Композиты и бетон, фибробетон, армированный волокнами и композитной арматурой бетон
Перевод и редакция: Третьяков Павел Андреевич
Преимущества композитных материалов отлично проявляются в строительстве и при армировании бетона.
Бетон является недорогим и многогранным строительным материалом, который используется во многих приложениях. В этой статье дана информация о том, как сделать бетон стойким к различным внешним воздействиям и нагрузкам, что позволит обеспечить его длительное функционирование.
Бетон является истиным композитом и состоит из гравия и песка, которые связаны между собой при помощи цемента, а металлическая арматура обычно добавляется для усиления прочности бетона. Бетон великолепно ведет себя при нагрузках на сжатие, но при растяжении становится хрупким и непрочным. Растягивающие напряжения, как и усадка бетона во время отверждения, приводят к появлению трещин, в которые попадает вода. Это в свою очередь приводит к коррозии металлической арматуры, ее разрушению и существенной потере целостности бетона.
Композитная арматура обладает великолепным сопротивлением к коррозии, благодаря чему она прочно утвердилась на строительном рынке. Источник: Hughes Bros. |
Пластики, усиленные волокнами (базальтопластик и стеклопластик) уже давно рассматриваются в качестве материалов, позволяющих улучшить характеристики бетона. Институт Бетона Америки и другие группы, такие как Японское Сообщество Гражданских Инженеров, помогли разработать спецификации и методы тестирования материалов на основе усиленных волокнами пластиков, многие из которых уже допущены к использованию и прочно закрепились в строительстве, где используется бетон и бетонные конструкции. «В дополнение к конструкторским документам теперь есть и методики тестирования материалов», — говорит Джон Бюсел, председатель
Композитная арматура и изготовленные из нее армирующие сетки находят применение в различных приложениях. Также уже разработаны материалы на основе усиленного волокнами бетона, материала, в котором для армирования используются стальные или полимерные волокна. Такие усиленные волокнами бетоны (фибробетоны) используются при изготовлении настилов, напольных плит и сборных конструкционных частей.
КОМПОЗИТНАЯ АРМАТУРА
За последние 15 лет композитная арматура прошла путь от экспериментальных прототипов до эффективного заменителя стали во многих приложениях. «Стеклопластиковая арматура используется очень часто, и это весьма конкурентный рынок», — говорит Дуг Гремел, руководитель направления армирования неметаллами компании
Для некоторых проектов, таких как оборудование для магниторезонансной томографии в больницах, или пункты взимания дорожной платы, где используется радиочастотная идентификация определения уже оплативших покупателей, единственно доступным материалом является композитная арматура. Использовать стальную арматуру не представляется возможным, т.к. она взаимодействует с электромагнитными сигналами, генерируемыми оборудованием. Композитная арматура, в отличие от стальной, обладает электромагнитной прозрачностью и необычайной стойкостью к коррозии, кроме того композитная арматура легкая – ее вес составляет около одной четверти от веса аналогичной стальной арматуры, а теплоизоляционные свойства композита препятствует протеканию тепла в стройконструкциях. Два самых крупных производителя композитной арматуры — компания
Для производства композитной арматуры обычно используется технология пултрузии, где армирующим наполнителем является ровинг из Е-стекла, а связующим винилэфирная смола. Продукты марки
Т.к. механические свойства стекла отличаются от свойств стали, структура бетона с применением композитной арматуры разрабатывается в соответствии с
Арматура марки V-ROD компании Pultrall поставляется в США эксклюзивно фирмой Concrete Protection Products Inc.
Мост O’Fallon Park в Колорадо был спроектирован полностью из композитной арматуры вместо традиционной стальной арматуры, и имеет монолитное композитное мостовое плотно. Источник: Hughes Bros. |
Арматура из стеклопластика марки Aslan 100 от компании Hughes Bros. недавно была использована в бетонном мосту в Морисон, штат Колорадо, который был построен Департаментом Перевозок Колорадо при поддержке Города и Графства Денвер Паркс и Департамента Восстановления. При строительстве моста общей длиной 13.8 метра, который перекрывает Бир Крик, стеклопластиковая арматура использовалась в основаниях, опорах, откосных стеновых крыльях, парапетах и изогнутой монолитной бетонной арке. Цельная композитная плита, установленная наверху бетонной арки, была сделана компанией
Есть предположение, что рынок композитной арматуры станет еще более конкурентоспособным при использовании нового материала – базальтового волокна. Грахам Смит, исполнительный вице президент компании Sudaglass Fiber Technology (Хьюстон, Техас), производителя базальтового волокна, производство которого расположено в России и на Украине, говорит, что компания уже имеет задел на производственных мощностях в северном Техасе. По словам Смита, композитная арматура из базальтового волокна и эпоксидной смолы сейчас производится при помощи пултрузии на Украине, и находится в процессе сертификации для использования в строительстве в США.
Обладая лишь немного более высокой плотностью, чем стеклянное волокно, базальтовое волокно имеет существенно более широкий диапазон рабочих температур — от -260°C до 982°C, в то время как номинальный рабочий диапазон стеклянного волокна составляет от -60°C до 650°C. Температура плавления базальта — 1450°C, что делает его пригодным для использования в приложениях, требующих стойкости к огню. Как замечает Смит, базальт обладает превосходной стойкостью к щелочной составляющей в бетоне без использования специальных сортировок по размеру, которые используются для защиты стеклянного волокна.
Каким бы не был выбор армирования, композитная арматура, вероятно, обладает наибольшей привлекательностью для лиц,ответственных за принятие проекта. «Хорошим практическим результатом для инженера или конструктора, который решает проблему коррозии, является то, что при 5-7% увеличении затрат на материалы с использованием композитной арматуры вы продлеваете срок эксплуатации структур на 10-20 лет», — подводит итог Гремел.
СЕТКИ ИЗ КОМПОЗИТНОЙ АРМАТУРЫ В СБОРНЫХ БЕТОННЫХ ПАНЕЛЯХ
С момента первого доклада CT об использовании в сборных бетонных конструкционных панелях полимерных сеток, усиленных волокнами («Composite Solutions Meet Growing Civil Construction Demands,» CT August 2002, p. 40), рынком был показан значительный рост, говорит Бюсел. «Область этих применений огромна и здесь существует огромный потенциал», — утверждает он.
Данное направление возглавляется группой AltusGroup, которая является консорциумом пяти производителей сборных бетонных панелей и производителя арматуры, компании TechFab LLC (Anderson, S.C.). Группа была сформирована специально для продвижения технологии CarbonCast, где в качестве вторичного армирования для замены традиционной стали или арматуры в сборных структурах применяются недавно разработанные углеродно-эпоксидные сетки C-GRID. TechFab — это долевое 50/50 объединение компании Hexcel (Дублин, Калифорния) и компании Chomarat Group (Le Cheylard, Франция). До настоящего времени членами AltusGroup являются Oldcastle Precast (Edgewood, Md.), HIGH Concrete Structures (Denver, Pa.), 2 компании, владельцем которых является Cretex Companies (Elk River, Minn.), и Metromont Prestress (Greenville, S.C.), но в группу также могут быть приняты новые участники в связи с возрастающим объемом продаж, говорит Джон Карсон, руководитель коммерческого развития TechFab и глава программы технологий C-GRID.
C-GRID является крупной сеткой из углепластиковой арматуры — материала на основе углеродных волокон и эпоксидной смолы. Используется как замена вторичной стальной армирующей сетки в бетонных панелях и архитектурных приложениях. Размер сетки меняется как в зависимости от бетона и типа заполнителя, так и от требований к прочности панели. Источник: AltusGroup |
AltusGroup предлагает ассортимент продукции на основе CarbonCast, который включает конструкционные и не строительные изолированные панели и наружную облицовку. C-GRID обычно заменяет вторичные армирующие элементы на основе сетки из стальной арматуры. В качестве первичного армирования по-прежнему во многих случаях используется обычная стальная арматура. C-GRID производится в запатентованном квази-тканном технологическом процессе, при котором в открытой структуре совмещается наложенние основы и утка углеродных волокон, смоченных высокореакционной эпоксидной смолой. Размеры ячейки сетки изменяются в диапазоне от 25.4 мм до 76 мм, конечный размер зависит от требований к прочности панели, типа бетона и размера наполнителя. В процессе производства сетки ее поверхности придается шероховатость для улучшения прочностных связей с бетоном. В линейке продукции C-GRID компании TechFab также есть композитные сетки, содержащие стеклянные, арамидные или полимерные волокна в сочетании с любым ассортиментом смол. Композитные сетки, как содержащие, так и не содержащие углеродные волокна, находят применение в различных областях строительства, таких как декоративные элементы, монолитные бетонные конструкции, ремонт или восстановление.
