Газобетонные блоки своими руками: технология производства
Многие владельцы загородных домов с целью сэкономить изготавливают газобетон своими руками в домашних условиях. Газобетонные блоки пользуются большим спросом среди застройщиков, поскольку обладают отличными эксплуатационными характеристиками. Но чтобы домашний строительный материал был качеством не хуже заводского, нужно ознакомиться со всеми особенностями его изготовления заранее, уделив особое внимание пропорциональному соотношению компонентов в составе.
Что собой представляют?
Востребованный в современное время строительный материал — газобетон нашел широкое применение при сооружении различных зданий. Изначально его изготавливали исключительно в заводских условиях, но позже опытные застройщики стали осуществлять производство газобетона собственноручно. Сам процесс выпуска газоблоков несложный, однако, требует строгого соблюдения технологического процесса и пропорций для замешивания. По классу газобетон относится к ячеистым бетонам, содержащим в структуре поры-ячейки.
Сильные и слабые стороны
Этот стройматериал имеет немалое количество преимуществ, которые значительно преобладают над недостатками. А считают плюсами газобетонных блоков следующее:
- Высокая прочность.
- Легкий вес.
- Отличные теплоизоляционные свойства. Здания из этого материала не требуют дополнительного использования теплоизоляционных средств, что существенно сэкономит бюджет.
- Поглощает уровень шума, проникающий извне.
- Универсальность.
- Влагостойкость и морозостойкость.
- Безопасность. Имея натуральный состав, является безопасным для здоровья человека.
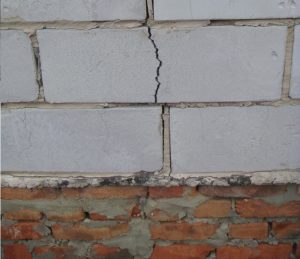
Из недостатков выделяют повышенную хрупкость, теплопроводность и способность чрезмерно поглощать влагу. Из газобетонных блоков можно построить ограждения, перегородки, наружные одно-, двух- и трехслойные стены, а также несущие внутри помещений. Следует отметить, что газобетон бывает 2 типов:
- Автоклавный. Газобетон изготавливается путем термической обработки стройматериала под давлением в специальных печах, которые носят название автоклав.
- Неавтоклавный. Газобетонные блоки твердеют и прочнеют в естественных условиях.
На дому удастся изготовить только неавтоклавный стройматериал, но при правильном соблюдении технологического процесса блоки выйдут не менее прочными и качественными.
Инструменты и материалы
Оборудование
Чтобы сделать газобетон собственноручно на дому, нужно запастись следующим оборудованием:
- Металлические струны. Они необходимы для удаления вытекающего газобетонного раствора.
- Формы. Применяются для придания изделию необходимого геометрического размера.
- Бетоносмеситель. Смешивает компоненты раствора и соединяет готовую массу с газообразователем. Без него не получится сделать качественный и правильной консистенции строительный материал.
Составляющие
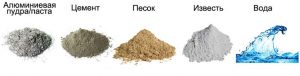
От правильности приготовления раствора зависит прочность газоблоков и непосредственно возводимого сооружения. Ингредиенты берутся только высококачественные, строго в соответствии с необходимой дозировкой. Так, понадобится 1 т портландцемента, маркой не ниже М400, 180 кг кварцевого песка, 1,5 кг каустической соды, 400 г алюминиевой пудры и в среднем 60 л воды. Подготовив компоненты, можно приступать к изготовлению газобетона, следуя такому алгоритму:
- Смешать цемент и песок.
- Влить воду и размешать смесь.
- Всыпать постепенно остальные составляющие (кроме серебрянки), постоянно помешивая массу.
- Подмешать алюминиевую пудру. Именно она вступает в реакцию с известью и в результате получается водород. Он и образует в сырье, имеющее невероятное множество пор.
Подготовка форм
Еще один важный этап производственного процесса — изготовление форм. Их можно приобрести готовые либо сделать собственноручно. Выбрав второй вариант, потребуется взять доски и сколотить из них прямоугольную емкость. В нее вставить перемычки, разделяющие форму по всей длине на ячейки. Размерами этих ячеек определяются параметры газобетонных блоков. Чтобы раствор не прилипал к доскам, опытные застройщики рекомендуют смазывать их внутренние части масляным составом, который готовится из 3 частей воды и 1 части машинного масла.
