Прочность — Википедия
Прочность деревянного кузова DKW F8, 1939. На едущем автомобиле стоят не менее 28 человекПро́чность (в физике и материаловедении) — свойство материала сопротивляться разрушению под действием напряжений, возникающих под воздействием внешних сил.
Свойство конструкции выполнять назначение, не разрушаясь в течение заданного времени.
Прочность подразделяют на статическую, под действием постоянных нагрузок, динамическую и усталостную (выносливость), имеющую место при действии циклических переменных нагрузок.
Для конструкций различают общую прочность — способность всей конструкции выдерживать нагрузки без разрушения, и местную — та же способность отдельных узлов, деталей, соединений.
В настоящее время при расчёте на прочность используют как расчёт по допускаемым напряжениям, так и расчёт по допускаемому числу циклов нагружения. Основные неравенства расчёта по допускаемым напряжениям:
σmax⩽[σ],τmax⩽[τ],{\displaystyle \sigma _{max}\leqslant [\sigma ],\quad \tau _{max}\leqslant [\tau ],}
где
- σmax{\displaystyle \sigma _{max}} и τmax{\displaystyle \tau _{max}} — наибольшие расчётные нормальное и касательное напряжения, соответственно;
- [σ]{\displaystyle [\sigma ]} и [τ]{\displaystyle [\tau ]} — допускаемые нормальное и касательное напряжения, безопасные для прочности детали.
Обеспечение прочности машин, аппаратов и конструкций осуществляется следующим образом. На стадии их проектирования производится расчётная или экспериментальная оценка возможности развития в несущих элементах проектируемых конструкций процессов разрушений различных типов: усталостного, хрупкого, квазистатического, разрушения вследствие ползучести материала, коррозии, износа в процессе эксплуатации и т. п. При этом должны быть рассмотрены все возможные в условиях эксплуатации конструкции, известные на данный момент механизмы разрушения материала, из которого выполнены её несущие элементы. Для вновь создаваемого класса машин или аппаратов указанные механизмы разрушения выявляются на стадии научно-исследовательского цикла проектирования. С каждым из таких механизмов разрушения связывается определённый критерий прочности — та или иная характеристика физического состояния материала элементов машин и аппаратов, определяемая расчётным или экспериментальным путём. Для каждого из критериев прочности материала конструкции экспериментально устанавливаются его предельные значения. По предельным значениям далее определяются допускаемые значения этих критериев. Последние определяются, как правило, путём деления предельных значений критерия прочности на соответствующий коэффициент запаса прочности. Значения коэффициентов запаса прочности назначаются на основе опыта эксплуатации с учётом степени ответственности проектируемой конструкции, расчётного срока её эксплуатации и возможных последствий её разрушения.
Значения коэффициентов запаса прочности для различных механизмов разрушения различны. При расчёте по допускаемым напряжениям они изменяются, как правило, в диапазоне значений от 1,05 (при обеспечении прочности элементов летательных аппаратов, имеющих краткий жизненный цикл и не предназначенных для транспортировки людей) до 6 (при обеспечении прочности тросов, используемых в конструкциях пассажирских лифтов). При расчёте по допускаемому числу циклов нагружения могут использоваться существенно большие значения этих коэффициентов. Расчёт наиболее ответственных и энергонасыщенных конструкций машин и аппаратов регламентируется отраслевыми нормами и стандартами. По мере накопления опыта эксплуатации, развития методов исследования физического состояния конструкций и совершенствования методов обеспечения прочности эти нормы и стандарты периодически пересматриваются.
Разрушения[править | править код]
Хрупкое и вязкое разрушение имеют разные виды разрушенной поверхности. Характер дефектов дает понятие, какого рода разрушение имеет место. При хрупком разрушении поверхность надломлена. При вязком разрушении поверхность натянута (вяжет разрушение).
Вязкость разрушения — это относительное повышение растягивающих напряжений в устье трещины при переходе её от стабильной к нестабильной стадии роста.[1]
Вязкость разрушения тесно связана с показателями прочности материала. Увеличение прочности сопровождается снижением пластичности и вязкости разрушения. Это объясняется тем, что у высокопрочных материалов мала энергия, поглощаемая при разрушении, уровень которой определяется величиной пластической деформации у вершины трещины. Для высокопрочных материалов эффект увеличения прочности существенно перекрывается снижением пластичности, в результате чего вязкость разрушения уменьшается. Материалы средней и низкой прочности при комнатной температуре обычно имеют более высокие значения, чем высокопрочные. С понижением температуры прочность растет и при определённых условиях поведение материала средней и низкой прочности становится таким же, как у высокопрочного материала при комнатной температуре. При низких температурах испытание вязкости разрушения можно проводить на образцах меньших размеров.
