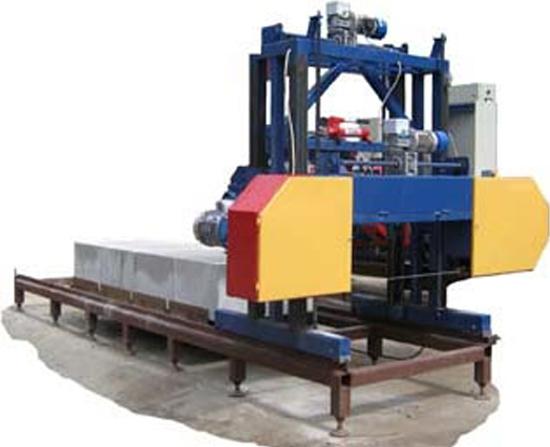
Стадии изготовления материала
Технология изготовления арболита состоит из нескольких этапов:
- подготовка определенного количества органического заполнителя;
- работа по замачиванию древесной щепы в растворе хлорида кальция;
- дозирование определенных составляющих арболита;
- непосредственно изготовление блоков.
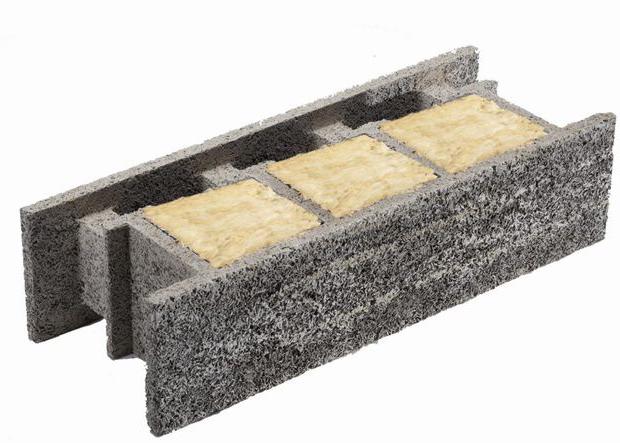
Подготовка органического заполнителя
Любое производство строительных материалов характеризуется предварительной подготовкой всего необходимого сырья. Древесина в брусках измельчается и формируется в определенные кучки. Их надо положить под навес и выдержать при оптимальной наружной температуре +15…+25 градусов около 1 месяца. После этого древесина измельчается в специальном оборудовании на щепку.
Только к такому действию нужно подходить ответственно. Щепа имеет свою определенную фракцию. Именно от нее зависит качество арболитовой смеси. Щепка размером в 10-20 мм характеризует фракционный состав в 70%, 5-10 мм уже относят к 30% фракции.
Замачивание древесины и приготовления раствора хлорида кальция
Полученную в ходе дробления щепку необходимо замочить в воде. Температура жидкости при этом должна быть не менее +20 градусов. Весь процесс замачивания длится до 6 часов. Все эти действия помогают увеличить прочность арболитовых блоков. Необходимо постоянно следить за наполняемостью древесины водой. Влажность полученного сырья должна быть не более 30%.
По истечении этого времени в бак с жидкостью выливается заранее приготовленный раствор хлорида кальция. В эту же емкость отправляется и пенообразователь.
Дозирование составляющих будущего строительного материала
Важный этап, которым обладает технология изготовления арболита, является правильное дозирование всех компонентов. Именно от этого зависит качество арболитовых блоков и его показатель прочности. Дозировка дробленой замоченной щепки должна учитывать влажность сырья. Все ингредиенты взвешиваются и дозируются согласно определенным установленным параметрам (ГОСТ). Можно использовать для этого процесса специальное оборудование. Нужно учитывать, что оно достаточно дорого, и в условиях некоммерческого производства покупать его нецелесообразно.
Процесс изготовления блоков
Необходимо подготовить специализированное оборудование для арболита. К нему на этапе смешивания ингредиентов относят бетономешалки и другие приспособления, которые могут качественно перемешивать смеси высокой плотности и доводить их до определенной консистенции.
Большую роль играет очередность закладки составляющих. Изначально засыпается подготовленная древесная щепка. Затем – цемент. После этого заливается вода и химические наполнители. Они могут меняться местами в производстве. Кому как будет удобно. Только подачу всех жидкостей стоит пропускать через специальный расходомер.
Далее происходит смешивание сырья. Мешать нужно до тех пор, пока смесь не станет однородной.
Необходимо заранее изготовить формы для блоков. Как правило, они деревянные, а размеры могут быть любыми. Внутри нее по всему периметру выкладывается линолеум. Он даст возможность после застывания смеси свободно вытащить блок из формы. Также его поверхность промазывается специальным средством.
Довольно часто в домашних условиях изготовления арболитовых блоков применяется вибростол. Он позволяет равномерно распределить смесь. После этого залитые составом формы выставляются под навес и находятся там до полного застывания. В некоторых случаях применяют определенные добавки, которые помогают сократить время отвердения цементного состава.
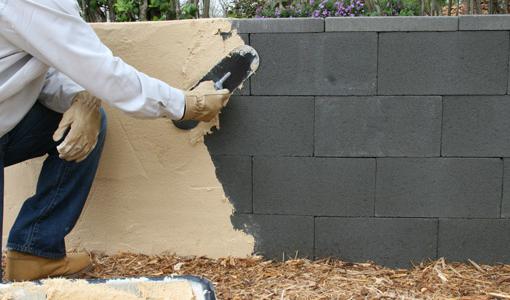
Строительство из арболита, который сделан в домашних условиях, может проводиться только по истечении определенного срока, обычно через 14-20 дней. За это время блоки полностью отвердеют, высохнут и будут готовы к кладке.