Панели CarbonCast имеют существенные преимущества, говорит Карсон. Сетки C-GRID гораздо более легкие чем стальные, и обладают свойствами растяжения почти в 7 раз лучшими, чем сталь. Вероятность разломов бетонных конструкций вследствие усадки при высыхании существенно снижена, кроме того C-GRID не корродирует, благодаря чему на поверхности бетонных панелей не возникают коррозионные пятна, характерные для бетонных панелей, армированных стальной арматурой. Коррозийная стойкость композитных сеток позволяет использовать бетонное покрытие толщиной всего 6.35 мм, в то время как может потребоваться до 76.2 мм бетонного покрытия для защиты стальной сетки от воздействия влаги. Таким образом, вес бетонной панели может быть уменьшен на 66% по сравнению с обычными панелями, армированными только стальной арматурой. Более легкие панели позволяют снизить общий вес стены, благодрая чему требуется меньше стальной подструктуры. Это позволяет значительно снизить затраты на строительство конструкций. Сетка C-GRID также слабо проводит тепло, так что величина тепловой изоляции панели не меняется. Более того, в панелях с сеткой C-GRID могут быть прорезаны отверстия непосредственно на месте работ, что невозможно сделать при использовании стальной сетки для армирования. Все эти преимущества композитных сеток в итоге выражаются в снижении расходов на транспортировку и строительство конструкций.
На сегодняшний день было продано более 3 млн. кв. футов панельной продукции CarbonCast и спрос так высок, что TechFab недавно анонсировала строительство новой фабрики, которая вместит добавочную линию по производству сетки. Это, по словам Карсона, должно быть сделано в октябре этого года. Анонсируемые планы соответствует долговременному соглашению с компанией Zoltek Corp. (St. Louis, Mo.), являющейся поставщиком волокна Panex 35, которое используется в C-GRID. По словам Карсона, это соглашение обеспечит последовательные поставки для C-GRID во время первых лет запуска продукции. «Компания Zoltek была нашим первым поставщиком волокон и партнером с первого для этого проекта», — заметил Карсон.
Сборные панели использовались в различных проектах, таких как кинотеатры, церкви и парковочные гаражи. Последним проектом был офисно-складской комплекс Cardinal Health рядом с Балтимором площадью 332 000 кв. футов. Для этого проекта были отлиты панели CarbonCast длиной до 15.5 метров, используемые для формирования двухэтажных наружных вертикальных стен здания. Каждая панель является сэндвич структурой с изоляционным слоем пены толщиной 152 мм между облицовочными панелями, состоящими из наружной кирпичной перегородки толщиной 50 мм (бетонный слой) и внутренней кирпичной перегородки толщиной 100 мм. Сетка C-GRID, расположенная перпендикулярно к поверхностям панелей, соединяет внутреннюю и наружную облицовки, обеспечивая усиление на срез.
ФИБРОБЕТОН — АРМИРОВАННЫЙ ВОЛОКНАМИ БЕТОН
Фибробетон (бетон, в который для улучшения свойств введены короткие волокна — фибры) отлично зарекомендовал себя на протяжении десятилетий, и даже столетий, если учесть, что еще в Римской Империи строительные растворы готовили с добавлением конского волоса. Использование волокон в бетоне (армирование) усиливает его прочностные и упругие свойства за счет удерживания части нагрузки и предотвращения роста трещин при повреждении матрицы бетона. Доктор Виктор Ли из Университета штата Мичиган исследовал свойства высокоэффективных цементных композитов, армированных волокнами, которые являются чрезвычайно высокоэффективными подгруппами фибробетона. Виктор Ли считает, что признание этого материала будет расти, если будут сохранены его механические характеристики, низкая стоимость и простота получения.
«Использование фибробетона может привести к отказу от использования арматуры, работающей на срез, что в свою очередь приведет к снижению материальных и трудовых затрат», — говорит Виктор Ли. «Прореживаемая фибрами структура позволяет снизить объем материала и вес, что делает транспортировку фибробетона более легкой. Общее снижение затрат по этим статьям может легко оправдать расходы на использование материала, армированного волокнами».
Официальное признание фибробетона за последние пять лет способствовало подготовке стандартов и руководств по его использованию (смотрите CT July/August 2001, p. 44). С этого времени начался расцвет коммерческих приложений фибробетона.
Компания Lafarge SA (Париж, Франция), которая является гигантом стройтельной индустрии и материалов, вот уже около 10 лет продвигает свой высокоэффективный фибробетон под торговой маркой Ductal, нацелившись на широкий сегмент гражданского строительства. Ductal является смесью цемента, кварцевой крошки, кварцевой муки, мелкого кварцевого песка, пластификаторов, воды и стальных или полимерных волокон, обычно длиной 12 мм. Вик Перри, вице президент компании и генеральный директор направления Ductal, говорит, что специально подобранная комбинация мелкозернистых порошков создает максимальную плотность при отверждении бетона, что выражается в полном отсутствии пор и фактически исключает доступ влаги в матрицу бетона и предотвращает коррозию стальных волокон. Фибробетон с волокнами из поливинилового спирта обычно используется в архитектурных и декоративных приложениях, что предотвращает вероятность поверхностного травления, которое может проявится при коррозии стальных волокон в бетоне. Кроме того, это позволяет удалить абразивность в местах, где предполагается контакт человека с поверхностью бетона. Производителям изделий из бетона и поставщикам растворов материалы поставляются в мешках.
«Добавление волокон улучшает пластическую деформацию материала и позволяет ему выдерживать растягивающие нагрузки», — говорит Перри. «Волокна усиливают прочность и улучшают микроструктурные свойства бетона».
Выдерживаемые материалом Ductal нагрузки на сжатие зависят от типа используемых волокон и варьируются от 150 МПа до 200 МПа. У стандартного бетона эта величина составляет 15-50 МПа. Доказанная прочность на изгиб материала Ductal составляет 40 МПа, говорит Перри. Фибробетон Ductal, в котором использовались стальные волокна производства Lafarge’s Forta steel fibers, применялся для сборного строительства и при производстве нескольких предварительно напряженных мостовых балок. В месте Saint Pierre La Cour, Франция, 20-ти метровый грузовой мост был построен с применением 10-ти балок I-типа, изготовленных их материала Ductal, которые поддерживают монолитную бетонную плиту, изготовленную с применением традиционного армированния стальной арматурой толщиной 170 мм. Сборные балки, изготовленные без арматуры, были заглублены на 600 мм и предварительно напряжены при помощи стальных плетеных кабелей толщиной 13 мм, размещенных в нижней кромке. По технологии напряжение прикладывается к кабелям до того, как Ductal заливается в форму балки. Как только бетон покрывает кабели и материал начинает твердеть, кабели обрезаются, что фактически прикладывает напряжение сжатия к бетонной смеси.
Если подвергнуть предварительно напряженную балку любому изгибу, объясняет Перри, она не будет испытывать растягивающих нагрузок, а просто «разожмется», что значительно улучшит ее характеристики. Благодаря прочности фибробетона Ductal, балки из него не требуют армирования арматурой, что значительно снижает их вес.
Структуры, изготовленные из фибробетона Ductal, и имеющие в сечении форму греческой прописной буквы «?» (по сути балки коробчатого сечения без нижней кромки), используются как настил и как балки экспериментального моста на тестовом пути Лаборатории Федеральных Магистралей США, что позволяет проводить исследования пригодности конструкции для строительства будущих высокоскоростных трасс. Балка-настил «?»-типа имеет конструкцию, которая позволяет выдерживать нагрузки, определенные Американской Ассоциацией Государственных Магистралей и Перевозок.
Для изготовления этих предварительно напряженных мостовых балок на тестовом пути был использован фибробетон. Благодаря высокой эластичности и прочности материала, полученного из бетона, армированного стальными волокнами, использование арматуры не потребовалось. Источник: LaFarge |
«Балки из фибробетона Ductal имеют большую протяженность при весе, сходном с балкой из обычного бетона», — говорит Перри. «В итоге, мы увидим использование фибробетона в балках и мостовых настилах».