Для расчёта напряженно-деформируемого состояния конструкции и определения её прочности применяются современные наукоемкие технологии — системы компьютерного инженерного анализа, основанные на применении сеточных методов решения задач математической физики. В настоящее время одним из наиболее эффективных и универсальных методов этого класса является метод конечных элементов (МКЭ).
Наиболее распространённые системы КЭ анализа:
ANSYS — универсальная система КЭ анализа с встроенным пре-/постпроцессором;
MSC.Nastran — универсальная система КЭ анализа с пре-/постпроцессором;
ABAQUS — универсальная система КЭ анализа с встроенным пре-/постпроцессором;
NEiNastran — универсальная система КЭ анализа с пре-/постпроцессором FEMAP;
NX Nastran — универсальная система КЭ анализа с пре-/постпроцессором FEMAP.
ПК ЛИРА-САПР — система КЭ анализа строительных и машиностроительных конструкций.
Определение прочности, пластичности, упругости
Прочность – способность материала сопротивляться разрушению под действием внешних сил.
Пластичность – способность материала к пластической деформации, т.е. к получению остаточного изменения формы и размеров без разрушения.
Упругость – свойство материала восстанавливать свои размеры и форму после прекращения действия нагрузки.
Прочность, пластичность и упругость материала определяют при статических испытаниях на растяжение.
Рис. 1.1. Статические испытания на растяжение:
а – схема испытания; б – диаграмма растяжения
Испытания производятся на цилиндрических (или плоских) образцах с определенным соотношением между длиной l0 и диаметром d0. Образец растягивается под действием приложенной силы P (рис. 1.1.) до разрушения. Внешняя нагрузка вызывает в образце напряжение и деформацию.Напряжение σ
=
,
Деформация характеризует изменение размеров образца под действием нагрузки, %
=
100,
где l – длина растянутого образца. Деформация может быть упругой (исчезающей после снятия нагрузки) и пластической (остающейся после снятия нагрузки).
При испытаниях строится диаграмма растяжения, представляющая собой зависимость напряжения от деформации. На рис 1.1, б приведена такая диаграмма для низкоуглеродистой стали. После проведения испытаний определяются следующие характеристики механических свойств.
Предел упругости σу – это максимальное напряжение, при котором в образце не возникают пластические деформации.
Предел
текучести

Предел
прочности (или временное сопротивление) –
это напряжение, отвечающее максимальной
нагрузке, которую выдерживает образец
при испытании.
Относительное
удлинение после разрыва
=
·
100,
где lk – длина образца после разрыва.
Относительным
сужением после разрыва называется
уменьшение площади поперечного сечения
образца, отнесенное к начальному сечению
образца, %:
=
·
100,
где Fk – площадь поперечного сечения образца в месте разрыва. Относительное удлинение и относительное сужение являются характеристиками пластичности.
Определение твердости
Твердость – способность материала сопротивляться проникновению в него другого тела.
Твердость материала испытывается при статическом характере вдавливания в него шарика, конуса или пирамиды.
Наиболее широкое применение нашли методы определения твердости по Бринеллю, Роквеллу и Виккерсу (рис. 1.2.).
Твердость по Бринеллю (НВ) определяется вдавливанием в испытываемую поверхность под нагрузкой Р стального шарика диаметром Д (рис. 1.2, а).
После снятия нагрузки на поверхности образца остается отпечаток (лунка).
Твердость определяется по формуле
НВ
= ,
Па,
где F – площадь поверхности отпечатка.
Рис. 1.2. Схемы определения твердости:
а – по Бринеллю; б – по Роквеллу; в – по Виккерсу
Диаметр шарика выбирают в зависимости от толщины изделия (Д = 10; 5; 2,5 мм). Нагрузку Р выбирают в зависимости от диаметра шарика и измеряемой твердости. При Д = 10 мм Р = 30000 Н, время – 10 секунд.
Практически величину твердости определяют не по формуле, а по прилагаемой к прибору таблице в зависимости от диаметра отпечатка.
Между твердостью по Бринеллю и пределом прочности металла существует приближенная зависимость
=
к · НВ, Па
Для
стали =
0,34 … 0,35 НВ.
Твердость по Роквеллу определяют по глубине отпечатка. Метод основан по вдавливании в испытуемый образец закаленного стального шарика диаметром 1,588 мм (шкала В) или алмазного конуса с углом при вершине 1200 (шкалы А и С). Вдавливание производится под действием двух нагрузок – предварительной Р0, равной 100 Н и окончательной Р, равной 600, 1000, 1500 Н для шкал А, В и С соответственно. Число твердости по РоквеллуHRA, HRB и HRC определяется по разности глубин вдавливания в условных единицах.