Технология производства
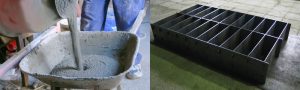
Автоклав — специальное оборудование, которое нагревает раствор под давлением выше атмосферного. С его помощью удастся создать прочный, высококачественный строительный материал, но применение такого агрегата возможно только в заводских условиях. Дома же при приготовлении газобетона приходится обходиться без такого оборудования и после того, как раствор размешан, а формы подготовлены, приступают к заливке. Этот этап обычно сложностей не вызывает, но также требует определенной аккуратности и внимательности. Подготовленный газобетон вливают в емкости, заполняя их наполовину, поскольку после химической реакции раствор начнет подниматься. Далее идет обратный процесс и строительная смесь опускается.
Чтобы придать газобетонным блокам ровную поверхность, нужно срезать выступающий бугорок металлической струной и оставить бетонное изделие высыхать, набираться прочностных характеристик. Спустя 24 часа блоки извлекают и ставят на ровный участок, пока они полностью не затвердеют. При этом нужно следить, чтобы в помещении, где сохнут газоблоки, не было сквозняков.
Неавтоклавный газобетон: технология, состав, свойства
В строительстве неавтоклавный газобетон применяется при возведении малоэтажных зданий. В многоэтажных конструкциях — оформление разделительных перегородок, внутренних стен, заполнение бетонных и стальных каркасов, для теплоизоляции поверхностей. Преимуществом материала является возможность заливки монолитной конструкции любого размера и веса.
Что это такое?
Первоначально технология производства ячеистого газобетона предусматривала помещение блоков в специальные печи-автоклавы при давлении в 8—10 бар и температуре 200 градусов, что обеспечивало полный выход влаги из материала. Позднее стал использоваться более простой способ производства под названием «неавтоклавный газобетон» — без давления и обжига в печах, с процессом твердения в естественных условиях. Составы растворов, заливаемых в формы для формирования блоков, одинаковы в обоих случаях.
Состав и свойства
Компоненты, входящие в состав смеси для производства неавтоклавного газобетона:
- портландцемент марки не ниже М300, не менее 50% от общего веса;
- песок;
- зола, мел, гипс, доменный шлак;
- алюминиевая пудра для пенообразования;
- известь;
- вода;
- хлорид кальция — для ускорения процесса твердения смеси;
- добавки и присадки для улучшения эксплуатационных характеристик материала.
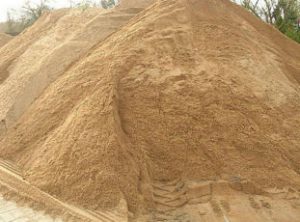
Рецептура раствора для неавтоклавного бетона требует использования песка без примесей глины или ила, воды — без содержания соли. В качестве добавок для улучшения прочности газобетона рекомендуются: полуводный гипс, микрокремнезем, кислая зола-унос. С этой же целью могут добавляться армирующие волокна, что улучшит характеристики материала. Для более качественного пенообразования могут быть добавлены стиральные порошки, поваренная соль.
Как производится: технология
Изготовление стандартное: приготовление раствора, заливка в опалубку или формы, застывание и твердение продукции. Из инструментов понадобится бетономешалка, лопата, ведра. Все сухие компоненты перед началом работ взвешиваются и отмериваются согласно долям, что требуют составы по технологии. Пенообразование происходит при вступлении в реакцию щелочных составляющих цементного раствора с алюминиевой пудрой. В результате высвобождается водород и формируются ячеистые поры.
Самый важный момент в процессе неавтоклавного изготовления газобетона, влияющий на конечные характеристики продукта, — вспенивание смеси. Реакция с газообразованием должна произойти до момента добавления в смесь вяжущего вещества.
Поэтапный процесс производства неавтоклавного газобетона:
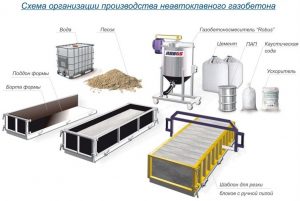
- Готовится опалубка либо формы для заливки. Внутренние поверхности обрабатываются маслом.
- В отдельной емкости готовится пенообразователь: заливается вода с алюминиевой пудрой из расчета 50:1. Добавляется стиральный порошок и оставшаяся часть пудры согласно рецептуре. Тщательно перемешивается до полного исчезновения металлических частиц на поверхности.
- В бетономешалку заливается расчетное количество воды, агрегат включается.
- Засыпается песок, цемент.
- Через 2 мин в смесь добавляется известь.
- Засыпается поваренная соль.
- Через 5 мин от начала процесса смесь готова для заливки в опалубку/формы.
- После полного отвердения массы опалубка снимается либо демонтируется каркас и монолитный газобетон нарезается на блоки нужной формы.