Компания SI Concrete Systems. (Chattanooga, Tenn.) является производителем армирующих волокон для бетона. SI предлагает волокна марки Novomesh, Fibermesh и другую фибро продукцию. Эти материалы используются в качестве альтернативы вторичной армирующей сетки стальных нитей и легкой арматуры как в офисных, так и в жилых приложениях, говорит Хал Пэйн (Hal Payne), руководитель стратегических соединений компании SI Concrete Systems. SI производит полипропиленовые волокна, стальные волокна, макросинтетические волокна и промышленные смеси. По словам Пэйна, материалы на основе полипропиленовых волокон необходимы для контроля ранней стадии образования трещин, которые возникают из-за пластической усадки бетона, и для предотвращения роста этих трещин и образования больших щелей во время высыхания бетона. Novomesh 950 является новым продуктом компании и представляет собой смесь необработанных макросинтетических и специально отобранных фибрилированных микросинтетических волокон. Пэйн говорит, что использование этого продукта дает такие же хорошие результаты, как и использование стальных волокон в бетоне, предназначенном для плит перекрытий.
Компания Kingspan (Sherburn, Malton, N. Yorkshire, U.K.), специалист в строительстве с применением бетона, использует фибро добавки для бетона производства Bekaert Building Products (Friedrichsdorf, Germany). Формованные стальные волокна Dramix от компании Bekaert добавляются в бетон при производстве полов и кровель без использования армирующих стальных сеток. Этот продукт идеален для строительства в сжатые сроки — т.к. бетон не требует армирования стальной сеткой, изначально нет необходимости ее закупать и отсутствуют все трудозатраты, связанные с доставкой рулонов арматуры, ее резкой и установкой в многоэтажном здании до операций по заливке бетона. Полы из фибробетона могут быть установлены в единой цикле — для этого надо только доставить армированный волокнами материал прямо к каждому полу.
Методические указания и допуски для фибробетона теперь даны в конструкторских руководствах разных стран, что является значимым показателем в признании фибробетона конструкторами, инженерами и ответственными лицами. «Использование фибробетона позволяет реализовать такие преимущества, как быстрота строительства, улучшенный внешний вид, отличная упругость и стойкость к коррозии», — говорит Перри. «Все это выражается в снижении расходов на обслуживание и более длительном времени эксплуатации структур».
Статья из журнала «Composites Technology», апрель 2005
Преимущества полимербетона перед другими материалами: Обзор +Видео
Характеристики полимербетона – чем он лучше обычного бетона. В наше время развития строительных технологий появляется множество новых материалов, а также бетонные смеси, для приготовления которых часто используют особые наполнители. Это дает возможность создавать прочные материалы композитного типа, которые имеют высокие эксплуатационные характеристики и прекрасные декоративные свойства.
Полимербетон является именно таким составом, который смог в рекордно короткие сроки завоевать популярность на рынке со строительным сырьем.
Общие сведения
Обратите внимание, материал вместе со стандартными составляющими – щебнем и песком, включает в свой состав вяжущее вещества вроде полимерные смол на фурановой, эпоксидной и полиэфирной основе. Полимерный бетон крайне востребован в области строительства, а еще его используют для того, чтобы создавать скульптуры, делать оригинальную мебель, а еще часто используют в ритуальной сфере.
Полимербетон (полимерценмент, литьевой камень, пластобетон, пластбетон, бетонополимер) был создан в Америке в качестве более прочно и долговечной альтернативы стандартному бетону. Полимерная разновидность материала имеет множество более серьезных достоинств, которые связаны с улучшенными механическими характеристиками (по сравнению с обычным бетоном), устойчивостью с агрессивным химическим средам, легкостью, большой цветовой палитрой, которая дает возможность делать имитацию под натуральный камень. Потребители композитного материала смогли убедиться в том, что данный состав надежен, имеет большую область применения. Давайте подробнее рассмотрим, вникнем в технологию изготовления, оценим все преимущества и недостаткам материала, а также изучим подробнее рецептуру.
Достоинства материала
Интересно, что композитная разновидность бетона за счет рецептурным особенностям имеет ряд положительных характеристик. Они используются во множестве различных ситуаций, где использование стандартного бетона не сможет обеспечивать желаемый результат.
Главные достоинства материала композитного происхождения:
Повышенный уровень устойчивости к попаданию влаги внутрь композитного массива. Капли воды будут быстро испаряться с поверхности материала, и при этом не будут успевать насытиться его разрушительной влагой.
- Устойчивость к большим перепадам температуры, которая дает возможность сохранять полимерному бетону целостность вне зависимости от того, какова продолжительность заморозки и сколько было циклов «замерзание-оттаивание». Этот материал представляет собой одну из разновидностей смесей бетонного типа, в которую вместо цемента или силиката (которые используют для изготовления стандартного бетонного материала) применяют полимеры.
- Устойчивость материала к веществам агрессивного действия, химическим реагентам любого происхождения, что позволяет использовать полимербетон в разных областях без защиты поверхности при помощи особых покрытий.
- Есть возможность восстанавливать поврежденные участки из-за механического воздействия путем использования реставрационной смеси для композитного массива.
- Повышенные характеристики полимербетона по прочности при относительно небольшой массе. Это дает возможность создавать различную продукцию, которая имеет расширенные эксплуатационные свойства.
- Отсутствие шероховатостей на гладкой, идеальной и совсем нескользкой поверхности материала. Такое свойства дает возможность камню искусственного происхождения на протяжении долгого времени оставаться чистым, а при необходимости можно без труда удалить различные типы загрязнений с поверхности материала.
- Огромная цветовая гамма бетона полимерной разновидности, которая дает возможность имитировать камень натурального происхождения, гранит и малахит. Изготовленный искусственный камень очень сложно отличить от настоящего, и это дает возможность обеспечивать композиту широкую сферу применения.
- Есть возможность выполнить вторичную переработку, которая используется при изготовлении отходов технологического характера, а это помогает в ощутимой мере снизить себестоимость продукции, которая выпускается при использовании безотходной технологии.
Кроме того, к плюсам стоит отнести малый вес, стойкость к ударам, а упругость намного выше, чем у стандартного бетона.
Недостатки
Вместе со множеством положительных моментов у полимерного бетона есть определенные недостатки:
- Восприимчивость к воздействиям от открытого огня, а также повышенная температура, которая способна вызывать разрушение материала.
- Куда выше стоимость (если сравнивать с обычным бетоном), потому что это обусловлено затратами на покупку особых смол, которые входят в состав.
Хотя недостатки есть, и об этом говорится открыто, их намного меньше, а значит, можно с полной уверенностью говорить о том, что материал отличный и изделия из полимербетона прослужат вам долгие годы.
Компоненты, входящие в состав
Если вы желаете сделать полимербетон в домашних условиях, то стоит для начала изучить состав композита.
Для того, чтобы приготовить самостоятельно полимербетон, следует использовать такие ингредиенты:
- Связующий компонент, в качестве которого используют полиэфирные, карбамидоформальдегидные, фурфуролацетоновые и эпоксидные смолы.
- Щебеночный крупнофракционный наполнитель. Размер фракции щебень, требуемый для того, чтобы сделать композит, может составлять до 4 см, но щебень, имеющий размер в 1-2 см должен составлять большую часть от общего состава.
- Кварцевый песок, который был предварительно очищен и просеян. Крупность частиц кварца не должна быть больше 0.5 см, и ни в коем случае не допускается наличие глинистых включений, а также пыли. Для полистиролбетона, в качестве заполнителя которого используют полистирол, есть свои, несколько иные стандарты.
Ингредиент | Составы предложенного полимербетона, масса в % | Прототип | ||||
1 | 2 | 3 | ||||
Смола эпоксидная | 5,4 | 4,76 | 4,76 | 5.2-5.21 | ||
Полиэтиленполиамин | 0,81 | 0,71 | 0,71 | 1,04 | ||
Лак КО-916К | — | — | — | 0.03-0.16 | ||
Лак КО-922 | 0,09 | -,08 | 0,16 | — | ||
Наполнитель минерального типа | 21,77 | 19,19 | 19,17 | 93,6-93,72 | ||
Заполнитель | 71,93 | 75,26 | 75,19 | — |
- Измельченный графитовый порошок, крупность которого не больше 0,015 см, мука кварцевая – при применении их в качестве молотого наполнителя потребность в использовании дорогостоящих смол отпадает или хотя бы частично сокращается.