Твердость по Виккерсу определяют вдавливанием в испытываемую поверхность (шлифованную или даже полированную) четырехгранной алмазной пирамиды с углом при вершине 1360. Метод используют для определения твердости деталей малой толщины и тонких поверхностных слоев, имеющих высокую твердость. Число твердости по Виккерсу HV определяется отношением приложенной нагрузки к площади поверхности отпечатка.
Практически величину твердости определяют не по формуле, а по прилагаемым к прибору таблицам по измеренной величине d (диагональность отпечатка) рис. 1.2., в.
Прочность — это… Что такое Прочность?
Прочность деревянного кузова DKW F8, 1939. На едущем автомобиле стоят не менее 28 человекПро́чность (в физике и материаловедении) — свойство материала сопротивляться разрушению под действием внутренних напряжений, возникающих под воздействием внешних сил.
Свойство конструкции выполнять назначение, не разрушаясь в течение заданного времени.
Классификация
Прочность подразделяют на статическую, под действием постоянных нагрузок, динамическую и усталостную (выносливость), имеющую место при действии циклических переменных нагрузок.
Для конструкций различают общую прочность — способность всей конструкции выдерживать нагрузки без разрушения, и местную — та же способность отдельных узлов, деталей, соединений.
Количественное рассмотрение
В настоящее время при расчёте на прочность используют как расчёт по допускаемым напряжениям, так и расчёт по допускаемому числу циклов нагружения. Основные неравенства расчёта по допускаемым напряжениям:
где
- и — наибольшие расчётные нормальное и касательное напряжения, соответственно;
- и — допускаемые нормальное и касательное напряжения, безопасные для прочности детали.
Прикладное применение
Обеспечение прочности машин и аппаратов осуществляется следующим образом. На стадии их проектирования производится расчётная или экспериментальная оценка возможности развития в несущих элементах проектируемых конструкций процессов разрушений различных типов: усталостного, хрупкого, квазистатического, разрушения вследствие ползучести материала, коррозии, износа в процессе эксплуатации и т. п. При этом должны быть рассмотрены все возможные в условиях эксплуатации конструкции известные на данный момент механизмы разрушения материала, из которого выполнены её несущие элементы. Для вновь создаваемого класса машин или аппаратов указанные механизмы разрушения выявляются на стадии научно-исследовательского цикла проектирования. С каждым из таких механизмов разрушения связывается определённый критерий прочности — та или иная характеристика физического состояния материала элементов машин и аппаратов, определяемая расчётным или экспериментальным путём. Для каждого из критериев прочности материала конструкции экспериментально устанавливаются его предельные значения. По предельным значениям далее определяются допускаемые значения этих критериев. Последние определяются, как правило, путём деления предельных значений критерия прочности на соответствующий коэффициент запаса прочности. Значения коэффициентов запаса прочности назначаются на основе опыта эксплуатации с учётом степени ответственности проектируемой конструкции, расчётного срока её эксплуатации и возможных последствий её разрушения.
Значения коэффициентов запаса прочности для различных механизмов разрушения различны. При расчёте по допускаемым напряжениям они изменяются, как правило, в диапазоне значений от 1,05 (при обеспечении прочности элементов летательных аппаратов, имеющих краткий жизненный цикл и не предназначенных для транспортировки людей) до 6 (при обеспечении прочности тросов, используемых в конструкциях пассажирских лифтов). При расчёте по допускаемому числу циклов нагружения могут использоваться существенно большие значения этих коэффициентов. Расчёт наиболее ответственных и энергонасыщенных конструкций машин и аппаратов регламентируется отраслевыми нормами и стандартами. По мере накопления опыта эксплуатации, развития методов исследования физического состояния конструкций и совершенствования методов обеспечения прочности эти нормы и стандарты периодически пересматриваются.
Разрушения
Хрупкое и вязкое разрушение имеют разные виды разрушенной поверхности. Характер дефектов дает понятие, какого рода разрушение имеет место. При хрупком разрушении поверхность надломлена. При вязком разрушении поверхность натянута (вяжет разрушение).
Вязкость разрушения — это относительное повышение растягивающих напряжений в устье трещины при переходе её от стабильной к нестабильной стадии роста. [1]
Вязкость разрушения тесно связана с показателями прочности материала. Увеличение прочности сопровождается снижением пластичности и вязкости разрушения. Это объясняется тем, что у высокопрочных материалов мала энергия, поглощаемая при разрушении уровень которой определяется величиной пластической деформации у вершины трещины. Для высокопрочных материалов эффект увеличения прочности существенно перекрывается снижением пластичности, в результате чего вязкость разрушения уменьшается. Материалы средней и низкой прочности при комнатной температуре обычно имеют более высокие значения, чем высокопрочные. С понижением температуры прочность растет и при определённых условиях поведение материала средней и низкой прочности становится таким же, как у высокопрочного материала при комнатной температуре. При низких температурах испытание вязкости разрушения можно проводить на образцах меньших размеров.