Плюсы и минусы использования
Составы бетонных блоков, применяемых в строительстве сходны, при этом неавтоклавный газобетон имеет свои достоинства. К ним относятся: небольшой вес; теплостойкость; влаго- и морозоустойчивость; энергосберегающие свойства; высокие звукоизоляционные характеристики; сейсмостойкость; податливость любым электрическим и ручным инструментам; возможность заливки блоков любой формы; несложный процесс изготовления. При этом показатели прочности ниже других подобных материалов. К другим недостаткам относится склонность к разрушению под действием механических нагрузок, большая усадка, длительный период ожидания затвердения материала в процессе производства.
Как сделать газобетонные блоки своими руками: расчет
Зачастую владельцев загородных домов интересует вопрос самостоятельного изготовления газобетонных блоков, так как это позволит существенно сэкономить на строительстве, к тому же, данный материал обладает неплохими эксплуатационными характеристиками.Чтобы помочь в этом вопросе, далее мы подробно рассмотрим, как делают газобетонные блоки в домашних условиях.

Газобетонные блоки
Общие сведения
Газобетон относится к классу легких ячеистых бетонов, так как содержит в своей структуре поры-ячейки.
Благодаря этому он обладает многими положительными качествами, среди которых можно выделить:
- Низкую теплопроводность;
- Хорошую паропроницаемость;
- Хорошие звукоизоляционные свойства;
- Небольшой вес
Кроме того, цена такого материала ниже, чем обычного бетона, что связано с его небольшой плотностью, и, как следствие, меньшим расходом цемента и других компонентов при изготовлении.

Структура газобетона
Следует отметить, что газобетон бывает двух типов:
Автоклавный | Технология изготовления автоклавного газобетона заключается в термической обработке материала под давлением в специальных печах (автоклавах). Блоки, полученные таким способом, отличаются высокой прочностью и долговечностью.Недостатком данной технологии является невозможность ее реализации в домашних условиях, так как для изготовления блоков требуется дорогостоящее профессиональное оборудование. |
Неавтоклавный | Такой газобетон затвердевает и набирает прочность в естественных условиях. По прочности и долговечности он уступает автоклавному, однако, для небольшого строительства и многих других частных нужд он вполне подходит. |

Оборудование для производства автоклавного газобетона
Изготовление газобетона
Итак, разобравшись как делают газобетонные блоки, можно прийти к заключению, что в домашних условиях получится изготовить только неавтоклавный материал. Надо сказать, что при точном соблюдении технологии, и использовании качественных компонентов, можно получить блоки с отличными характеристиками.
Процесс изготовления газобетонных блоков своими руками состоит из нескольких этапов:
- Приготовления бетона в соответствии с определенными пропорциями.
- Заливки форм;
- Выдержке изделия и извлечении из форм.

Бетоносмеситель
Оборудование
Изготовление неавтоклавного газобетона, как уже было сказано выше, не требует сложного оборудование, однако, некоторый необходимый минимум все же имеется:
- Бетоносмеситель–без него не получится качественно размешать раствор и смешать его с газообразователем.
- Формы – чтобы придать изделию правильные геометрические размеры.
- Металлические струны – нужны для обрезки излишков раствора с верхней части форм.
Формы
Прежде чем приступить к изготовлению блоков, следует подготовить формы.Их можно купить либо сделать самостоятельно. Для этого понадобятся доски с тщательно оструганной одной стороной.
Из этих досок надо собрать деревянный пенал, внутрь которого вставляются перемычки. При помощи таких вставок, внутреннее пространство пенала делится на отсеки. Перемычки можно сделать из фанеры. Для их фиксации в досках выполняются пропилы.
Как несложно догадаться, от размеров ячеек будут зависеть габариты блоков.Определившись с размерами ячеек, можно заранее подсчитать, сколько газобетонных блоков в 1м3, при необходимости размеры можно подкорректировать.

На фото — формы для газоблоков
Для ускорения процесса изготовления материала, желательно сделать несколько форм всех необходимых типоразмеров.Предварительно следует сделать расчет газобетонных блоков, в соответствии с которым подготовить оптимальное количество форм.
Совет!
Чтобы раствор не прилипал к доскам, внутреннюю часть ячеек следует хорошо смазать отработанным машинным маслом.
Данную процедуру необходимо выполнять перед каждой заливкой.
Приготовление раствора
Состав газобетонных блоков довольно простой:
- Портландцемент;
- Кварцевый песок;
- Вода;
- Добавки –алюминиевая пудра, известь, сульфат натрия.