что это такое? Плюсы и минусы строительного материала, технология его изготовления по ГОСТ, отзывы о производителях
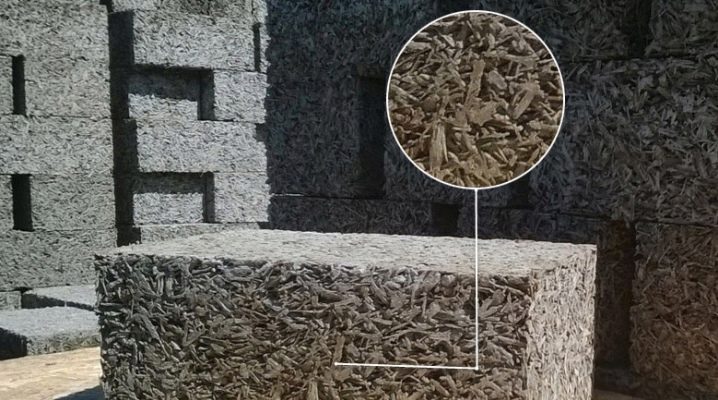
Для малоэтажного строительства создано множество разновидностей материалов. Одни из них используются чаще, другие – реже.
Несмотря на то, что арболит не является новинкой на строительном рынке, многие потребители не знают ничего о его технологии производства, об особенностях, преимуществах и недостатках.
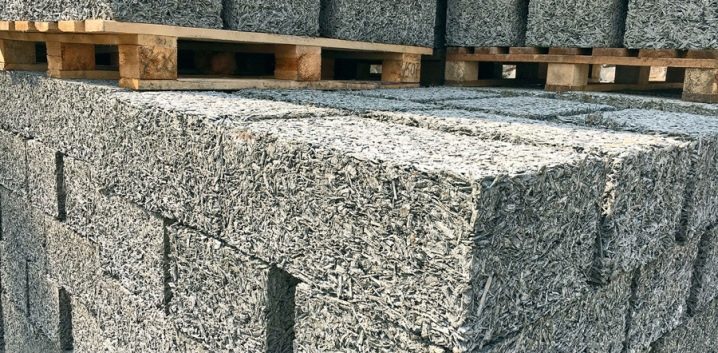
Что это такое?
Арболит – облегченный бетонный материал, изготовленный с применением органических наполнителей. Он легче большинства конструкционных стройматериалов. Например, он обладает более низкой массой по сравнению с классическим кирпичом или искусственным камнем.
Технология производства арболитовых блоков во многом определяет их технические характеристики и эксплуатационные качества. Материал должен выпускаться в строгом соответствии с нормативами ГОСТ.
Однако некоторые производители используют некачественное сырье, в результате чего получают блоки, не отвечающие заявленным характеристикам.
Состав
В арболитовую смесь могут входить различные составляющие. Согласно ГОСТ 19222-84 арболит должен состоять из нескольких компонентов.
Органический наполнитель – щепа. Чтобы получить качественные блоки, должны использоваться древесные частицы с размерами, не превышающими 30, 10 и 5 мм в длину, ширину и толщину соответственно. Помимо этого, в древесине содержание полисахаридов не должно превышать 2%. В органическом наполнителе не должно быть пораженных грибком элементов или различных механических включений. В зависимости от вида арболита содержание щепы колеблется в пределах от 75 до 90%.
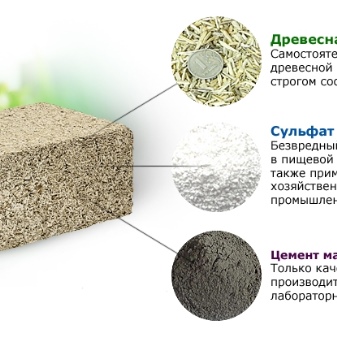
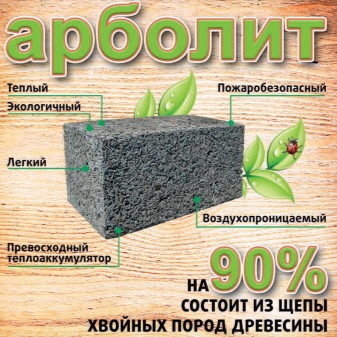
Цементное вяжущее. В качестве такого заполнителя должен использоваться портландцемент, имеющий марку не ниже М400. Некоторые производители предлагают блоки, изготовленные на основе морозостойкого цемента. Следует учесть, что при длительном хранении цементные блоки теряют первоначальные характеристики, из-за чего они могут не соответствовать требованиям, заявленным производителем.
Чтобы не столкнуться с такой проблемой, опытные строители рекомендуют покупать арболит из цемента не ниже марки М500.
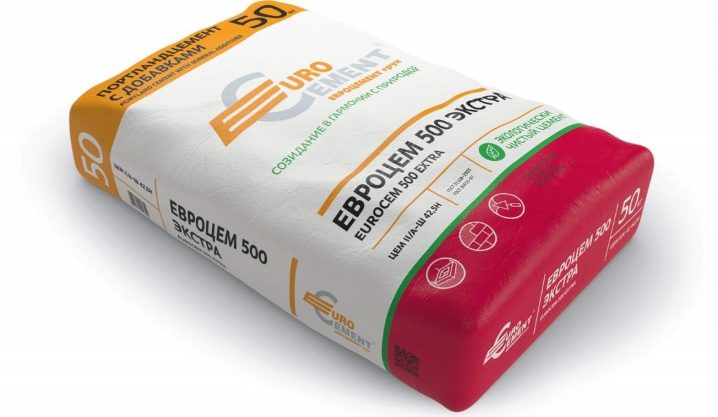
Компоненты химического происхождения. Арболитовые блоки частично состоят из органических заполнителей, которые имеют свойство гнить. Чтобы избежать поражения щепы грибком, в смесь добавляются различные химические добавки. Это могут быть хлориды кальция или аммония, сульфат алюминия или другие неорганические вещества. Такие компоненты отличаются безвредностью для здоровья человека. Они позволяют не только защитить древесную щепу от преждевременной порчи, но и ускорить процесс адгезии компонентов арболитовой смеси, при этом сократив время высыхания блоков.