Примечания
См. также
Ссылки
Прочность — это… Что такое Прочность?
твёрдых тел, в широком смысле — свойство твёрдых тел сопротивляться разрушению (разделению на части), а также необратимому изменению формы (пластической деформации) под действием внешних нагрузок. В узком смысле — сопротивление разрушению.
В зависимости от материала, вида напряжённого состояния (растяжение, сжатие, изгиб и др.) и условий эксплуатации (температура, время действия нагрузки и др.) в технике приняты различные меры П. (предел текучести, временное сопротивление, предел усталости и др.). Разрушение твёрдого тела — сложный процесс, зависящий от перечисленных и многих др. факторов, поэтому технические меры П. — условные величины и не могут считаться исчерпывающими характеристиками.
Физическая природа прочности. П. твёрдых тел обусловлена в конечном счёте силами взаимодействия между атомами и ионами, составляющими тело. Эти силы зависят главным образом от взаимного расположения атомов. Например, сила взаимодействия двух соседних атомов (если пренебречь влиянием окружающих атомов) зависит лишь от расстояний между ними (рис. 1). При равновесном расстоянии ro Прочность 10 нм эта сила равна нулю. При меньших расстояниях сила положительна и атомы отталкиваются, при больших — притягиваются. На критическом расстоянии rk сила притяжения по абсолютной величине максимальна и равна Fт. Например, если при растяжении цилиндрического стержня с поперечным сечением So действующая сила Р, направленная вдоль его оси, такова, что приходящаяся на данную пару атомов внешняя сила превосходит максимальную силу притяжения Fт, то последние беспрепятственно удаляются друг от друга. Однако, чтобы тело разрушилось вдоль некоторой поверхности, необходимо, чтобы все пары атомов, расположенные по обе стороны от рассматриваемой поверхности, испытывали силу, превосходящую Fт. Напряжение, отвечающее силе Fт, называется теоретической прочностью на разрыв στ (στ ≈ 0,1 Е, где Е — модуль Юнга). Но на опыте наблюдается разрушение при нагрузке Р*, которой соответствует напряжение σ = P*/S, в 100—1000 раз меньшее στ. Расхождение теоретической П. с действительной объясняется неоднородностями структуры тела (границы зёрен в поликристаллическом материале, посторонние включения и др.), из-за которых нагрузка Р распределяется неравномерно по сечению тела.
Механизм разрушения. Зарождению микротрещин при напряжении ниже στ способствуют термической Флуктуации. Если на участке поверхности S малых размеров (но значительно превышающем сечение одного атома) локальное напряжение окажется больше στ, вдоль этой площадки произойдёт разрыв. Края разрыва разойдутся на расстояние, большее rk, на котором межатомные силы уже малы, и образуется трещина (рис. 2). Локальные напряжения особенно велики у края образовавшейся трещины, где происходит Концентрация напряжений, причём они тем больше, чем больше её размер. Если этот размер больше некоторого критического rc, на атомы у края трещины действует напряжение, превосходящее σт, и трещина растет дальше по всему сечению тела с большой скоростью — наступает разрушение. rc определяется из условия, что освободившаяся при росте трещины упругая энергия материала покрывает затраты энергии на образование новой поверхности трещины: rc ≈ Еγ / σ2 (где γ — энергия единицы поверхности материала). Прежде чем возрастающее внешнее усилие достигнет необходимой для разрушения величины, отдельные группы атомов, особенно входящие в состав дефектов в кристаллах, обычно испытывают перестройки, при которых локальные напряжения уменьшаются («релаксируют»). В результате происходит необратимое изменение формы тела — пластическая деформация; ей также способствуют термической флуктуации. Разрушению всегда предшествует большая или меньшая пластическая деформация. Поэтому при оценке rc в энергию γ должна быть включена работа пластической деформации γР, которая обычно на несколько порядков больше истинной поверхностной энергии γ. Если пластическая деформация велика не только вблизи поверхности разрушения, но и в объёме тела, то разрушение вязкое. Разрушение без заметных следов пластической деформации называется хрупким. Характер разрушения проявляется в структуре поверхности излома, изучаемой фрактографией (См. Фрактография). В кристаллических телах хрупкому разрушению отвечает скол по кристаллографическим плоскостям спайности, вязкому — слияние микропустот (на фрактограммах выявляются в виде чашечек) и скольжение. При низкой температуре разрушение преимущественно хрупкое, при высокой — вязкое. температура перехода от вязкого к хрупкому разрушению называется критической температурой хладноломкости.Поскольку разрушение есть процесс зарождения и роста трещин, оно характеризуется скоростью или временем τ от момента приложения нагрузки до момента разрыва, т. е. долговечностью материала. Исследования многих кристаллических и аморфных тел показали, что в широком интервале температур Т (по абсолютной шкале) и напряжений σ, приложенных к образцу, долговечность τ при растяжении определяется соотношением