- Гипс строительной разновидности, используемый при наличии в рецептуре композита смолы карбамидоформальдегидного типа.
- Поверхностно активные вещества, ингредиенты, увеличивающие объем массива и добавки с антисептическими свойствами помогают повысить теплоизоляционные свойства готового композитного бетона.
Теперь стоит рассмотреть подробную классификацию.
Классификация
Полимерный бетон в зависимости от того, какая у него концентрацию наполнителя, доля которого во всем объеме составляет до 4/5, может быть разделена на классы:
- Особо тяжелый композитный материал, его 1 метр кубически будет весить от 2.5 до 4 тонн.
- Тяжелый, плотность материала составляет от 1.8 до 2.7 на 1 м3.
- Легкий, который имеет удельный вес от 0.5 до 1.8 тонны на 1 м3.
- Облегченный, причем его масса на 1 метр кубический не больше 0.5 тонны.
Прежде чем рассмотреть технологию полимербетона, следует узнать подробнее, где его используют.
Область применения
Полимерный композитный материал используется для различных областей, а также является прекрасной основой для того, чтобы создавать различные виды изделий:
Столешницы, которые стаи невероятно популярны в последнее время, используемые в кухонном пространстве как модный аксессуар. Изделия достаточно практичные, гигиеничные, имеют высокий эксплуатационный ресурс, прекрасно гармонируют с помещением. При визуальном осмотре изделие, сделанное из композита, будет сложно отличить от минерала естественного происхождения. Устойчивость к механическим воздействиям у композита куда выше, чем у камня природного происхождения.
- Покрытия для поверхности пола, которые отличаются тем, что их очень удобно мыть и можно выполнить ускоренную установку. Покрытия характеризуются высокой практичностью, устойчивость к воздействиям от нагрузок ударного типа, а также малыми затратами, которые связаны непосредственно с монтажными работами. Длительный эксплуатационный срок дает возможность при толщине слоя до 0.2 см использовать материал 10 лет.
- Элемент для декорирования, который прекрасно используется для фасадных конструкций. Полимербетон достаточно сложно отличить от гранита натурального происхождения или мрамора, который он с успехом имитирует. Благодаря небольшому весу полимерных изделий нет необходимости возводить усиленное укрепленное основание, а также делать дополнительное укрепление конструкции. Также материал совсем невосприимчивый к температурным воздействиям и уровню влажности, его можно легко установить, долговечный и имеет оригинальную фактуру.
- Памятники и конструкции для ограждения, которые используют для ритуальных услуг. Устойчивость полимерного массива к воздействию факторов погодного типа с сохранением целостности помогает обеспечивать популярность композитного бетона, используемого для ритуальных услуг. Идеально гладкая и блестящая поверхность продукции дает возможность изделиям сохранить красивый внешний вид, при этом находясь в открытом виде при любых погодных условиях.
Из полимербетона можно сделать лестницы, полы, облицовочную и тротуарную плитку, строительные конструкции, скульптуры и водоотводные лотки, памятники, даже фонтаны!
Более того, изготовление по технологии полимербетона дает возможность использовать его для создания:
- Перильных ограждений.
- Подоконников.
- Балясин.
- Поручней.
- Лестничных маршей.
- Лепных изделий для декоративного украшения.
- Опорных колонн.
- Лестничных маршей.
- Моек.
- Элементов для каминов.
А теперь рассмотрим, как делают этот материал.
Этапы изготовления
Технология создания полимерного композитного бетона и изготовление продукции будет предусматривать такие этапы:
- Подготовка всех компонентов.
- Смешивание.
- Формирование.
Рассмотрим все по отдельности. Во время изготовления материала самым главным является оптимальный подбор всех компонентов, которые будут соответствовать назначенной цели.
Как подготовить все компоненты
Когда вы ознакомитесь с составом композита, подготовьте все составляющие для того, чтобы выполнить замешивание:
- Очистите все от инородных добавок, промойте гравий, который будет играть роль заполнителя.
- Просейте кварцевый песок.
- Просушите фракцию, чтобы удалось обеспечивать концентрацию влаги до 1%.
Как делать смесь?
Изготовление смеси
Полимерный состав следует готовить по предложенному алгоритму:
- Поместите щебень в миксер, а также добавьте кварцевый песок и заполнительный ингредиент, при этом соблюдайте последовательность, предложенную в инструкции.
- Смешайте компоненты, причем процесс должен длиться примерно 2 минуту, добавьте горячую воду и выполните повторное смешивание.
- Размягчите связующий компонент при помощи такой добавки, как растворитель.
- Введите пластификатор внутрь смолы, хорошенько смешайте.
- Размешайте связующие вещества с заполнителем, введите компонент для отвердевания.
- Тщательно смешивайте состав примерно 3 минуты.
Теперь, когда состав готов, следует сразу ж приступить к заливке, так как материал имеет свойства быстро затвердевать.
Заливка
Выполняйте работы и при этом соблюдайте следующее последовательность:
- Нанесите смазочное масло на поверхность формы или же используйте вместо него технический вазелин, что поможет исключить прилипание.
- Заполните при помощи композита емкость, выровняйте поверхность.
- Уплотните раствора на площадке вибрационного типа.
- Готовое изделие можно достать через сутки, не ранее.
На этом инструкция заканчивается, остается лишь радоваться плодам своих рук.
Заключение
Теперь, когда вы сами знаете обо всех технологии полимербетона, вы сможете самостоятельно делать композитный материал. Если вы в чем-то сомневайтесь, прочтите информацию еще раз, так как это консультация профессиональных строителей, которая поможет избежать ошибок.
Композитный бетон способен накапливать тепловую энергию
В строительстве широко используется способность некоторых материалов впитывать, сохранять и выделять накопленное тепло. В качестве примеров можно привести воду в качестве теплоносителя систем отопления и кирпичную кладку обыкновенной печи, которая долго согревает дом после того, как очаг уже давно погас.
Сберегающий тепло
Причём вода является классическим примером способности некоторых соединений впитывать и отдавать огромные объёмы тепловой энергии, не изменяя при этом температуры. Такое происходит во время фазовых переходов Газ — Жидкость — Лёд. Это три основных состояния, или фазы, с которыми большинство знакомо со школы (технически есть ещё и четвёртое, плазменное состояние, когда вода реагирует на электромагнетизм, то есть молнию).
Схожей с водой способностью захватывать и хранить тепло имеет парафиновый воск. Для него также характерны фазовые переходы, однако происходят они при куда менее экстремальных температурах. Когда температура поднимаются, воск начинает переходить в жидкую фазу, попутно поглощая тепло. Когда температура падает, парафин снова затвердевает и высвобождает тепловую энергию обратно.
Разнообразные изобретения, использующие данные физические свойства парафина, присутствуют на строительном рынке уже почти десяток лет. Так что само изменение фазы материала не является совершенно новой концепцией. Новизна заключается в том, что подобную способность придали такому консервативному материалу, как бетон.
Новый композитный материал для хранения тепловой энергии, был интегрирован в цементные композиты. Исследователи создали защитное покрытие — своеобразную «оболочку» из вспученного перлита, которая оборачивает парафин, останавливает его утечку и препятствует его контакту с другими компонентами бетона. Капсулы имеют размер всего 2-20 мкм и описываются как «механически практически не разрушаемые» без потери функции теплообмена при разрезах или сверлении бетонных конструкций.
Бетоны с добавками от 20 до 80 процентов фазового материала были подвергнуты стандартным испытаниям на сжатие. Было выяснено, что замена 60% бетонной смеси на композит значительно улучшает его термические способности при сохранении механической прочности. При этом существенно уменьшается его плотность. То есть получаем лёгкий бетон со стандартными конструкционными параметрами и необычными тепловыми характеристиками.
Это предоставляет возможность хранения достаточного количества тепловой энергии, обеспечивающей тепловую инертность (стабильность) внутри здания. Например, можно обходиться без систем кондиционирования. Скажем, задать материалу номинальную температуру в 21, 23 или 25°С. По её достижении в жаркий день излишки тепла будут поглощаться стенами и перекрытиями, стабилизируя комфортный микроклимат. Ночью же происходит обратный процесс. Или, что нам ближе и понятнее, днём конструкции накапливают тепло, а ночью запускают его на «обогрев» дома.