Для создания арболита также используется вода. Ее качество регламентируется ГОСТом 23732-79. В воде не должны содержаться жиры и производные липидов, красящие компоненты. Для производства блоков применяется только пресная жидкость.
Перед тем как приступить к технологическому процессу, вода и химические составляющие подвергаются лабораторным исследованиям. Их проводят регулярно для каждой вновь поступившей партии.
Разновидности
Производители выпускают несколько видов такого класса бетона. Речь о них пойдет ниже.
- Строительные блоки. В эту группу входит теплоизоляционный и конструкционный материал. Эти составляющие применяются в различных сферах. Первый обладает небольшой плотностью, благодаря чему он используется для укладки теплоизоляционной основы при возведении межкомнатных перекрытий. Конструкционный вариант имеет плотность, примерно равную 800 кг/куб. м (из-за большего содержания цемента). За счет более высокой прочности такой арболит применяется для сооружения несущих стен и опорных конструкций.
- Арболитовые плиты. Применяются в качестве теплоизоляционного материала. Их плотность не превышает 500 кг/куб. м.
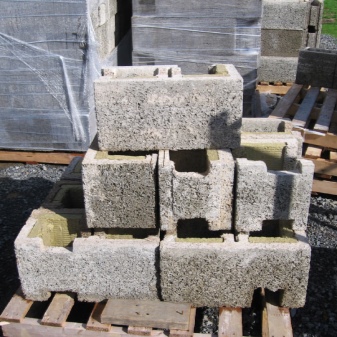
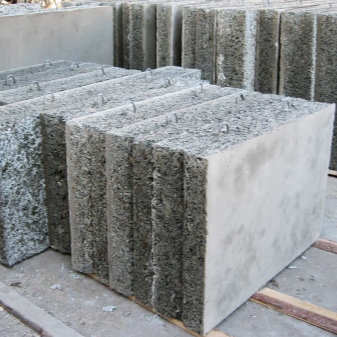
- Блоки с декоративной облицовкой. Такие изделия могут быть отделаны мраморной крошкой или облицовочной плиткой. Эти материалы стоят гораздо дороже обычных блоков. Однако строение, при помощи которых оно возведено, не нуждается в дальнейших работах по декоративной отделке фасадной части.
- Раствор. Он готовится непосредственно на стройплощадке и не подлежит хранению. Раствор применяется для создания монолитных изделий. Чаще всего он используется для утепления жилых помещений, гораздо реже – для возведения небольших сооружений. Помимо этого, из него изготавливается несъемная опалубка для сооружений, чья высота не превышает 3 этажей.
- Гипсовый арболит. Его отличие от обычного – использование при производстве гипса, вместо портландцемента. Он обладает существенными преимуществами: не требует применения химических составляющих и быстро отвердевает.
Как и любые сертифицированные строительные материалы, блочный арболит выпускается в определенных размерах. Самыми «ходовыми» считаются изделия в форме параллелепипеда с параметрами длины, ширины и высоты, равными 500, 300 и 200 мм соответственно.
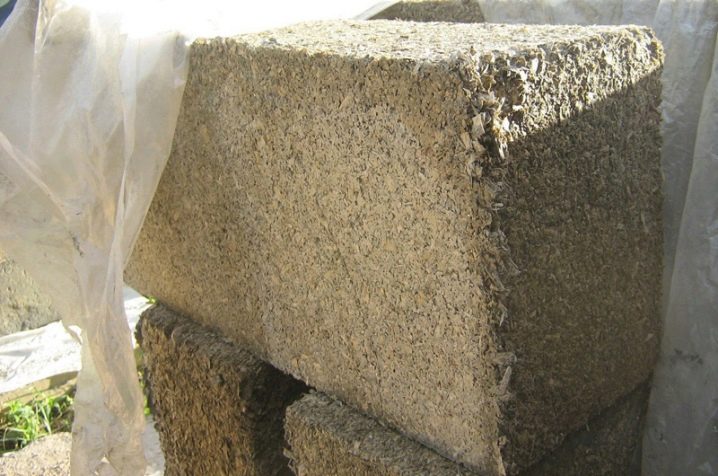
Технология изготовления
Производство арболита в блоках на крупных предприятиях автоматизировано. Процесс изготовления включает несколько этапов, которые описаны ниже.
- Загрузка органического наполнителя в дозатор. Дозирующее устройство фиксируется на подъемнике, который доставляет компонент в емкость смесительного оборудования.
- Загрузка химических реагентов.
- Добавление портландцемента определенной марки.
- Тщательное перемешивание составляющих смеси до получения однородной массы. Полученный раствор направляется на вибрационный стол с вибропрессовочным устройством.
- Разравнивание массы в формах. На этом этапе происходит сжимание изделий за счет применения пресса. При необходимости получения блоков нестандартных форм в ячейки вручную вставляются специальные пластины. В результате получаются треугольные или трапециевидные изделия.
- Отправка блоков в сушильные камеры. Температура, при которой изделия должны подвергаться сушке, не регламентирована ГОСТом. Однако материалы допускается оставлять в камере не более чем на 24 часа.
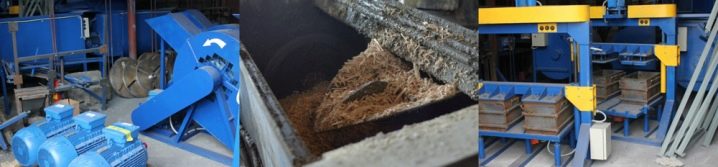
Изготовить арболитовые блоки можно и в домашних условиях. Самостоятельное создание материала – сложный процесс. Он потребует тщательной подготовки всех компонентов.
Особое внимание здесь нужно уделить древесной щепе. Из всех пород древесины предпочтительнее будут хвойные породы, такие как пихта или сосна. Присутствие коры или хвои не должно быть более 5% по отношению к общей массе.