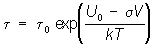
Некоторые значения прочности на растяжение, σ0 в кгс/мм2 (1 кгс/мм2= 10 Мн/м2)
———————————————————————————————————————————————-
| Материалы | σ0 | σ0/Е |
|———————————————————————————————————————————————|
| Графит (нитевидный кристалл) | 2400 | 0,024 |
| Сапфир (нитевидный кристалл) | 1500 | 0,028 |
| Железо (нитевидный кристалл) | 1300 | 0,044 |
| Тянутая проволока из высокоуглеродистой стали | 420 | 0,02 |
| Тянутая проволока из вольфрама | 380 | 0,009 |
| Стекловолокно | 360 | 0,035 |
| Мягкая сталь | 60 | 0,003 |
| Нейлон | 50 | |
———————————————————————————————————————————————-
Время τ затрачивается на ожидание термофлуктуационного зарождения микротрещин и на их рост до критического размера rc. Когда к образцу прикладывают напряжение σ, он деформируется сначала упруго, затем пластически, причём около структурных неоднородностей, имевшихся в исходном состоянии или возникших при пластической деформации, возникают большие локальные напряжения (в кристаллах в голове заторможенных сдвигов — скоплений дислокаций (См. Дислокации)). В этих местах зарождаются микротрещины. Их концентрация может быть очень большой (например, в некоторых ориентированных полимерах до 1015 трещин в 1 см3). Однако при этом их размеры, определяемые масштабом структурных неоднородностей, значительно меньше rc. Трещины не растут, и тело не разрушается, пока случайно, например благодаря последовательному слиянию близко расположенных соседних микротрещин, одна из них не дорастет до критического размера. Поэтому при создании прочных материалов следует заботиться не столько о том, чтобы трещины не зарождались, сколько о том, чтобы они не росли.
Случайное распределение структурных неоднородностей по объёму образца, по размерам и по степени прочности и случайный характер термических флуктуаций приводят к разбросу значений долговечности (а также предела П. σ0) при испытаниях одинаковых образцов при заданных значениях σ и Т. Вероятность встретить в образце «слабое» место тем больше, чем больше его объём. Поэтому П. (разрушающее напряжение) малых образцов (например, тонких нитей) выше, чем больших из того же материала (т. н. масштабный эффект). Участки с повышенным напряжением, где легче зарождаются микротрещины, встречаются чаще у поверхности (выступы, царапины). Поэтому полировка поверхности и защитные покрытия повышают П. Напротив, в агрессивных средах П. понижена.
Меры повышения прочности. При создании высокопрочных материалов стремятся в первую очередь повысить сопротивление пластической деформации. В кристаллических телах это достигается либо за счёт снижения плотности дефектов (П. нитевидных кристаллов, лишённых подвижных дислокаций, достигает теоретической), либо за счёт предельно большой плотности дислокаций в мелкодисперсном материале. Второе требование — большое сопротивление разрушению — сводится к выбору материала с высокой теоретической П. σт = 0,1 Е. Создать материалы с модулем Юнга Е, превышающим максимальные встречающиеся в природе значения, можно искусственно, путем применения высоких давлений; однако в этом направлении делаются лишь первые шаги. Большие значения σт затрудняют зарождение микротрещин. Чтобы предотвратить их рост, материал должен быть достаточно пластичным. Тогда у вершины трещины необходимые для её роста высокие напряжения рассасываются за счёт пластической деформации. Сочетание высокой П. и пластичности достигается в сплавах термомеханической обработкой, в композитах — подбором материала волокон и матрицы, объёмной доли и размера волокон. Трещина, возникшая в прочной (обычно хрупкой) фазе сплава или в волокне композита, останавливается у границы с пластичной матрицей. Поэтому важной характеристикой высокопрочных материалов является сопротивление распространению трещины, или вязкость разрушения. При механическом измельчении материалов требуется пониженная П. Она достигается воздействием поверхностно-активных сред (органические вещества, вода).
Лит.: Разрушение, пер. с англ., под ред. А. Ю. Ишлинского, т. 1, М., 1973; Работнов Ю. Н., Сопротивление материалов, М., 1962; Гуль В. Е., Структура и прочность полимеров, 2 изд., М., 1971; Механические свойства новых материалов, пер. с англ., под ред. Г. И. Баренблатта, М., 1966; Инденбом В. Л., Орлов А. Н., Проблема разрушения в физике прочности, «Проблемы прочности», 1970, № 12, с. 3; Регель В. Р., Слуцкер А. И., Томашевский Э. Е., Кинетическая природа прочности твердых тел, М., 1974.