Для получения качественной смеси, необходимо строго соблюдать пропорцию:
100 кг | |
Кварцевый песок | 180 кг |
Сульфат натрия | 0,5 кг |
Каустик | 1,5 кг |
Алюминиевая пудра | 0,4 кг |
Вода | Около 60 л |

Алюминиевая пудра для газобетона
Инструкция по приготовлению раствора выглядит следующим образом:
- В первую очередь смешивается цемент и песок.
- Далее в состав добавляется вода, и смесь тщательно перемешивается.
- Постепенно в раствор добавляются другие компоненты и хорошо перемешиваются.
- В последнюю очередь засыпается алюминиевая пудра.
Надо сказать, что этап приготовления раствора является наиболее ответственным, так как подгадать удачные пропорции очень сложно, и сделать это можно лишь опытным путем. Пропорции во многом зависят от качества песка, марки цемента и остальных компонентов. Даже вода влияет на ход химической реакции, которая происходит при добавлении газообразователя.
Обратите внимание!
Соединение натрия можно не применять. Этот компонент служит для ускорения процесса застывания состава.
Поэтому не существует какой-то конкретной рекомендации по изготовлению газобетона в домашних условиях.

Заливка форм
Заливка
Заливка форм является довольно простым процессом, однако, требующим определенной аккуратности и внимательности. Заполнять формы следует до половины, после чего, в результате химической реакции, состав начнет подниматься.
Увеличение в объеме происходит обычно в течение 5 – 8 минут. Время реакции зависит от температуры окружающей среды. Спустя некоторое время начнется обратный процесс, т.е. масса немного опустится.
Когда положение массы стабилизируется, верхнюю бугристую часть следует обрезать при помощи металлической струны. Затем состав должен выдержаться до отвердения бетонного изделия, на это обычно уходит 20-24 часа.Спустя данный промежуток времени, блоки надо извлечь из форм и поставить на ровное место до полного затвердевания.
Обратите внимание!
При изготовлении пенобетонных блоков следует позаботиться, чтобы в помещении отсутствовали сквозняки.
После успешного выполнения первой партии блоков, следует выполнить расчет количества газобетонных блоков, необходимого для строительства. После этого процедуру следует в точности повторить.Вот и все основные нюансы изготовления газобетонных блоков, ознакомившись с которыми, можно самостоятельно обеспечить строительство необходимым стройматериалом.
Вывод
Как мы выяснили, самостоятельно изготовить неавтоклавный газобетон совершенно несложно. Самое главное в данной операции – подобрать оптимальные пропорции компонентов. Кроме того, придется потратить некоторое время и силы на изготовление форм, однако, все эти затраты будут оправданы экономией финансовых средств при строительстве.
Из видео в этой статье можно получить дополнительную информацию по данной теме.
Технология. Рецепт Вашего газобетона.
Златоустовские Бетонные Технологии уделяют особое внимание сопровождению Заказчика в области технологии изготовления газобетона.
Высококлассное оборудование должно быть оснащено правильной, выверенной технологией изготовления.
В большей степени именно владение технологией — залог производительности, качества продукции, уменьшения издержек и отходов.
Сырьевые компоненты у всех Заказчиков разные:
- песок — зависит от природных характеристик региона;
- цемент – от поставщика, срока годности;
- реактивы, добавки – от поставщика, а главное – от их комбинирования.
Характеристики газобетона требуются разные:
- по прочности;
- по плотности;
- по цветности.
Т.е. для каждого Заказчика нужна своя технология изготовления газобетона.
Поэтому, еще на начальном этапе технолог ЗБТ рекомендует задуматься о подборе оптимального рецепта изготовления Вашего газоблока.
С этой целью Вы можете прислать в адрес ЗБТ пробники своих компонентов. В лаборатории ЗБТ мы проведем ряд испытаний и исследований представленных материалов. Вам будет выписана Ваша технология – выберем золотую середину с точки зрения практики и экономики, исходя из оптимального набора Ваших компонентов.
Отлаженную технологию изготовления легко перенести на реальные объемы. Во время пуско-наладочных работ мы вместе проведем необходимое количество замесов до получения готовой продукции.
Дистанционно работа будет продолжена. При Вашем желании, вместе получим сертификат, подтверждающий соответствие Вашего газоблока требованиям ГОСТ.
Конечно, любые вопросы технологии, ее шлифовки, изменения и пр.и в дальнейшем мы будем решать вместе. Эта работа очень значима для ЗБТ.
Мы заинтересованы в том, чтобы наше классное оборудование не стояло в Вашем красивом цеху, а производило газобетон, способствуя строительству новых городов и поселков.