При создании блоков в домашних условиях не у каждого строителя под рукой могут оказаться химические добавки. Без них процесс адгезии будет значительно затруднен, а также увеличится время затвердевания изделий (порой на высыхание уходит несколько недель). Самостоятельное изготовление материала высокого качества своими руками маловероятно. Чаще всего в домашних условиях создают блочные изделия для строительства сооружений с низкими эксплуатационными требованиями.
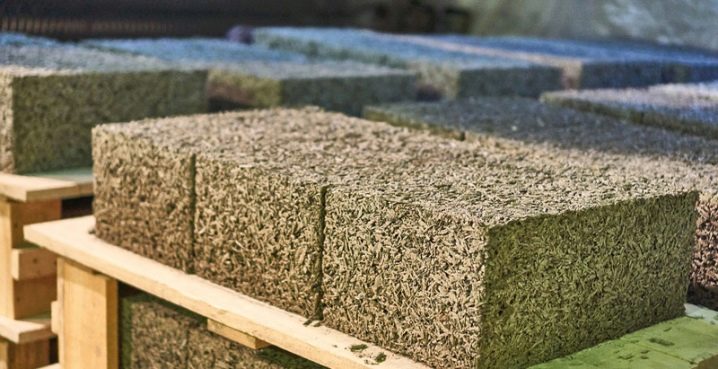
Сфера использования
Арболитовые блоки – строительный материал, который активно применяется в частном строительстве. Из него сооружают дома и коттеджи, различные постройки хозяйственного назначения. Блочные изделия отлично сохраняют тепло, из-за чего их допустимо применять даже в суровых климатических условиях. Помимо этого, материал является довольно прочным, за счет чего он пользуется популярностью в сейсмически активных областях.
В малоэтажном строительстве арболит используется как для возведения построек «с нуля», так и для утепления стеновых конструкций и напольной поверхности. Арболитовые блоки нашли свое применение при сооружении помещений складского, производственного и сельскохозяйственного назначения. Из него получаются теплые гаражи, бани, сараи и различные подсобные строения.
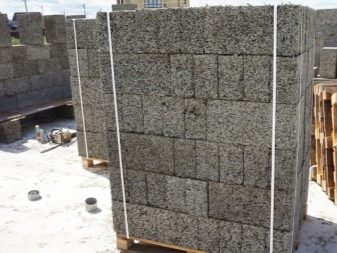
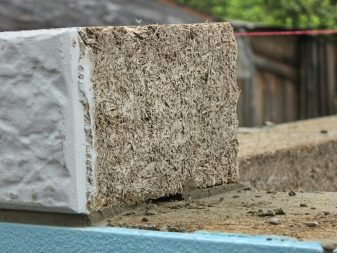
Преимущества
Чтобы решить, стоит ли выбирать арболит в качестве основного строительного материала, следует заранее изучить его свойства, а также плюсы и минусы. Ниже рассмотрены достоинства блочных изделий.
- Экологическая чистота. При производстве материала не используются химические компоненты, которые выделяют вредные для здоровья человека вещества при строительстве или последующей эксплуатации сооружения.
- Высокие показатели прочности на изгиб. При осадке почвы или сезонных движениях грунта большинство стройматериалов трескается, что приводит к образованию трещин внутреннего декоративного покрытия. Арболитовые блоки – иные изделия. Они способны деформироваться, не допуская растрескивания.
- Небольшая масса. Вес 1 куб. м арболита составляет не более 700 кг. Такой же объем кирпича имеет массу 2 тыс. кг. Строителям малый вес материала позволяет отказаться от сооружения массивной фундаментной основы, что экономит время, силы и средства.
- Быстрая кладка. При строительстве сооружений чаще всего отдается предпочтение крупногабаритным блокам (500×300×200 мм). Благодаря большим размерам материала можно создать теплоемкое сооружение за короткий временной отрезок.
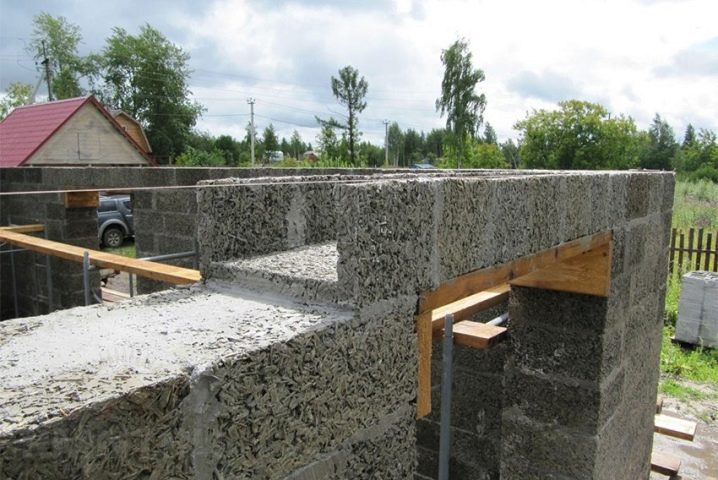
- Малый расход песчано-цементной смеси.
- Отличные теплоизоляционные свойства. Арболитовые блоки обладают низкой теплопроводностью, за счет чего они не пропускают холод извне и не отдают тепло, накопленное в помещении.
- Пожаробезопасность. Арболит – практически негорючий материал. Входящие в состав арболитовой смеси химические добавки способствуют повышению огнеупорности блоков до 3 часов. При воздействии пламени огня изделия не выделяют едкого дыма.
- Хорошая паропроницаемость. Арболитовая кладка способна «дышать». Она способствует естественной циркуляции воздуха, что обеспечивает хороший микроклимат в любом помещении.
- Биологическая устойчивость. Возведя сооружение из арболита, можно не бояться, что его перекрытие или стены будут поражены плесенью или другими видами грибка. Это позволяет сохранить деньги на покупку антисептических средств.