А. Н. Орлов.
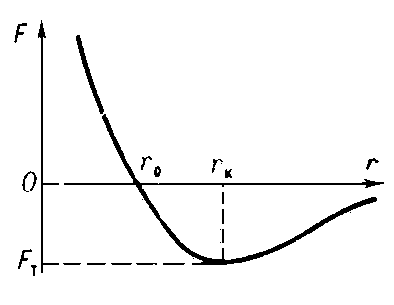
Рис. 1. Зависимость силы взаимодействия двух атомов от расстояния между ними.
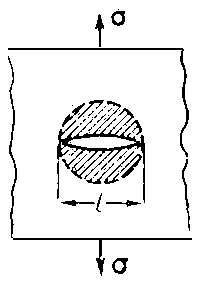
Рис. 2. Трещина Гриффита. Стрелки указывают направление растяжения; заштрихована область, в которой сняты напряжения.
Большая советская энциклопедия. — М.: Советская энциклопедия. 1969—1978.
Определение прочности, пластичности, упругости
Прочность – способность материала сопротивляться разрушению под действием внешних сил.
Пластичность – способность материала к пластической деформации, т.е. к получению остаточного изменения формы и размеров без разрушения.
Упругость – свойство материала восстанавливать свои размеры и форму после прекращения действия нагрузки.
Прочность, пластичность и упругость материала определяют при статических испытаниях на растяжение.
Рис. 1.1. Статические испытания на растяжение:
а – схема испытания; б – диаграмма растяжения
Испытания производятся на цилиндрических (или плоских) образцах с определенным соотношением между длиной l0 и диаметром d0. Образец растягивается под действием приложенной силы P (рис. 1.1.) до разрушения. Внешняя нагрузка вызывает в образце напряжение и деформацию.Напряжение σ – это отношение силы P к площади поперечного сечения F, МПа:
=
,
Деформация характеризует изменение размеров образца под действием нагрузки, %
=
100,
где l – длина растянутого образца. Деформация может быть упругой (исчезающей после снятия нагрузки) и пластической (остающейся после снятия нагрузки).
При испытаниях строится диаграмма растяжения, представляющая собой зависимость напряжения от деформации. На рис 1.1, б приведена такая диаграмма для низкоуглеродистой стали. После проведения испытаний определяются следующие характеристики механических свойств.
Предел упругости σу – это максимальное напряжение, при котором в образце не возникают пластические деформации.
Предел
текучести –
это напряжение, соответствующее площадке
текучести на диаграмме растяжения (рис.
1.1, б). Если на диаграмме нет площадки
текучести (что наблюдается для хрупких
материалов), то определяют условный
предел текучести
–
напряжение, вызывающее пластическую
деформацию, равную 0,2%.
Предел
прочности (или временное сопротивление) –
это напряжение, отвечающее максимальной
нагрузке, которую выдерживает образец
при испытании.
Относительное
удлинение после разрыва –
отношение приращения длины образца при
растяжении к начальной длине l0,
%:
=
·
100,
где lk – длина образца после разрыва.
Относительным
сужением после разрыва называется
уменьшение площади поперечного сечения
образца, отнесенное к начальному сечению
образца, %:
=
·
100,
где Fk – площадь поперечного сечения образца в месте разрыва. Относительное удлинение и относительное сужение являются характеристиками пластичности.
Определение твердости
Твердость – способность материала сопротивляться проникновению в него другого тела.
Твердость материала испытывается при статическом характере вдавливания в него шарика, конуса или пирамиды.
Наиболее широкое применение нашли методы определения твердости по Бринеллю, Роквеллу и Виккерсу (рис. 1.2.).
Твердость по Бринеллю (НВ) определяется вдавливанием в испытываемую поверхность под нагрузкой Р стального шарика диаметром Д (рис. 1.2, а).
После снятия нагрузки на поверхности образца остается отпечаток (лунка).
Твердость определяется по формуле
НВ
= ,
Па,
где F – площадь поверхности отпечатка.
Рис. 1.2. Схемы определения твердости:
а – по Бринеллю; б – по Роквеллу; в – по Виккерсу
Диаметр шарика выбирают в зависимости от толщины изделия (Д = 10; 5; 2,5 мм). Нагрузку Р выбирают в зависимости от диаметра шарика и измеряемой твердости. При Д = 10 мм Р = 30000 Н, время – 10 секунд.
Практически величину твердости определяют не по формуле, а по прилагаемой к прибору таблице в зависимости от диаметра отпечатка.
Между твердостью по Бринеллю и пределом прочности металла существует приближенная зависимость
=
к · НВ, Па
Для
стали =
0,34 … 0,35 НВ.