Конечно, подобное решение не сможет полноценно заменить климатическую систему. Однако, учитывая простоту, неприхотливость и ненужность какого-либо дополнительного обслуживания и связанных с этим затрат (пусть не обычный, но всё же бетон), рациональное зерно присутствует. В любом случае, изобретению пророчат блестящие перспективы в плане энергосбережения.
Источник: tateinc.com
состав, характеристики и технология изготовления
В строительной отрасли внедряются прогрессивные технологии и используются новые материалы. Один из них – фибробетон. Не все знают, что это композит, отличающийся от бетона повышенной прочностью. Материал содержат специальные волокна, которые пропорционально распределены в бетонном массиве, выполняя функцию арматуры. Применение фибры стандартных размеров, изготовленной из металла или синтетических материалов, существенно повышает прочностные характеристики. Разберемся, что такое фибробетон. Остановимся на свойствах материала, технологии изготовления.
Что такое фибробетон
На вопрос, что такое фибробетон, многие затрудняются дать правильный ответ. Что это такое? Материал является разновидностью традиционного бетона, усиленного путем добавления в бетонную смесь фибры. Для бетонного состава характерна пониженная зернистость, а также равномерная концентрация в массиве различных видов армирующих элементов:
- металлического наполнителя в виде стальной проволоки, которая может иметь разную конфигурацию и размеры;
- синтетической фибры, изготовленной из базальтового волокна, стеклянных нитей, асбеста, полиамидного наполнителя или акрила.
Обеспечение повышенных прочностных характеристик достигается путем введения в состав металлических волокон. Их диаметр не превышает полмиллиметра, а длина элементов составляет от 1 до 5 см. Стальная проволока – наиболее популярная разновидность наполнителя. Одновременно с ней растет популярность стеклянных волокон и различных наполнителей на основе полипропилена.
На рынке стройматериалов предлагают новый материал – фибробетонНасыщение бетонного массива наполнителем улучшает эксплуатационные характеристики композита:
- прочностные свойства;
- устойчивость к воздействию растягивающих усилий;
- стойкость к образованию трещин.
Технология изготовление стройматериала позволяет одновременно использовать различные виды фибры:
- вискозное волокно;
- нейлоновые материалы;
- хлопчатобумажные нити.
Они повышают эффективность армирования, позволяют достичь новых характеристик без увеличения себестоимости производства. Тип применяемых волокон и их концентрация влияют на прочность бетона. В строительной отрасли распространен фибробетон с маркировкой В25. Увеличенный запас прочности достигается путем смешивания стальной проволоки со стеклянными волокнами.
Эксплуатационные свойства материала
Выбирая композит для решения специальных задач в строительной сфере важно разбираться, что такое фибробетон, какие свойства для него характерны. Повышенные прочностные характеристики композитного бетона обеспечивают возможность возведения из него зданий, которые имеют повышенную устойчивость при пониженной толщине капитальных стен. Специалисты уверены, что это снижает объем расходов на постройку объекта. Проверенная на практике рецептура применяется при изготовлении бетонного композита. Вид используемой фибры влияет на эксплуатационные свойства.
Эти волокна исполняют роль арматуры, которая применяется с целью повышения прочности бетонного раствораГлавные характеристики композитного бетона:
- способность массива сохранять целостность под влиянием значительных растягивающих нагрузок;
- нейтральность к воздействию агрессивных веществ, стойкость к влиянию природных факторов;
- морозостойкость с сохранением структуры массива при многократных и резких колебаниях температуры;
- устойчивость к интенсивному нагреву, обусловленному воздействием высокой температуры и открытого огня;
- сохранение исходного объема массива, после набора твердости не вызывающего усадку;
- стойкость к абразивному износу, истиранию, растрескиванию, воздействию крутящих моментов;
- влагостойкость, обусловленная своеобразной структурой, которая затрудняет проникновение влаги вглубь композита;
- увеличенная пластичность бетонного массива, повышенная прочность к воздействию ударных нагрузок.
Благодаря указанным свойствам, материал применяется для решения широкого круга задач в строительной отрасли.
Область применения
Введение в бетон различных типов фибры позволяет изменить свойства материала, который может использоваться для решения различных задач.
Бетон с фиброволокном является лучшим материалом для решения многих строительно-ремонтных задачВведение стальной проволоки позволяет значительно повысить прочность бетона, который используется для строительства:
- фундаментов строений, волнорезов, дорожных покрытий и шпал для железнодорожных путей;
- тоннелей и бетонных оснований, которые способны воспринимать значительные нагрузки;
- пешеходных дорожек, покрытий мостов и взлетных полос с повышенной несущей способностью;
- бордюров для автодорог, а также декоративной плитки и изделий для ландшафтного дизайна;
- строений из монолитного железобетона и несущих значительную нагрузку каркасов многоэтажных зданий;
- объектов гидротехнического назначения, водоочистных станций, специальных колодцев и подземных магистралей.
Сфера использования усиленного бетона, в массиве которого содержится стеклянная фибра, отличается. Он используется для решения следующих задач:
- изготовления шумоизоляционных щитов, которые монтируются вдоль автомобильных магистралей;
- обеспечения повышенной гидроизоляции бетонных емкостей на объектах, осуществляющих водоочистку;
- фасадной отделки зданий жилого и производственного назначения, обладающей повышенной прочностью;
- производства различных видов отделочной продукции, предназначенной для декорирования;
- формирования влагостойкой основы для коммерческих, производственных и общественных помещений;
- изготовления прочных элементов декора, используемых оформителями в ландшафтном дизайне.
Фибробетон с добавлением базальтовых волокон также популярен в строительной сфере.
Он применяется в конструкциях, на которые оказывается сильное давление со стороны окружающей средыОн способен воспринимать значительные нагрузки и используется для следующих целей:
- сооружения автостоянок, укрепленных фундаментов, а также покрытий автомагистралей;
- постройки гидротехнических объектов, бетонных резервуаров для хранения жидкостей.
Полипропилен также используется в качестве наполнителя. Бетонная смесь с добавлением полипропилена применяется при производстве:
- вспененных блоков;
- ячеистых бетонов;
- малогабаритных построек.
Реже применяется вискоза и хлопок, область использования которых ограничена.
Плюсы и минусы фибробетона
Фибробетон является довольно новым и перспективным стройматериалом. Вполне закономерно, что не все застройщики имеют представления, что такое фибробетон. Планируя использовать его для строительства, полезно узнать о преимуществах и слабых сторонах фиброволоконного композита. Материал, усиленный стальной проволокой или синтетическими нитями, отличается повышенными эксплуатационными характеристиками.
На практике этот бетон обрел большую популярность благодаря низкому показателю хрупкостиРассмотрим главные достоинства армированного композита:
- снижение уровня затрат на производство строительных работ. При укреплении бетона фиброволокнами отпадает необходимость применения стальных сеток, арматурных каркасов, что снижает трудоемкость, сокращает продолжительность строительных работ;
- повышенные прочностные характеристики продукции, которая не растрескивается. Устойчивость к сколам связана с равномерным расположением фибры в бетонном массиве. При стандартном усилении бетона арматурой проблематично достигнуть аналогичной прочности;
- устойчивость к резким колебаниям температуры. Влага не может проникнуть в армированный фиброй бетон. Он сохраняет целостность массива при резком охлаждении и дальнейшем оттаивании;
- пожаробезопасность. Усиленные фиброволокнами композиты воспринимают воздействие повышенной температуры и открытого огня без нарушения структуры массива и образования трещин;
- небольшой вес. Легкие фибробетонные блоки несложно доставить на строительную площадку. Кладка осуществляется ускоренными темпами, что позволяет оперативно ввести объект в эксплуатацию;
- снижение потребности в стройматериалах. Оно связано с добавлением в смесь усиленного фиброй наполнителя. Повышенная прочность массива позволяет уменьшить толщину стен, сохранив при этом их устойчивость;
- увеличенный ресурс эксплуатации. Усиленный композит превосходит стандартный бетон по долговечности, сохраняя эксплуатационные характеристики на протяжении длительного времени.
Фибробетон обладает множеством положительных свойствНа фоне множества достоинств материала, имеющийся недостаток кажется несущественным. Минус – увеличенная цена фибробетона. Осуществляя производство фибробетона, приходится приобретать дорогостоящее сырье, нести дополнительные расходы. Однако в результате повышенных затрат материал приобретает уникальные эксплуатационные свойства, механическую прочность и долговечность.