- Механическая стойкость. Блоки арболита довольно прочны. Им не страшны удары, падения и другие механические воздействия. Такая устойчивость доказана экспериментально: изделия с трудом разбиваются кувалдой и сохраняют свою целостность при падении с высоты до 18 метров.
- Отличное поглощение шумов. Звукоизоляция материала лучше показателей шумопоглощения древесины или кирпича.
- Возможность обработки. При необходимости блоки можно пилить обычной бензопилой, получая нужный размер изделия.
- Простой монтаж крепежных элементов. В арболитовые блоки без особых усилий вкручиваются саморезы или вбиваются гвозди.
Несмотря на многочисленные преимущества, арболит выбирает не каждый строитель. Причина проста – это недостатки материала. Для одних они являются несущественными, в то время как для других – серьезное основание для отказа от покупки арболитовых блоков.
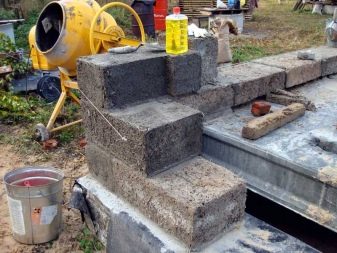
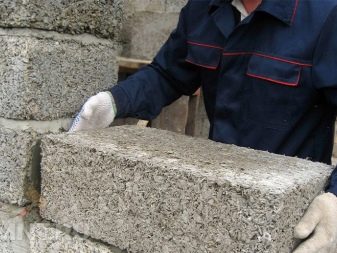
Недостатки
Арболит имеет много преимуществ, чуть меньше – минусов. К главному недостатку относят высокие риски приобретения модулей кустарного производства. Дело в том, что качественные блоки выпускают на крупных производственных предприятиях, которых не найти в регионе.
В мелких городах и некоторых мегаполисах работают «кустарники» или компании-однодневки. С целью уменьшить себестоимость готовой продукции, они нередко используют дешевое некачественное сырье.
Такие производители не задумываются об эксплуатационных качествах выпускаемых стройматериалов. Они изготавливают модули, нарушая технологический процесс. В результате они реализуют арболит, технические характеристики которого существенно ниже заявленных.
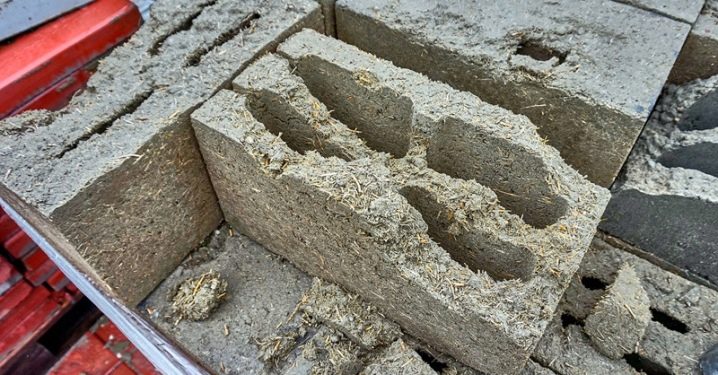
К еще одному минусу относят малую плотность материала. С одной стороны, это положительный момент, поскольку снижается нагрузка на фундамент, а с другой – такие блоки нельзя использовать для возведения многоэтажных сооружений.
Существует ряд других недостатков такого материала.
- Отклонения в размерах. Готовые блоки могут существенно различаться по типоразмерам, прописанным регламентом. Иногда из-за несоответствия параметров строителям приходится увеличивать толщину швов. Это ведет к образованию «мостиков холода» и промерзанию швов в стужи.
- Биологическая неустойчивость. Блоки из арболита – изделия, которые «полюбились» грызунам. Мыши и крысы делают в них многочисленные норки и ходы, что значительно снижает срок службы постройки. Чтобы защитить конструкцию от таких вредителей, потребуется делать бетонный цокольный этаж. А это дополнительные денежные растраты на стройматериалы и наем строительной бригады.
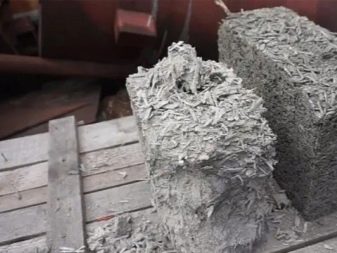
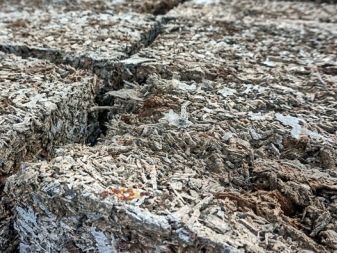
- Необходимость в декоративной отделке фасада. Арболит – эстетически непривлекательный строительный материал (если речь не идет об изделиях с облицовкой). Чтобы улучшить внешний вид строения, не обойтись без финишной отделки. Она повлечет за собой расходы на покупку облицовки и наем рабочей силы.
- Слабая устойчивость к повышенной влажности. Арболитовые блоки способны накапливать влагу, что со временем разрушает материал. Чтобы строение из арболита прослужило как можно дольше, нужно сделать фундаментную основу с хорошей гидроизоляционной оболочкой и произвести оштукатуривание внешней части стены.
- Высокая стоимость. Здесь не идет речь о блоках низкого качества кустарного производства. Изделия, соответствующие нормативам ГОСТ, стоят недешево. Их цена примерно в 1,5 раза выше по сравнению со стоимостью газобетона или пеноблока.
Некоторые недостатки арболита связаны с нарушением технологии его производства или с использованием некачественных составляющих. Чтобы не приобрести блоки, непригодные для строительства, нужно прислушаться к некоторым рекомендациям.