Твердость по Роквеллу определяют по глубине отпечатка. Метод основан по вдавливании в испытуемый образец закаленного стального шарика диаметром 1,588 мм (шкала В) или алмазного конуса с углом при вершине 1200 (шкалы А и С). Вдавливание производится под действием двух нагрузок – предварительной Р0, равной 100 Н и окончательной Р, равной 600, 1000, 1500 Н для шкал А, В и С соответственно. Число твердости по РоквеллуHRA, HRB и HRC определяется по разности глубин вдавливания в условных единицах.
Твердость по Виккерсу определяют вдавливанием в испытываемую поверхность (шлифованную или даже полированную) четырехгранной алмазной пирамиды с углом при вершине 1360. Метод используют для определения твердости деталей малой толщины и тонких поверхностных слоев, имеющих высокую твердость. Число твердости по Виккерсу HV определяется отношением приложенной нагрузки к площади поверхности отпечатка.
Практически величину твердости определяют не по формуле, а по прилагаемым к прибору таблицам по измеренной величине d (диагональность отпечатка) рис. 1.2., в.
Определение прочности, пластичности, упругости
Прочность– способность материала сопротивляться разрушению под действием внешних сил.
Пластичность – способность материала к пластической деформации, т.е. к получению остаточного изменения формы и размеров без разрушения.
Упругость – свойство материала восстанавливать свои размеры и форму после прекращения действия нагрузки.
Прочность, пластичность и упругость материала определяют при статических испытаниях на растяжение.
Рис. 1.1. Статические испытания на растяжение:
а – схема испытания; б – диаграмма растяжения
Испытания производятся на цилиндрических (или плоских) образцах с определенным соотношением между длиной l0 и диаметром d0. Образец растягивается под действием приложенной силы P (рис. 1.1.) до разрушения. Внешняя нагрузка вызывает в образце напряжение и деформацию. Напряжение σ – это отношение силы P к площади поперечного сечения F, МПа:
=
,
Деформация характеризует изменение размеров образца под действием нагрузки, %
=
100,
где l – длина растянутого образца. Деформация может быть упругой (исчезающей после снятия нагрузки) и пластической (остающейся после снятия нагрузки).
При испытаниях строится диаграмма растяжения, представляющая собой зависимость напряжения от деформации. На рис 1.1, б приведена такая диаграмма для низкоуглеродистой стали. После проведения испытаний определяются следующие характеристики механических свойств.
Предел упругости σу – это максимальное напряжение, при котором в образце не возникают пластические деформации.
Предел
текучести –
это напряжение, соответствующее площадке
текучести на диаграмме растяжения (рис.
1.1, б). Если на диаграмме нет площадки
текучести (что наблюдается для хрупких
материалов), то определяют условный
предел текучести
– напряжение, вызывающее пластическую
деформацию, равную 0,2%.
Предел
прочности (или временное сопротивление) – это напряжение, отвечающее максимальной
нагрузке, которую выдерживает образец
при испытании.
Относительное
удлинение после разрыва – отношение приращения длины образца
при растяжении к начальной длинеl0,
%:
=
·
100,
где lk – длина образца после разрыва.
Относительным
сужением после разрыва называется уменьшение площади поперечного
сечения образца, отнесенное к начальному
сечению образца, %:
=
·
100,
где Fk – площадь поперечного сечения образца в месте разрыва. Относительное удлинение и относительное сужение являются характеристиками пластичности.
Определение твердости
Твердость – способность материала сопротивляться проникновению в него другого тела.
Твердость материала испытывается при статическом характере вдавливания в него шарика, конуса или пирамиды.
Наиболее широкое применение нашли методы определения твердости по Бринеллю, Роквеллу и Виккерсу (рис. 1.2.).
Твердость по Бринеллю (НВ) определяется вдавливанием в испытываемую поверхность под нагрузкой Р стального шарика диаметром Д (рис. 1.2, а).
После снятия нагрузки на поверхности образца остается отпечаток (лунка).
Твердость определяется по формуле
НВ
= ,
Па,
где F – площадь поверхности отпечатка.
Рис. 1.2. Схемы определения твердости:
а – по Бринеллю; б – по Роквеллу; в – по Виккерсу
Диаметр шарика выбирают в зависимости от толщины изделия (Д = 10; 5; 2,5 мм). Нагрузку Р выбирают в зависимости от диаметра шарика и измеряемой твердости. При Д = 10 мм Р = 30000 Н, время – 10 секунд.
Практически величину твердости определяют не по формуле, а по прилагаемой к прибору таблице в зависимости от диаметра отпечатка.
Между твердостью по Бринеллю и пределом прочности металла существует приближенная зависимость
=
к · НВ, Па
Для
стали = 0,34 … 0,35 НВ.