Производство фибробетона – технология, состав и рецептура
Технология, обеспечивающая производство фибробетона, имеет свои особенности. Ее эффективность зависит от ряда факторов:
- подбора определенных видов волокон в зависимости от требуемых эксплуатационных свойств композита;
- равномерности перемешивания ингредиентов и введения модификаторов для обеспечения однородной структуры массива;
- особенностей применяемой рецептуры, в том числе одновременного использования различных видов фибры.
Важно правильно подготовить композитный состав, используя проверенные методы:
- введение фиброволокон в сухую смесь из песка и цемента с последующим смешиванием ингредиентов и добавлением воды. Отличие способа – простота, а также отсутствие необходимости привлечения дополнительной рабочей силы;
- добавление волокон фибры в готовую перемешанную смесь из цемента, воды и песка. Метод позволяет повысить прочностные характеристики композита, сократить производственный цикл изготовления.
На прочность и свойства бетонного композита влияют следующие факторы:
- состав применяемых материалов;
- правильно выбранная рецептура;
- соблюдение технологического процесса.
В зависимости от требуемых свойств композита изменяется концентрация вводимых фиброволокон. Доля волокон в общем объеме варьируется от 0,5 кг до 20 кг в зависимости от их типа. Наиболее распространенные марки фибробетона содержат до 2 кг фибры. Оценка качества сырья производится лабораторным методом.
Она включает:
- входной контроль применяемых материалов;
- проверку влажности синтетического наполнителя.
Использование качественного сырья улучшает адгезию фибры, положительно влияет на прочность бетона. Технология позволяет в бытовых условиях самостоятельно подготовить усиленный фибробетонный состав. Для этого потребуется бетоносмеситель и дробилка для измельчения наполнителя.
Подводим итоги
Изучив, что такое фибробетон, можно сделать вывод, что армированный фиброй композит является перспективным стройматериалом. Он обладает комплексом неоспоримых преимуществ, позволяет решать множество серьезных задач в строительной отрасли. Уникальные свойства армированного бетона по достоинству оценили профессиональные строители и частные застройщики. Характеристики композита, усиленного металлической проволокой или синтетической фиброй, позволяют ему уверенно конкурировать со стандартными марками бетона.
Что такое геополимерный бетон?
Во все времена учеными проводились опыты и эксперименты, на которых исследовались смеси, сочетающие природные и искусственные компоненты. Такой тандем позволял получать материалы с более высокими эксплуатационными качествами, поскольку элементы искусственного происхождения усиливали все показатели тех составляющих, которые дала природа. Материалы, полученные таким путем, назывались композитными или полимерными. Один из них – геополимерный бетон, который является новейшим экологически чистым и безопасным стройматериалом. Приставка «гео» (на греческом – «земля») является подтверждением, что новый материал содержит только натуральные ингредиенты.
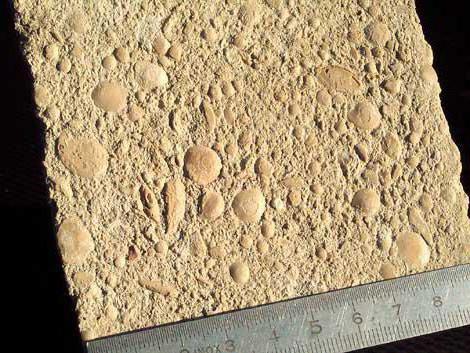
Описание инновационного раствора
Одно из самых важных свойств инновационной бетонной смеси – набор максимальной прочности за короткое время: чтобы полностью затвердеть, ей нужна всего неделя, тогда как традиционному раствору для этого понадобится ровно в 4 раза больше времени.
Геополимерный бетон, как и портландцемент, состоит из нескольких компонентов, но их состав значительно разнится. Новый раствор состоит в основном из золы и шлака – отходов разных отраслей. Ранее подобные отходы совершенно не перерабатывались и только загрязняли окружающую среду. Конечно, выпуск инновационных стройматериалов не решит эту проблему сразу, зато зола и шлаки станут значительной сырьевой базой для их изготовления.
Преимущества применения
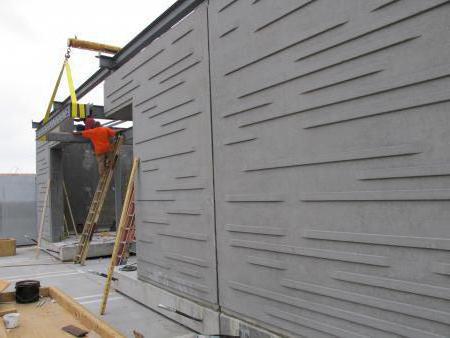
Соответственно, применяя для строительства инновационный раствор, можно значительно сэкономить средства:
- Можно возводить здания, используя меньшее количество стройматериалов.
- Благодаря низкой теплопроводности геополимерного стройматериала снизятся расходы на обогрев помещений в них.
Основные характеристики
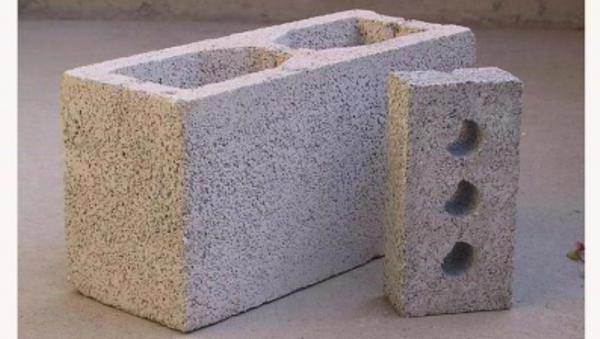
- Малая усадка.
- Высокая прочность на сжатие.
- Устойчивость к кислотам.
- Низкая проницаемость. Этот показатель почти равен аналогичному показателю гранита.
- Отличная устойчивость против высоких температур – до +1300°. Ученые провели эксперимент: на протяжении 120 минут подвергали панели из геополимерного бетона и портландцемента воздействию очень высокой температуры. После этого изделия из инновационной смеси остались совершенно целыми, в то время как на панелях из портландцемента появилось много трещин и сколов.
Но самым ценным свойством рассматриваемого нами раствора является то, что он выделяет минимум парниковых газов.
Если сравнивать структуру нового стройматериала, то она напоминает таковую натурального камня, благодаря чему имеет более высокие свойства, чем обычный раствор. Но самое главное – можно приготовить геополимерный бетон своими руками, поскольку это совсем не сложно. Необходимо только подготовить нужные для работы составляющие.
Особенность состава
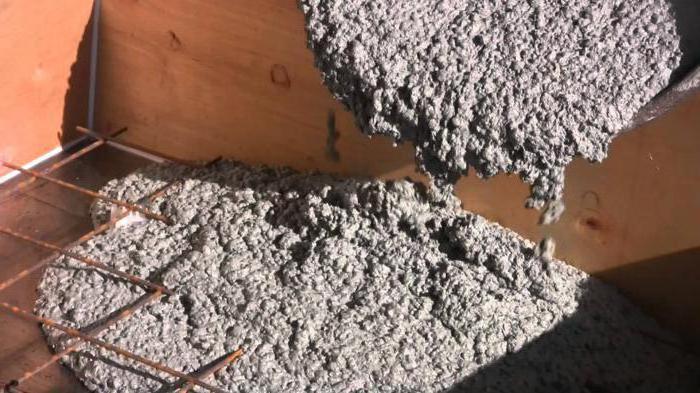
Почему именно зольная пыль? Потому что даже сам по себе этот компонент обладает высокими технологическими и физическими свойствами, поэтому введение его в состав помогает повысить прочностные показатели готовых изделий (до уровня гранита).
Также усилить прочность стройматериала призваны входящие в состав алюминиевые силикаты. Они, вступая со щелочью в реакцию, полимеризуются. Благодаря этому образуется твердый монолит. Именно эта реакция компонентов послужила толчком к появлению другого названия материала — его называют шлакощелочной бетонной смесью.
Подготовка к работе
Прежде чем приступить к работе, нужно подготовить:
- Емкости.
- Инструменты.
- Спецодежду.
- Респиратор.
- Очки.
- Перчатки.
- Весы, чтобы контролировать пропорции.
- Опалубку или форму, куда будет отливаться готовый раствор.
Важная деталь: для перемешивания нужно взять лопатку из такого материала, который не будет вступать в реакцию со щелочами. Лучше всего подойдет инструмент из дерева.