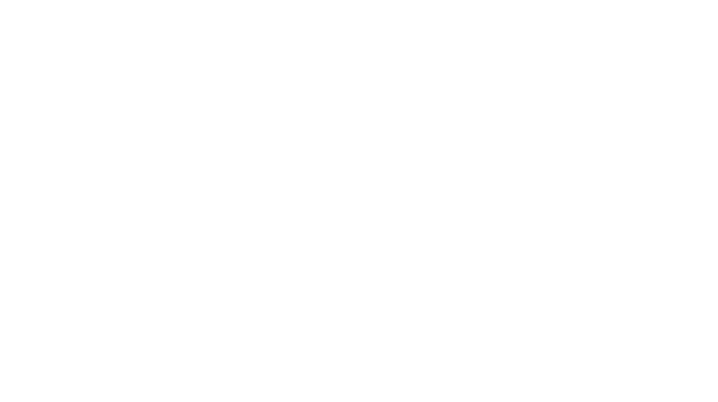
Критерии качественной продукции
Выбор арболита – ответственный процесс, поскольку от него во многом будет зависеть срок службы будущего строения, а также микроклимат внутри него. Опытные строители при покупке материала советуют, в первую очередь, обращать внимание на его стоимость. Маловероятно, что производитель будет работать себе в ущерб и продавать качественные арболитовые блоки ниже их рыночной цены.
Чтобы обезопасить себя от подделки, нужно просить у продавца соответствующие документы на товар (сертификаты качества и соответствия).
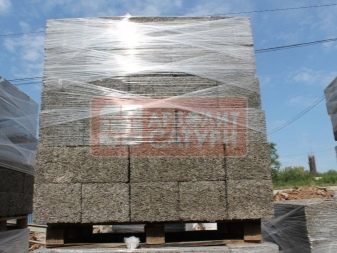
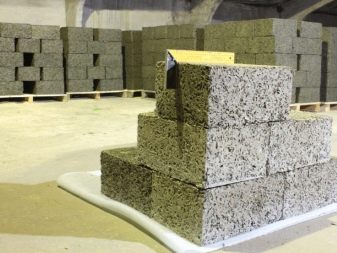
Выбирая арболит, важно произвести его визуальную оценку. Ниже приведены показатели качества такого материала.
- Однородность состава. Если арболитовая смесь была неоднородной, готовые блоки со временем будут расслаиваться. Согласно регламенту показатель расслоения должен быть менее 10%.
- Правильная геометрическая форма. Ее нарушения наблюдаются при несоблюдении условий хранения готовых изделий или технологии производства.
- Однородный серый цвет. Неравномерный окрас блоков или посторонние включения говорят о низком качестве изделий. Например, присутствующие зеленые или коричневые оттенки – признак недосушивания изделий. Стоит учесть, что материалы могут иметь различные включения (солому, опилки, хвою, древесную кору), но не более 5%.
- Щепа одинакового размера (наличие частичек с размерами, превышающими установленные нормы, недопустимы). Слишком большие древесные фракции неспособны полностью пропитаться химическими реагентами. Из-за этого они плохо смешиваются с бетоном и снижают прочность готового стройматериала.
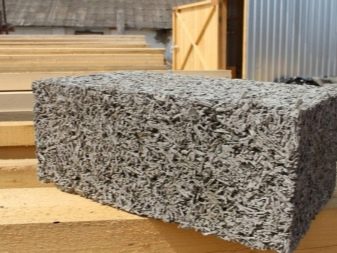
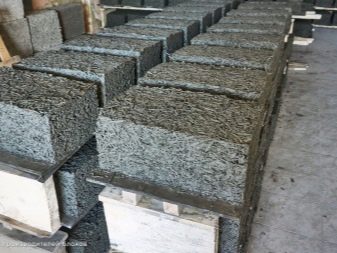
Нужно отказаться от приобретения блоков, изготовленных на основе опилок, а не щепы. Такие блоки обладают меньшей прочностью, обусловленной плохой армирующей связкой.
Чтобы точно быть уверенным в качестве арболита, следует договориться с производителем о возможности лабораторной проверки выборочных образцов материала из выпущенной партии.
Отзывы
Узнать о том, какие дома получаются из арболита, помогут отзывы их владельцев. В сети встречаются как положительные, так и отрицательные отклики.
Среди преимуществ покупатели отметили:
- быстроту и легкость возведения строения;
- отличную звуконепроницаемость;
- сохранение тепла зимой и осенью.
Потребители также отметили возможность сохранить деньги на аренде спецтехники при постройке дома, поскольку блоки перемещаются вручную по причине легкого веса.
Судя по откликам, положительно отзываются об арболите лишь те покупатели, которые приобретали материал у крупных и известных производителей. Однако в сети встречаются и отрицательные мнения. Их в большинстве оставляют люди, производящие арболитовые блоки собственноручно. Они отметили следующие негативные факторы:
- сырость и холод внутри помещения;
- неприятный запах, который не выветривается;
- промерзание межблочных швов;
- большой расход штукатурной смеси.
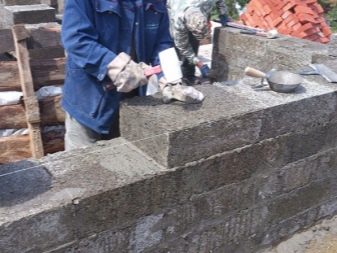
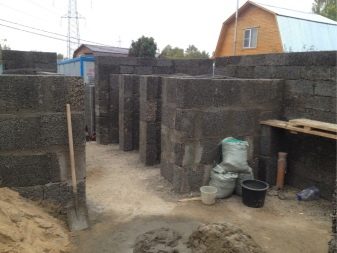
Арболитовые блоки – выбор тех, кто желает быстро и недорого возвести хозяйственную постройку или жилой дом. Чтобы помещение было теплым, сухим и тихим, следует покупать только качественные строительные изделия по реальной рыночной цене.
О плюсах и минусах арболита смотрите в видео ниже.