Твердость по Роквеллу определяют по глубине отпечатка. Метод основан по вдавливании в испытуемый образец закаленного стального шарика диаметром 1,588 мм (шкала В) или алмазного конуса с углом при вершине 1200 (шкалы А и С). Вдавливание производится под действием двух нагрузок – предварительной Р0, равной 100 Н и окончательной Р, равной 600, 1000, 1500 Н для шкал А, В и С соответственно. Число твердости по Роквеллу HRA, HRB и HRC определяется по разности глубин вдавливания в условных единицах.
Твердость по Виккерсу определяют вдавливанием в испытываемую поверхность (шлифованную или даже полированную) четырехгранной алмазной пирамиды с углом при вершине 1360. Метод используют для определения твердости деталей малой толщины и тонких поверхностных слоев, имеющих высокую твердость. Число твердости по Виккерсу HV определяется отношением приложенной нагрузки к площади поверхности отпечатка.
Практически величину твердости определяют не по формуле, а по прилагаемым к прибору таблицам по измеренной величине d (диагональность отпечатка) рис. 1.2., в.
8. Прочность материалов. Выражение и определение прочности. Зависимость прочности от различных факторов.
Прочность – свойство материалов сопротивляться разрушению из-за возникающих в них внутренних напряжений.
Численной характеристикой этого свойства является предел прочности (временное сопротивление), который в строительном материаловедении обозначается R.
Предел прочности равен напряжению, вызывающему разрушение материала, поэтому для нахождения предела прочности необходимо определить напряжение, при котором материал разрушается.
Например, чтобы определить предел прочности при сжатии бетона, необходимо сначала вычислить площадь грани образца, на которую будет распределена нагрузка, а затем на испытательной машине (прессе) зафиксировать разрушающую нагрузку в кгс или ньютонах.
После этого подсчитывают напряжение, при котором разрушился образец, т.е. предел прочности при сжатии RСЖ
На результат при определении предела прочности материала влияет множество факторов. Например, предел прочности при сжатии малых образцов получается выше, чем образцов большего размера. Влияет на результат испытаний и форма образца. Например, более предпочтительна форма цилиндра по сравнению с формой кубика. С увеличением размеров образца, главным образом его высоты, влияние сил трения снижается, под нагрузкой образец разрушается от поперечного разрушения.
Предел прочности материалов – условная величина, которая зависит от множества причин. Это размеры и конфигурация образцов, их температура и влажность, скорость приложения нагрузки и т.д.
Методы определения прочностных показателей различных материалов подробно прописаны в соответствующих нормативных документах.
Коэффициент конструктивного качества (ККК) – это характеристика относительной прочности материала, т.е. предела прочности по отношению к плотности.
Чтобы плотность перевести в безразмерную величину, пользуются понятием относительная прочность (т.е. по отношению к плотности воды), МПа:
В строительстве используют различные строительные материалы, выбирая те, у которых высокая величина этого коэффициента, т.е. высокая прочность при малой плотности, например, стеклопластик (225 МПа), древесину (200 МПа), сталь (50-120 МПа), бетон (10-50 МПа), кирпич (5,5 МПа).
9. Прочность при ударе, твердость, истираемость материалов и их определение.
Твердость – свойство материала сопротивляться проникновению в него другого, более твердого тела.
Твердость пластичных материалов, в частности металлов, наиболее часто определяют путем вдавливания в образец малодеформирующихся тел, изготовленных в виде шарика, конуса или пирамиды. В этом случае твердость характеризует свойство материала сопротивляться пластической деформации на поверхности образца.
Известен ряд способов определения твердости материалов посредством вдавливания твердого наконечника, например, метод Бринелля.
По этому методу в поверхность испытуемого образца вдавливается при заданной нагрузке шарик определенного диаметра из закаленной хромистой стали.
По результатам испытаний вычисляют число твердости учитывая нагрузку на шарик, площадь поверхности отпечатка, диаметр шарика, диаметр отпечатка.
Твердость хрупких материалов, например минералов или мономинеральных пород, можно характеризовать по условной десятибальной шкале Мооса, в которой в качестве эталонов принята твердость десяти минералов, расположенных по возрастающей твердости:
1 – тальк — 10 – алмаз.
Испытуемый материал имеет число твердости между эталонными минералами шкалы Мооса, из которых один чертит данный материал, а другой сам чертится испытуемым материалом.
Чем выше твердость материалов, тем больше сопротивление истиранию.
Истираемость – способность материала истираться тонкими слоями при трении его о другой, более твердый материал.
Сопротивление материала истиранию определяют на специальных машинах (кругах истирания) и выражают потерей массы образца, отнесенной к площади истирания.
Истираемость И, г/см2 вычисляют по формуле:
где — масса образца до и после испытания,
г; F – площадь истирания, см2.