НАШИ ТВЕРДЫЕ РЕШЕНИЯ ДЛЯ ВАШЕГО ЛЕГКОГО БЕТОНА
Все материалы о технологии изготовления газобетона Вы можете посмотреть в разделе нашего сайта «О газобетоне»- «Советы технолога».
Состав для получения неавтоклавного газобетона и способ его приготовления
Изобретения относятся к производству строительных материалов и изделий из ячеистого бетона. Состав для получения неавтоклавного газобетона включает, мас.%: портландцемент 30,7-40,9, зола ТЭС 21,5-32,3, оксид кальция 1,62-2,16, алюминиевая пудра 0,098-0,110, отработанный текстильный корд 0,64-0,97, хлориды щелочных и щелочноземельных металлов, выбранные из NaCl, CaCl2, KCl, LiCl 0,15-0,41, продукт конденсации нафталинсульфокислоты и формальдегида 0,23-0,41, вода — остальное. Способ получения неавтоклавного газобетона включает приготовление пластично-вязкой указанной выше сырьевой смеси с предварительным совместным помолом сухих компонентов указанной смеси, за исключением портландцемента, в течение 30-40 мин, вспучивание сырьевой смеси, ее твердение при пропаривании или в нормальных условиях, причем после указанного совместного помола сухих компонентов в состав сырьевой смеси вводят портландцемент. Технический результат — улучшение эксплуатационных характеристик газобетона с одновременным упрощением его получения. 2 н.п. ф-лы, 1 табл.
Изобретение относится к производству строительных материалов и изделий из ячеистого бетона, поризованного газом, и может быть использовано на заводах ячеистобетонных изделий и в монолитном строительстве.
Известен состав сырьевой смеси для получения газобетона (RU №2255073, кл. С04В 38/02, 27.06.2005), содержащий компоненты в мас.%:
Цемент | 15-50 |
Песок | 31-42 |
Алюминиевая пудра | 0,10-1,0 |
Каустическая сода | 0,05-0,45 |
Вода | остальное |
Недостатком известного состава является повышенный расход наиболее дорогого компонента сырьевой смеси — алюминиевой пудры, что ведет к увеличению себестоимости газобетона. Кроме того, использование в известном составе песка естественной дисперсности может вызывать явления седиментации при приготовлении и укладке газобетонной смеси, что приводит к вариотропности структуры газобетона, увеличению толщины межпоровой перегородки, что негативно влияет на прочностные характеристики и увеличению его средней плотности.
Наиболее близким составом сырьевой смеси для получения газобетона является состав (RU №2304127, кл. С04В 38/02; В28В 1/50, 10.08.2007), содержащий следующие компоненты, мас.%:
Портландцемент | 40,1-45,8 |
Известь | 8,1-9,2 |
Молотый песок | 41,3-48,0 |
Текстильный корд | 3,5-8,5 |
Алюминиевая пудра | 0,210-0,214 |
Недостатками прототипа являются замедленная кинетика набора прочности материала, а также увеличенные энергозатраты на помол кварцевого песка, что затрудняет его использование в монолитном строительстве.
Известен способ получения неавтоклавного зольного газобетона (RU №2134250, кл. С04В 40/00, 10.08.1999), который заключается в приготовлении пластично-вязкой сырьевой смеси, насыщении ее газовой средой, в процессе вспучивания или вспенивания, твердении при пропаривании, причем зольный наполнитель, входящий в состав сырьевой смеси, предварительно активируют путем его перемешивания с водой затворения в бетоносмесителе с частотой вращения рабочего органа 500-700 об/мин в течение 1-5 мин. Оптимальное время активации определяют по максимальной высоте осадка в отстое активированной зольной суспензии или оптимальному водородному показателю рН той же суспензии.
Однако известный способ получения неавтоклавного зольного газобетона трудоемок, характеризуется большими затратами времени, требует специального смесительного оборудования и не всегда может быть реализован в условиях строительной площадки.
Прототипом предлагаемого способа является способ получения зольного газобетона, включающий приготовление пластично-вязкой сырьевой смеси с предварительным активированием отвальной золы ТЭЦ, вспучивание сырьевой смеси, твердение ее при пропаривании или в нормальных условиях, причем активирование отвальной золы ТЭЦ производят в процессе совместного помола всех сухих компонентов сырьевой смеси в течение 20-40 мин (RU №2168485, кл. C04B 38/02, С04В 40/00, 10.06.2001).
Недостатком этого способа является наличие в нем операции помола тонкодисперсного компонента сырьевой смеси — цемента — совместно с другими составляющими, что увеличивает время технологического процесса и уменьшает производительность помольных установок.
Задачей изобретения является разработка состава неавтоклавного газобетона и способа его изготовления с возможностью использования газобетона в монолитном строительстве.