Что немаловажно: смешиваясь, компоненты выделяют тепло, поэтому для перемешивания нужно взять емкость, устойчивую к повышенной температуре. Если необходимо, чтобы готовый раствор быстрее застыл, можно проложить электролиты в опалубке. В таком случае их нужно тоже заранее подготовить.
Рецепт приготовления
Домашние мастера, которые решили сделать геополимерный бетон своими руками, интересуются в первую очередь точным составом смеси. В Сети нет готового рецепта, поскольку производители держат его в тайне, а ученые продолжают работать над совершенствованием инновационного стройматериала. Можно найти много вариаций рецептуры, но при этом изначально предложенный основной состав остается практически неизменным.
Следуя ему, на изготовление 1,0 л геополимерного раствора нужно подготовить:
- 550 г зольной пыли и столько же шлака;
- 110 г воды;
- 240 г жидкого стекла;
- 180 г 45 % КОН.
Все компоненты есть в продаже, и найти их можно без проблем. Конечно, стоимость полученных в итоге изделий будет выше, чем аналогов из обычного портландцемента, зато их прочность намного превосходит бетонные элементы.
Технология приготовления
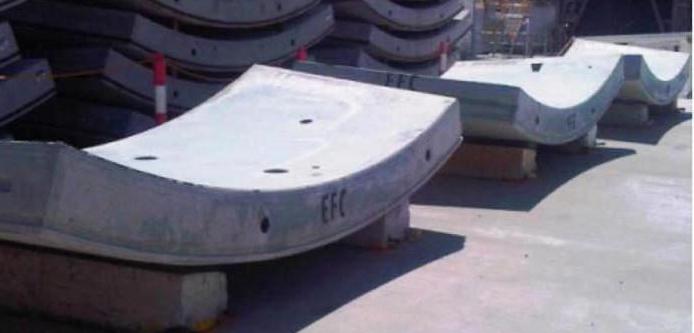
- В помещении, где проводится работа, должна быть низкая влажность, чтобы гидроксид калия не «поплыл». Из-за этой особенности гидроксид обычно распаковывают только перед тем, как положить в раствор.
- КОН является достаточно агрессивным материалом, поэтому работать с ним нужно, используя защитные средства — перчатки и очки.
- Жидкое стекло тоже считается гигроскопичным и агрессивным – с ним нужно быть не менее осторожным.
- Все работы по замешиванию нужно проводить быстро.
Если используется бетономешалка, работать предстоит в следующей последовательности:
- Залить воду. Использовать холодную жидкость нельзя – она должна быть теплой.
- Засыпать шлак и золу.
- После того как все хорошо перемешается, добавить полимеры.
- Снова перемешать до получения однородного раствора.
- Залить смесь в формы.
Важная деталь: летучая зола является веществом с достаточно сомнительной экологической репутацией, но благодаря её применению бетонная смесь приобретает более высокую прочность, которую сохраняет очень долгое время. Поэтому если важно получить прочный материал, можно использовать и золу, но если важнее экологичность, золы можно взять меньше, а часть ее заменить цементом.
Формование изделий
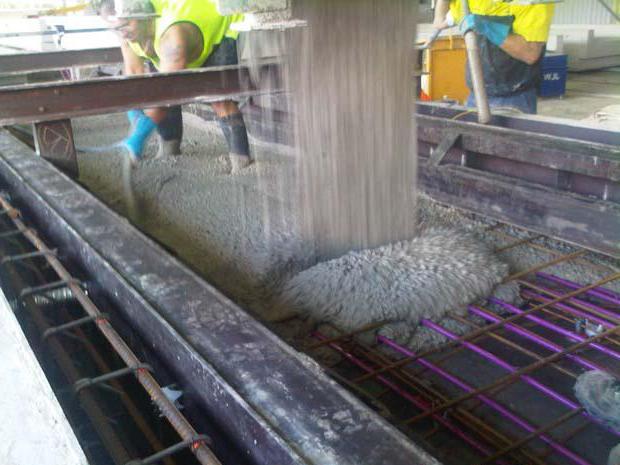
Уже через сутки заготовки затвердеют: на их поверхности образуется пленка. Ее наличие повысит монолитность материалов, и они смогут выдерживать более высокие нагрузки.
Варианты растворов
Для любителей экспериментов этот материал представляет широкое поле для внедрения любых задумок: изготавливая бетонную смесь, можно использовать любые органические вещества. Так, вяжущими компонентами могут послужить водорастворимые смолы. Еще один вариант — использовать вместо смол ПВА, тогда эмульгатором будет поливиниловый спирт, который есть в его составе.
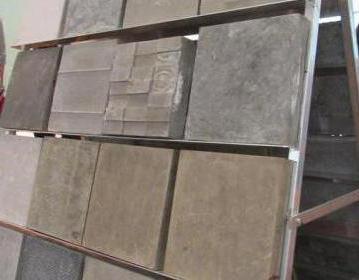
Приобретение готовых смесей
Далеко не каждому потребителю или мастеру нравится экспериментировать — многие предпочитают не делать строительный бетон, а приобретать уже готовый, тем более что никаких затруднений с поиском состава не возникает: уже более 4 лет в России выпускаются геополимерные бетоны на основе глинистого сырья РТ. Производители предлагают разные марки, стоимость которых зависит от количества компонентов и их пропорций. Приобрести стройматериал можно в виде сухих смесей, в которых нет затвердителя.
В продаже есть готовые составы и российского, и зарубежного производства. Их отличия – стоимость и скорость затвердевания.
Представляет интерес продукция следующих торговых марок России:
- «Каменный цветок».
- «Себряковцемент».
- «Евроцемент груп».
Из зарубежных фирм пользуются популярностью материалы таких компаний:
- Немецкая Heidelberger Cement.
- Испанская GRUPOSUBDI.
- Французская LAFARGE.
Достоинства готовых материалов
Сегодня можно приобрести уже готовые бетонные заготовки разных марок. Они изготавливают с учетом следующих показателей:
- Водонепроницаемость – марки W 2-W 12.
- Морозостойкость – марки от F 50 до F 300.
- Прочность – марки от М 50 до М 500.
Кроме того, в готовых смесях — для удобства в работе — объем частей каждого вида наполнителей может варьироваться в зависимости от желаемого конечного результата. Цемент в геополимерный бетон тоже входит, но его часть заменяет зольная пыль. Ее количество должно равняться сумме частей щебня, песка и цемента.
Геополимерный бетон, его состав и рецепты приготовления своими руками
Геополимерный, или как его еще называют, природный, композитный бетон – это новейший экологически безопасный строительный материал. Приставка «гео», говорит о том, что при его изготовлении используются только природные натуральные компоненты. Джозеф Давидовец, в 1978 году ввел понятие «геополимер», а в луизианском Технологическом Университете, спустя несколько десятилетий, группой ученых под руководством профессора Эреза Эллоче был разработан и исследован состав этой инновационной бетонной смеси.
Состав и свойства
В состав геополимерного бетона входят только натуральные компоненты, такие как жидкое стекло, зольная пыль, так называемая «летучая зола», шлак и другие составляющие, служащие для связывания и закрепления смеси. Изготавливают его посредством смешивания указанных компонентов в четко выверенной пропорции, при очень низких температурах. Благодаря химическим процессам, происходящим в такой смеси, получается монолит, который по своим свойствам в несколько раз превосходит обычный портландцемент.
Согласно проведенным исследованиям, геополимер очень устойчив к коррозии, а также на 90% меньше, чем стандартные бетоны, выделяет различных газов, способствующих возникновению «парникового эффекта». Лабораторные испытания также показали огромную огнеупорность данного материала – он способен выдержать до 1 316 °C, а также прочность на растяжение и сжатие.
Кроме этого, он очень устойчив к воздействию различных агрессивных сред, в том числе и к воздействию кислоты. В отличие от обычного бетона, например для скульптур, геополимерный обладает очень низкой проницаемостью, равной проницаемости натурального гранита и значительно меньшей усадкой.
Помимо низкой проницаемости и высокой прочности, отличной устойчивости к температурным и кислотным воздействиям, небольшой усадке, геополимер является быстро затвердевающим и устойчивым к многократным циклам «оттаивания-замораживания». К тому же, в отличие от обычного бетона, он имеет значительно меньший вес.