Арболит — технология изготовления
Чтобы получить арболит, нужно четко следовать технологическому процессу, иначе будут допущены ошибки, способные негативно сказаться на качестве итогового продукта. Получение превосходных эксплуатационных свойств, возможно только в том случае, если производитель знает, что такое арболит технология изготовления, и соблюдает все пропорции и характеристики компонентов, участвующие в процессе изготовления.
Так как арболитовые блоки обладают сравнительно небольшой массой, из них сооружаются конструкции, которые не оказывают сильного воздействия на фундамент. Застройщики получают возможность экономить на формировании фундамента и на прочих строительных работах, которые необходимы при возведении объектов из кирпича или бетонных плит.
Свойства и состав арболита
Благодаря своей пористой структуре, арболитовый блок выгодно отличается от многих других строительных материалов, так как обладает меньшим весом при больших габаритных размерах. С помощью арболита быстро возводятся объекты различной степени сложности, и остается только провести отделочные работы. В составе арболитовых блоков находится:
- портландцемент,
- связующие элементы,
- древесные опилки,
- химические добавки,
- целлюлозное сырье,
- жидкость в необходимом объеме.
Если соблюдается арболит технология изготовления, то на выходе получаются арболитовые блоки или арболитовые плиты. По свойствам данные материалы отличий практически не имеют, но зато отличаются габаритные размеры и сфера использования данных элементов.
Строить из арболита допускается различные сооружения, но они не должны превышать двух уровней, потому что данному материалу присуща склонность к деформациям под действием чрезмерных нагрузок. Зато арболитовыми плитами утепляют множество строительных объектов, причем их монтаж производится и с наружной стороны здания, и с внутренней.
Габаритные размеры и сферы применения изделий из арболита
Арболитовые блоки обладают габаритными размерами: 25х25х50 сантиметров. При помощи этих блоков быстро возводятся объекты, и кроме того, для арболита характерны:
- долговечность,
- прочность,
- устойчивость к солнечным лучам,
- устойчивость к перепадам температуры,
- экологически чистый материал,
- практичность.
Если арболит технология изготовления используется для получения плит, то производитель должен выдерживать следующие габариты изделия:
- 100х150 см;
- 100х125 см;
- 50х100 см.
Допускаются и другие размеры, но значительно реже, если делается индивидуальный заказ.
Как изготавливается арболит?
Производство материала осуществляется, как в заводских, так и в домашних условиях, и если выдержаны количественные параметры всех элементов, участвующих в производственном процессе, то получается арболит с присущими ему свойствами. Естественно, что более высокое качество имеют арболитовые блоки и плиты, которые изготавливаются на заводе на специальном оборудовании.
В основном заводские процессы автоматизированы и постоянно осуществляется контроль за производством. В процессе изготовления применяются специальные формы, сушильная камера и вибростол.
Чтобы добиться оптимального результата, необходимо использование смазывающих веществ, так как после получения плиты или блока их нужно извлекать из форм. Если этого не делать, изделие способно потерять правильную конфигурацию, а значит, получится брак.
Но все-таки в домашних условиях тоже есть возможность получать арболитовые изделия, но для этого придется все процессы выполнять вручную, пользуясь специальными приспособлениями и инструментом. Для получения данного материала потребуется:
- Бетономешалка,
- Форма из листового металла или из пиломатериалов,
- Компоненты для замешивания.
Специалисты рекомендуют использовать формы именно из древесины, так как они отличаются практичностью и обходятся недорого. Нужно только сбить из досок необходимую форму, обшить изнутри пленкой, чтобы исключить прилипание смеси к дереву, а затем заливать раствор, выдерживая параметры.
Не следует забывать про специальную смазку, чтобы не испортить арбонитовые блоки при изъятии из деревянной формы. При загрузке компонентов в формы нужно соблюдать последовательность и не спешить загружать ингредиенты в полном объеме, так как это негативно скажется на качестве и прочности блока.
Сушить плиты придется в естественных условиях, так как обычно дома отсутствуют специальные сушильные камеры – если повезет с погодными условиями, блок сформируется и высохнет в течение нескольких часов.
Покупка и доставка арболита из другого региона
В силу того, что арболит как строительный материал в новейшей истории применяется не так часто (не берем в расчет строительство во времена СССР), не во всех регионах есть «правильные» производители, которые делают блоки по ГОСТу.
В некоторых случаях выгоднее купить арболитовые блоки в соседнем регионе и привезти их при помощи транспортной компании. Фактически любая транспортная компания из тех, что мы знаем (Рус-Экспресс Rus-Express.com, ЖелДорЭкспедиция JDE.ru, ПЭК Pecom.ru) возит стройматериалы от производителя к заказчику.
Транспортной компании выгодно везти такой груз, потому что на строительство даже небольшого арболитового дома мы заказываем как минимум панель, а иногда и две — от 6 до 20 поддонов блоков.
И нам это выгодно, потому что на объеме мы можем получить скидки у производителя арболитовых блоков, и тогда доставка выйдет нам бесплатно.
оборудование, технология, пропорции и формы
Рейтинг материала
16 out of 5
Практичность16 out of 5
Внешний вид20 out of 5
Простота изготовления20 out of 5
Трудоемкость при использовании20 out of 5
ЭкологичностьИтоговая оценка
Арболитовые блоки относятся к легким стеновым строительным материалам. Они изготавливаются из опилок, древесины, цемента, воды и других составляющих.
В качестве основной составляющей используется древесная щепа, которая представляет собой рубленую древесину. У таких блоков больше граница прочности, чем у пеноблоков и газоблоков. Важными характеристиками материала являются: высокая устойчивость к трещинам и ударопрочность.
Технология производства
Первоначальным этапом производства арболита является тщательная подготовка всех необходимых компонентов, затем следует приготовление основы, ее отлив в формы для дальнейшего получения блоков.
Подготовка основы
Наполнитель для блоков включает в себя стружки и опилки в пропорции 1:2 или 1:1. они должны быть хорошо просушены, для этого их выдерживают 3-4 месяца на открытом воздухе, периодически переворачивая и обрабатывая раствором извести.