Техническим результатом изобретения являются улучшенные эксплуатационные характеристики неавтоклавного газобетона с одновременным упрощением его получения.
Поставленная задача и указанный технический результат решается тем, что состав для получения неавтоклавного газобетона, включающий портландцемент, кремнеземистый компонент, оксид кальция, алюминиевую пудру, отработанный текстильный корд, согласно изобретению дополнительно содержит хлориды щелочных и щелочноземельных металлов, выбранные из групп NaCl, CaCl2, KCl, LiCl, и продукт конденсации нафталинсульфокислоты и формальдегида, а в качестве кремнеземистого компонента используют золу ТЭС при следующем соотношении компонентов, мас.%:
Портландцемент | 30,7-40,9 |
Зола ТЭС | 21,5-32,3 |
Оксид кальция | 1,62-2,16 |
Алюминиевая пудра | 0,098-0,110 |
Отработанный | |
текстильный корд | 0,64-0,97 |
Хлориды щелочных | |
и щелочноземельных | |
металлов, выбранные | |
из групп NaCl, CaCl2, | |
KCl, LiCl | 0,15-0,41 |
Продукт конденсации | |
нафталинсульфокислоты | |
и формальдегида | 0,23-0,41 |
Вода | остальное |
Поставленная задача достигается также тем, что в способе приготовления неавтоклавного газобетона, включающем приготовление пластично-вязкой сырьевой смеси с предварительным помолом сухих компонентов смеси в течение 30-40 мин, вспучивание сырьевой смеси, твердение при пропаривании или в нормальных условиях, согласно изобретению после совместного помола сухих компонентов вводят в состав сырьевой смеси портландцемент.
При содержании в составе неавтоклавного газобетона портландцемента менее 30,7% прочность газобетона ниже допустимого стандартами уровня, а при содержании портландцемента более 40,9% в газобетоне появляются усадочные деформации, приводящие к снижению прочности и морозостойкости.
При содержании оксида кальция менее 1,62% не обеспечивается достаточной щелочности жидкой фазы и эффективного газообразования смеси, а при содержании оксида кальция более 2,16% возможно снижение прочности газобетона.
При содержании золы ТЭС менее 21,5% появляются усадочные деформации, приводящие к снижению прочности и морозостойкости. При содержании золы ТЭС более 32,3% прочность газобетона ниже допустимого стандартами уровня.
При содержании алюминиевой пудры менее 0,098% газобетон не достигает заданной пористости, что приводит к повышенной плотности. При содержании алюминиевой пудры более 0,110% образуется избыточное количество водорода, что приводит к слиянию газовых пузырьков и вырыванию их через поверхность наружу. В результате чего происходит осадка газобетонной смеси.
Введение отработанного текстильного корда в количестве 0,64-0,97% оптимизирует макроструктуру, уменьшает усадочные деформации и увеличивает трещиностойкости газобетона. При содержании корда менее 0,64% не обеспечивается достаточного улучшения физико-механических свойств газобетона. При содержании корда более 0,97% затрудняется равномерное его распределение в смеси, структура газобетона характеризуется наличием крупных пор и пустот.
Хлориды щелочных и щелочноземельных металлов, выбранные из групп NaCl, CaCl2, KCl, LiCl, увеличивают щелочность жидкой фазы и тем самым улучшают газообразование и вспучивание сырьевой смеси, а также способствуют ускорению твердения газобетона, что позволяет получать изделия без тепловой обработки. При содержании хлоридов менее 0,15% не обеспечивается эффективного ускорения твердения газобетона. При содержании хлоридов более 0,41% прочность газобетона изменяется незначительно.
Продукт конденсации нафталинсульфокислоты и формальдегида снижает водотвердое отношение газобетонной смеси на 13-15% и повышает прочность газобетона. Содержание продукта конденсации нафталинсульфокислоты и формальдегида менее 0,23% не дает достаточного водоредуцирующего эффекта, а при содержании добавки более 0,41% замедляется дальнейшее водоредуцирование и повышение прочности газобетона.
В данном способе приготовления неавтоклавного газобетона производят совместный помол сухих компонентов сырьевой смеси за исключением портландцемента, который вводят в состав смеси после помола. Портландцемент — это тонкодисперсный материал и его дополнительный помол неэффективен. При этом достигается уменьшение времени технологического процесса, энергозатрат на помол и увеличение производительности помольных установок. При совместном сухом помоле компонентов смеси происходит механическая активация частиц алюминия, снятие с их поверхности парафиновой пленки, диспергирование зольного компонента, что приводит к возрастанию числа активных центров на поверхности зольных частиц и улучшению физико-механических характеристик газобетона. Также происходит равномерное распределение компонентов во всем объеме смеси, что приводит к повышению качества газобетона. При совместном помоле компонентов газобетонной смеси в одном агрегате упрощается технология производства газобетона за счет уменьшения оборудования.