Ученые в разных странах продолжают улучшать и совершенствовать свойства, чтобы он мог быть использован как при жилищном, так и транспортном строительстве. Производство развивается и в России. Сочетая в себе бетон и экологически безопасную древесину, данный материал довольно дешев.
Для изготовления используется измельченная древесина, которая в дальнейшем вымачивается в воде и обрабатывается озонатором. После подобной обработки, полученную древесную массу закладывают в бетономешалку и соединяют с вяжущими компонентами смеси. После перемешивания смесь заливают в пространство между опалубкой, которая является одновременно и электродами. Ее размер — метр на метр. От автономного источника энергии через преобразователь, в течение часа, на смесь воздействуют электрическим током через опалубку-электроды. После затвердевания обрабатываемого фрагмента, опалубку снимают и переставляют дальше.
Приготовление
Узнав об уникальных свойствах, многие из тех, кто самостоятельно занимается строительством, пытаются найти информацию о том, как можно изготовить геополимерный бетон своими руками и из доступных материалов. Действительно, это возможно. Все дело в том, что необходимы хорошие знания физико-химических свойств и особенностей ингредиентов, а также возможность экспериментировать, так как точной рецептуры и пропорций компонентов, входящих в состав бетона геополимерного типа нет. Вернее сказать, рецептура есть у ученых и производителей, но вот делиться ею и технологией изготовления композитного бетона никто не спешит. Это значит, что получить достойный результат можно только методом «проб и ошибок».
Если вы все же хотите поэкспериментировать, то помните, что наиболее часто в качестве вяжущих компонентов используют водорастворимые смолы или ПВА, особой консистенции. Содержащийся в таком ПВА поливиниловый спирт служит эмульгатором для смеси.
Для того чтобы создаваемая вами бетонная смесь получилась качественной, полимеры или любые другие органические добавки должны составлять около 20% от всей массы цемента. Масса наилучшего качества получается при введении в состав полиамидной или эпоксидной водорастворимых смол, с последующим добавлением полиэтилен-полиаминового отвердителя.
Приготавливаются геополимерные бетонные растворы аналогично стандартным смесям из цемента. В бетономешалку закладывается вода с небольшим количеством цемента, специально предназначенного для полимербетона. После цемента, в смесь вводят, в равных долях, зольную пыль и шлак. Все это тщательно перемешивается, после чего добавляют полимерные компоненты, и всю смесь перемешивают до готовности.
Новые композитные стройматериалы для высотного строительства
Главная страница » Новые композитные стройматериалы для высотного строительства
Американское архитектурное бюро (SOM — Skidmore, Owings & Merrill) активно занимается исследованиями композитов на основе массивной древесины и бетона. Новый стройматериал планируется использовать в технологиях строительства высотных зданий. В частности, речь идёт о сооружении напольной части этажных секций, поддерживаемых стальной конструкцией. Традиционно многоэтажные конструкции создаются на базе металла и бетона. Этот вариант не удовлетворяет всех потребностей конечных владельцев недвижимости. Поэтому новые стройматериалы для сферы строительства многоэтажных зданий, способные урезать господство бетона и стали, всегда были ожидаемы.
СОДЕРЖИМОЕ ПУБЛИКАЦИИ :
Новые стройматериалы для высоток
Одной из причин ограничения внедрения древесины в конструкции высотных строений видится незавершённое до конца тестирование подобных строительных систем на их эксплуатационные качества, в том числе прочность.
И вот совсем недавно (2016-2017 гг.) появилась новая архитекторская идея, где используются конструкционные стальные колонны и балки в ассоциации с композитным стройматериалом — кросс-шихтованной древесиной (CLT) и системой бетонных полов.
Именно такую конструкцию предложено внедрять в современных проектах зданий повышенной этажности.

Американский институт стальных конструкций (AISC) завершил исследования в области применения стальных и деревянных систем высотного строительства.
В результате родился реальный конкурент традиционным схемам – новая система древесно-бетонных полов, специально предназначенная под высотные сооружения.
Композитные полы городских небоскрёбов
Сталь и древесина обладают естественными преимуществами и недостатками. Устойчивые структуры стремятся использовать минимальное количество материалов и минимизировать влияние углеродного следа.
Гибридные (композитные) структуры используют каждый материал там, где он наиболее эффективен, что снижает потребление стройматериалов в целом.

Гибридный (композитный) подход часто является наиболее экономичным решением с точки зрения стоимости и последствий углеродного следа.
Поэтому строительство деревянных конструкций комплексным (гибридным) решением может стать более выгодным.
Техническое примечание:
Углеродный след (carbon footprint) – массовая доля выбросов парниковых газов прямым или косвенным путём:
- людьми,
- производимыми продуктами,
- промышленными организациями,
- мероприятиями разного рода деятельности.
(Из определений UK Carbon Trust – Углеродный фонд Великобритании).
Исследования нового композитного стройматериала
Оценивая разные механизмы сдвиговых усилий соединений между верхним слоем бетона толщиной 57 – 60 мм и слоем кросс-шихтованной древесины толщиной 170 – 172 мм, американские исследователи остановились на применении перфорированного металла и эпоксидной смолы в качестве сцепки.
Именно этот тандем, по мнению учёных, способствует достижению идеальных параметров по сдвиговым скольжениям.

Для тестирования была изготовлена полноразмерная композитная панель пола размерами 2,5 х 11 м. Образец нагружался массой, примерно 37 тонн, что в восемь раз выше проектной нагрузки.
Таким образом, сила давления как возможный фактор ограничения применения композитного пола, не нашла места в исследовательском отчёте.

Исключение составляет «обугливание» древесины в случае пожара, что резко снижает нагрузочные способности композитной бетонно-древесной конструкции полов высотных зданий.
Ограничения применения бетонно-древесного композита
Львиная доля исследований неизбежно порождает дополнительные вопросы именно в моменты изучения тестируемых образцов стройматериалов. Так и здесь, не обошлось без уточнения аналитических методов:
- изучения составных систем пола на основе панелей CLT и бетона;
- разработки руководящих принципов проектирования композитов;
- разработки положений на гибридные системы пола бетон-дерево.
Всё это пока что остаётся без должного ответа и не позволяет без каких-либо ограничений использовать композитный бетонно-древесный стройматериал при строительстве высотных зданий.
Тем не менее, проект SOM «Деревянная башня», можно сказать, дал новую жизнь технологиям высотного строительства, предложив сооружение конструкций на базе стальной системы с внедрением композитной структуры пола.

Чтобы не быть голословными, исследователи разработали эталонный проект девятиэтажной башни, которая недавно была возведена в Калифорнии.
Высотный дом с полами из нового стройматериала
Модель башни выстроена с применением ассиметричных широко-фланцевых стальных балок. На эти балки опираются панели CLT и крепятся специальными фланцами.
При этом в области посадочных точек сделаны технологические вырезы, дабы обеспечить посадку лицевой стороны панелей заподлицо.
Предполагалось, что пересечение бетонного слоя панели со сталью также позволит создать композитную связь, но тестирования на этот счёт ещё не проводилось.
Эталон здания, где используются пост напряженные 200-мм бетонные плоские панели, имеет типичный пролёт колонн 8,5 х 9,75 м.
Смоделированная композитная система предполагает типичный пролёт колонн 8,5 х 7,5 м, при максимальном охвате древесиной композитной системы с глубиной напольного покрытия 270 мм.
Согласно отчету, смоделированная композитная система по размерам больше, чем традиционно предлагаемые габариты.

После проверки различных сценариев: сочленения стройматериалов, предположений относительно объема работ, условий загрузки, соображений планирования, отчет показал очевидные детали. Жизнеспособность предлагаемого композитного стройматериала определит:
- рыночный спрос,
- практичность эксплуатации,
- эффективность строительства,
- общая стоимость проекта.
Между тем здания на основе стали и массивной древесины могут возводиться быстрее, чем каркасно-бетонные здания, при условии предварительного производства гибридных элементов.
Также подчёркивается: высотное здание, возведённое на новых композитных стройматериалах, весит примерно на 65% меньше традиционного проекта. Этот фактор снижает затраты на фундамент, сейсмическую защиту и сокращает время строительства.
В исследовании делается вывод о том, что два типа зданий – на композитных стройматериалах и без таковых, могут быть сопоставимы по стоимости в пределах 10% относительно один другого, в зависимости от специфики проекта и текущих рыночных условий.
Как склеивать древесину — столярная практика
Написано по материалам: Architectmagazine