В последнем случае на 1 куб. метр сырья необходимо около 200 л раствора извести 15%. В нем будут находиться древесные компоненты в течение 4 дней, которые требуется перемешивать 2-4 раза в день.
На данном этапе главная цель – это убрать сахар, содержащийся в опилках. Он может стать причиной их дальнейшего гниения.
Щепу можно купить готовую, а можно сделать самим, соорудив щепорез. Что это такое и как он работает, расскажет видео:
Необходимые компоненты
После того как опилки подготовлены, к ним присоединяют следующие добавки:
- Гашеная известь;
- Сернокислый кальций и алюминий;
- Портландцемент 400 марки;
- Растворимое жидкое стекло;
- Хлористый кальций.
Как правило, доля этих компонентов в арболитовой смеси не превышает 4% от массы цемента. Они придают конечному продукту устойчивость к гниению, обеспечивают высокую огнеупорность и пластичность.
Технология изготовления
Арболитовые блоки имеют оптимальные параметры 25 см*25 см*50 см. они удобны не только в процессе изготовления, но и при укладке. Процесс отливки заключается в следующем: блоки заполняются арболитовой смесью из трех слоев. После каждого подхода следует тщательное уплотнение деревянным молотком, обшитым жестью.
Лишняя масса ударяется при помощи линейки, а форма выдерживается сутки с температурой воздуха от +18оС. По истечению времени блоки извлекаются из форм путем небольшого постукивания и выкладываются на ровное основание для полного затвердения на 2 дня и просушивания на срок от 10 дней.
На фото — процесс выемки арболитового блока из станка после формовки:
Оборудование
Чтобы производить арболитовые блоки может потребоваться различное оборудование в зависимости от объема производства и используемого сырья. Процесс изготовления данного строительного материала и его конечный результат должны отвечать ряду критериям: ГОСТ 19222-84 и СН 549-82.
Чаще всего для производства арболита используются остатки деревьев хвойных пород. Их измельчение производится на рубильной машине (РРМ-5, ДУ-2 и прочие). Более тщательный процесс дробления производится на дробилках (ДМ-1) или молотковых мельницах. На вибростолах из измельченной древесной смеси отделяются кусочки земли и коры.
Саму арболитовую смесь рекомендуется приготавливать на лопастных растворосмесителях или смесителях принудительного цикличного действия. Перевозить готовую смесь к специальным формам можно с помощью кюбелей или бетонораздатчиков. А сам подъем транспортера не должен превышать 15о вверх и 10о вниз при скорости движения до 1 м/с. Падение смеси осуществлять на высоте не более одного метра.
Уплотнение конструкций можно произвести как ручными трамбовками, так и вибропрессом (Рифей и прочие). Если изготовить блоки из арболита необходимо в небольших объемах, то можно воспользоваться специальным мини-станком. Если речь идет о промышленных масштабах, то используют целые линии по производству арболитовых блоков, которые включают в себя станки для изготовления блоков, прессы и смесители.
Так выглядит линия по производству арболитовых блоковЛучший процесс затвердения достигается путем использования тепловых камер с ТЭНом, ИК-излучением и т. д. В них можно контролировать необходимую температуру и уровень влажности.
Формы для блоков
Формы для производства арболитовых блоков могут быть следующих размеров: 20 см*20 см*50 см или 30 см*20 см*50 см. для строительства конструкций из арболитовых блоков формы могут выпускаться и других размеров (для перекрытий, вентиляционных систем и т. д.).
Формы для блоков можно купить, а также можно изготовить своими руками. Для этого понадобятся доски толщиной 2 см, которые сбиваются в необходимую по размерам форму. Внутренняя часть обшивается фанерой и сверху пленкой или линолеумом.
Схема по изготовлению формы для арболитовых блоков
Как сделать арболитовые блоки своими руками
Список оборудования:
- Разъемная форма и вставки для нее;
- Падающий и вибростол;
- Установка для подъема формы;
- Ударно-встряхивающий стол;
- Лоток для смеси;
- Поддон для формы из металла.
Имея все необходимое оборудование для производства блоков, можно получать 300-400 м3 стройматериала в месяц. При этом площадь для установки всего оборудования потребуется около 500 кв. м и затраты на электроэнергию 10-40 кВт/ч.
Изготовление больших блоков требует их дополнительного армирования. Когда форма заполнена на половину арболитовой смесью, сверху заливается слой бетона с арматурой, после этого продолжается заполнение арболитом.
При самостоятельном изготовлении блоков из арболита органические вещества необходимо залить водой, после чего – цементом до однородного состояния. Для этого потребуется 3 части цемента, 3 части опилок или древесной стружки и 4 части воды. Получившаяся смесь должна быть сыпучей и в тоже время удерживать форму при сжатии в руке.
Перед заливкой внутренняя часть формы смазывается известковым молочком. После этого можно выкладывать подготовленную смесь слоями с тщательной утрамбовкой. Поверхность блока выравнивается шпателем и заполняется штукатурным раствором на высоту 2 см.
Видео о том, как осуществляется производство арболитовые блоки своими руками:
Рекомендации
- Уплотнить смесь можно при помощи дерева, обитого железом.
- Наибольшей прочностью обладают блоки, которые находились под пленкой во влажном состоянии около 10 дней. При этом температура воздуха не должна быть ниже 15 градусов.
- Предотвратить пересыхание блоков можно, периодически поливая их водой.
Достаточно просто самостоятельно изготовить данный строительный материал. Если соблюдать все технологии, то конечный продукт будет прост в применении, обладать высокой прочностью, пожаробезопасностью и длительным сроком эксплуатации.
Понравилась статья? Поделитесь с друзьями в социальных сетях:Вконтакте
Одноклассники
Google+
И подписывайтесь на обновления сайта в Контакте, Одноклассниках, Facebook, Google Plus или Twitter.