Состав для получения неавтоклавного газобетона и способ его приготовления иллюстрируются примером.
Пример.
Для получения неавтоклавного газобетона использовали портландцемент, оксид кальция, золу ТЭС, алюминиевую пудру, отработанный текстильный корд, хлориды щелочных и щелочноземельных металлов, выбранные из групп NaCl, CaCl2, KCl, LiCl, продукт конденсации нафталинсульфокислоты и формальдегида. В таблице приведены конкретные составы для получения неавтоклавного газобетона.
В соответствии с предлагаемым способом все сухие компоненты смеси за исключением портландцемента совместно размалывали в шаровой лабораторной мельнице. Далее полученную сухую смесь перемешивали с портландцементом. Окончательный состав сухой смеси помещали в воду затворения и перемешивали в течение 2 мин. Приготовленную газобетонную смесь заливали в формы 10×10×10 см. После 3 часовой выдержки срезали «горбушку». Распалубка форм осуществлялась через 48 часов, после чего образцы помещались в камеру нормального твердения. В дальнейшем образцы высушивались до постоянной массы и подвергались физико-механическим испытаниям. Результаты испытаний образцов приведены в таблице.
Остальные примеры приготовления состава для получения неавтоклавного газобетона осуществлялись аналогично примеру, данные которых представлены в таблице.
№ п/п | Компоненты состава, мас. % | Плотность, кг/м3 | Предел прочности при сжатии, МПа | |
3 сут | 28 сут | |||
1 | Портландцемент — 30,7 | |||
Зола ТЭС — 32,3 | ||||
Оксид кальция — 1,62 | ||||
Алюминиевая пудра — 0,098 | ||||
Отработанный текстильный корд — 0,64 | ||||
Хлориды щелочных и щелочноземельных металлов, выбранные из групп NaCl, CaCl2, KCl, LiCl — 0,15 | ||||
445 | 0,51 | 1,1 | ||
Продукт конденсации нафталинсульфокислоты и формальдегида — 0,23 | ||||
Вода — 34,262 | ||||
2 | Портландцемент — 35,1 | |||
Зола ТЭС — 27,7 | ||||
Оксид кальция — 1,85 | ||||
Алюминиевая пудра — 0,104 | ||||
Отработанный текстильный корд — 0,64 | ||||
Хлориды щелочных и щелочноземельных металлов, выбранные из групп NaCl, CaCl2, KCl, LiCl — 0,17 | ||||
460 | 0,73 | 1,3 | ||
Продукт конденсации нафталинсульфокислоты и формальдегида — 0,26 | ||||
Вода — 34,176 | ||||
3 | Портландцемент — 40,9 | |||
Зола ТЭС — 21,5 | ||||
Оксид кальция — 2,16 | ||||
Алюминиевая пудра — 0,110 | ||||
Отработанный текстильный корд — 0,97 | ||||
Хлориды щелочных и щелочноземельных металлов, выбранные из групп NaCl, CaCl2, KCl, LiCl — 0,41 | ||||
485 | 0,87 | 1,6 | ||
Продукт конденсации нафталинсульфокислоты и формальдегида — 0,41 | ||||
Вода — 33,540 |
Данные таблицы показывают, что предлагаемый состав и способ его приготовления позволяют получать неавтоклавный газобетон с прочностью на 34% выше и плотностью на 12% ниже, чем у прототипа. Исключение операции помола тонкодисперсного компонента — цемента — совместно с другими составляющими сырьевой смеси увеличивает производительность помольных установок и уменьшает время технологического процесса.
Заявленный состав и способ не ограничиваются приведенными примерами их осуществления. В рамках изобретения возможны и другие примеры состава и способа его осуществления, не выходящие за пределы формулы и описания.
В настоящее время изобретение находится на стадии опытно-лабораторных испытаний.
1. Состав для получения неавтоклавного газобетона, включающий портландцемент, кремнеземистый компонент, оксид кальция, алюминиевую пудру, отработанный текстильный корд, отличающийся тем, что он дополнительно содержит хлориды щелочных и щелочноземельных металлов, выбранные из групп NaCl, CaCl2, KCl, LiCl, и продукт конденсации нафталинсульфокислоты и формальдегида, а в качестве кремнеземистого компонента используют золу ТЭС при следующем соотношении компонентов, мас.%:
портландцемент | 30,7-40,9 |
зола ТЭС | 21,5-32,3 |
оксид кальция | 1,62-2,16 |
алюминиевая пудра | 0,098-0,110 |
отработанный текстильный корд | 0,64-0,97 |
хлориды щелочных и щелочноземельных | |
металлов, выбранные из групп NaCl, | |
CaCl2, KCl, LiCl | 0,15-0,41 |
продукт конденсации | |
нафталинсульфокислоты | |
и формальдегида | 0,23-0,41 |
вода | остальное |
2. Способ получения неавтоклавного газобетона, включающий приготовление пластично-вязкой сырьевой смеси по п.1 с предварительным совместным помолом сухих компонентов смеси за исключением портландцемента в течение 30-40 мин, вспучивание сырьевой смеси, ее твердение при пропаривании или в нормальных условиях, причем после указанного совместного помола сухих компонентов в состав сырьевой смеси вводят портландцемент.
Технология. Какие добавки делают газобетон лучше?
Алексей Бурдовицын 05 сен 2016
У многих наших клиентов получается снять блоки с форм и увезти их на склад через 6-7 часов. Как же они этого добиваются?
Скажу сразу — у всего есть разумный предел. Отгрузить заказчику готовые блоки через час после заливки не получится. Зато у многих наших клиентов получается снять блоки с форм и увезти их на склад через 6-7 часов. Как же они этого добиваются?
Для начала я перечислю основные моменты, которые влияют на производительность линии:
- Соблюдение технологии. Если правильно подобрана технология, то и производительность будет высокой.
- Качество сырья. Если сырье качественное и свежее, то и все химические процессы будут протекать быстрее.
- Температура воды. Чем горячее вода, тем теплее газобетонная смесь. Но во всем есть своя золотая середина. Оптимальной температурой смеси мы считаем 43-45 градусов.
- Температура в камерах прогрева или в помещении, где будут находиться формы после заливки. Чем этот показатель выше, тем быстрее будет твердеть газобетон.
- Наличие автоматизации производства. Автоматизированное производство как правило более производительное.
- Навыки персонала. Практика показывает, что производительность разных рабочих может отличаться в несколько раз.
- Применение добавок. Об этом пункте поговорим подробнее.
Перечислю и кратко расскажу об основных добавках, которые мы рекомендуем применять нашим клиентам:
- Пластификаторы. Эта добавка применяется в производстве железобетона для изготовления особо прочных марок. Она позволяет уменьшить количество воды на 15-20% и примерно на столько же сделать бетон прочнее. Так же практика показывает что применение пластификатора заметно ускоряет схватывание цемента.
- Хлорид кальция (поваренная соль). Одна из самых доступных и дешевых добавок ускорителей твердения. Но такие добавки очень чувствительны к цементу — далеко не с каждым они будут взаимодействовать. Также при больших дозировках в будущем на блоках могут выступать высолы.
- Сульфат натрия также является ускорителем твердения цемента. Он менее восприимчив к марке цемента, и большинство наших клиентов применяют именно его.
- Комплексные добавки. Это как правило смесь пластификаторов с сульфатами или хлоридами. К таким добавкам относится, например, Реламикс. На рынке много разных вариантов таких комплексных добавок, и они работают у всех наших клиентов по-разному. Оптимальную можно подобрать только в результате экспериментов.
- Фиброволокно. Это тончайшие волокна, которые пронизывают весь массив газобетона, тем самым делая его прочнее в 1,5-2 раза. Фиброволокно не влияет на процесс, но значительно улучшит конечный результат. Для газобетона хорошо подойдут полипропиленовые или базальтовые волокна. Они увеличат прочность и никак не помешают резке блоков. Кроме того, уменьшится усадка и повысится устойчивость к трещинам.
Ещё один важный момент. Добавки составляют отдельную статью расходов, но как ни странно их применение позволяет существенно экономить.
Дело в том, что применение добавок как правило значительно увеличивает прочность газобетона. Но если прочность нас и так устраивает, то применение добавок позволяет снизить количество цемента. И как правило экономия на цементе оказывается намного выше, чем затраты на добавки.
Качественный газобетон — это результат последовательных экспериментов и в этот момент очень важно иметь хорошую техническую поддержку от поставщика оборудования.
Наши технологи всегда готовы вам помочь, к тому же большинство вопросов можно обсудить у нас на форуме.
У нас всегда есть помощь для вас, к тому же большинство вопросов можно обсудить у нас на форуме — прямо сейчас.
Обсудить на форумеСтатьи по теме:
Где взять денег на запуск бизнеса на газобетоне? Что нужно знать о покупке оборудования в лизинг?