Мокрый и сухой способ производства цемента: основные отличия
Так называемые «мокрая» и «сухая» технология производства цемента являются самыми распространенными способами получения этого незаменимого строительного материала.
СодержаниеСвернуть
Российские цементные заводы используют преимущественно «мокрый» метод, в то же время практически все зарубежные производители связующего работают по «сухой технологии».
Отличия мокрой технологии производства цемента от сухой
Обе технологии имеют свои преимущества и свои недостатки. Основной недостаток, которым отличается мокрый способ производства цемента – значительная энергоемкость процесса, отражающаяся на себестоимости конечного продукта. Сухая технология отличается большей экологической опасностью и соответственно большими капитальными затратами на устранение данного фактора. Рассмотрим оба способа производства цемента подробнее.
«Мокрая» технология производства связующего
Технологическая схема мокрого способа предусматривает раздельную первичную обработку компонентов клинкера. Измельченные «ингредиенты» загружаются в специальное оборудование для кратковременной выдержки под слоем воды. После этого компоненты клинкера, мокрыми, попадают в специальные мельницы, где их перемалывают до состояния порошка и тщательно перемешивают.
Подготовленный таким образом шлам подается в вертикальные и горизонтальные «шлюмбассейны» на корректировку необходимого соотношения «ингредиентов». Следующей технологической операцией идет печной обжиг откорректированного шлама и охлаждение промышленными холодильными установками. Полученный таким образом клинкер измельчается до мелкодисперсного порошка – цемента. Далее производятся: лабораторный анализ на соответствие цемента требованиям ГОСТ, фасовка и отправка потребителю.
Преимущества «мокрой» технологии
- Меньшие технологические затраты на измельчение сырья. Такие компоненты как мел и глина хорошо размокают в воде при первичной обработке в бассейнах. Соответственно процесс их измельчения происходит намного проще и легче;
- Транспортировка, усреднение и корректировка шлама происходит проще и экологически безопаснее, чем аналогичные операции при сухой технологии;
- В разы меньшее пылеобразование;
- Конструкция печей обжига шлама проста, надежна и имеет высокий Коэффициент Использования пространства – от 0,89 до 0,91;
- Имеется принципиальная возможность использовать сырьевые компоненты «пестрого» химсостава и хорошей гомогенизации шлама.
Недостатки
- Большой удельный расход тепловой энергии на обжиг сырья для производства цемента. Сырье поступающее на обжиг, имеет среднюю влажность 35-45%. Соответственно для испарения влаги и прогрев компонентов требуется порядка 5 450-6 800 кДж/кг тепловой энергии или 35% тепловой мощности печи. Поэтому часть обжиговой печи работает как сушильный агрегат со всеми вытекающими «неприятностями»;
- Высокая материалоемкость обжиговых печей при небольшой производительности.
Указанные недостатки выливаются в относительно низкую производительность труда, значительные технологические и эксплуатационные расходы, обуславливающие относительно высокую себестоимость производства.
«Сухая» технология производства связующего
В этом случае основное производственно-технологическое оборудование аналогично мокрому способу. Изменения заключаются в принципиально иной технологической схеме производства клинкера. После предварительного измельчения компоненты клинкера подаются в сушильные барабаны, причем каждый компонент подается в отдельный барабан. После сушки «ингредиенты» перемешиваются и поступают в общую мельницу для дальнейшего измельчения и ввода присадок.
Следующая операция обусловлена видом и влажностью глины. Все остальные компоненты корректируются по указанным параметрам глины. Суть операции заключается в незначительном увлажнении (не более 13% влажности) шлама и последующую подачу на обжиг. Соответственно небольшой влажности энергетические затраты на обжиг небольшие, а печи менее металлоемки и менее габаритны. Операции, следующие после обжига шлама, аналогичны предыдущему способу производства цемента.
Преимущества «сухой» технологии
- Относительно невысокий удельный расход тепловой энергии расходуемой на обжиг клинкера – 2 900-3 700 кДж/кг;
- Меньший на 30-40% объем печных газов при аналогичной производительности и возможность их вторичного использования для сушки компонентов. Это позволяет существенно снизить энергозатраты на производство клинкера и требует меньших капиталовложений на обеспыливание;
- Относительно меньшая металлоемкость обжиговых печей при большей производительности по сравнению с «мокрой» технологией. Производственная мощность печей при «сухом» способе – от 3 000 до 5 000 тонн продукта в сутки, что на 100-200% мощнее аналогичного оборудования работающего по «мокрой» технологии;
- Отсутствует необходимость в наличии мощных источников технологической воды.
Недостатки
- В разы большее пылевыделение, обуславливающее сложность обеспечения санитарных норм и охрану окружающего пространства;
- Относительная сложность конструкции обжиговых печей;
- «Капризность» обжиговых печей по отношению колебаний химсостава сырья, его дисперсности и степени важности;
- Относительно низкий Коэффициент Использования печей – от 0,7 до 0,8;
Более высокая трудоемкость энергоемкость на помол компонентов, обусловленные их низкой влажностью.
salecement.ru
Сухие строительные цементные смеси (на основе цемента)
Во время строительства и ремонтных работ широко используются готовые сухие строительные цементные смеси. Их использование позволяет ускорить сроки производства работ и повысить их качество. Для приготовления рабочего раствора того или иного назначения не требуется следить за правильной дозировкой компонентов, нужно просто затворить готовую смесь водой в количестве, указанном в инструкции.
Типы и характеристики цементно-песчаных смесей
Изобретение портландцемента оказало большое влияние на строительную отрасль, позволив заменить натуральный камень на искусственный — бетон. Также цемент стал неотъемлемым компонентом других материалов, без которых строительство теперь уже обойтись не может.
Цементно-песчаные составы (ЦПС) подразделяются на различные типы согласно следующим факторам:
- Удельный вес набравшего прочность состава. Согласно ему, все они делятся на 2 типа: облегченные плотностью до 1,5 т/м3 и тяжелые плотностью больше 1,5 т/м3.
- Функциональное назначение: штукатурные, кладочные, для стяжки, для устройства облицовки.
- Прочность отвердевшего материала на сжатие. Она имеет буквенно-цифровое обозначение, представляющее собой букву М и цифры, указывающие несущую способность в кг/см2.
- Количество вяжущих компонентов. В состав смеси в качестве вяжущего может входить не только цемент, но также гипс, известь полимеры и другие вещества.
- Содержание вяжущего в составе смеси. В этом плане все составы делятся на обедненные (соотношение песка и цемента более чем 5:1), нормальные (4:1) и жирные (3:1 и менее).
Характеристики состава определяются в основном концентрацией входящих в него компонентов.
От их пропорции зависят показатели запаса прочности и интенсивности твердения:- обедненные составы твердеют медленно, а затем со временем могут рассыпаться;
- жирные схватываются слишком быстро и часто растрескиваются.
Поэтому эксплуатационные характеристики материала зависят от правильно выбранной марки цемента и соблюдения рецептуры смеси.
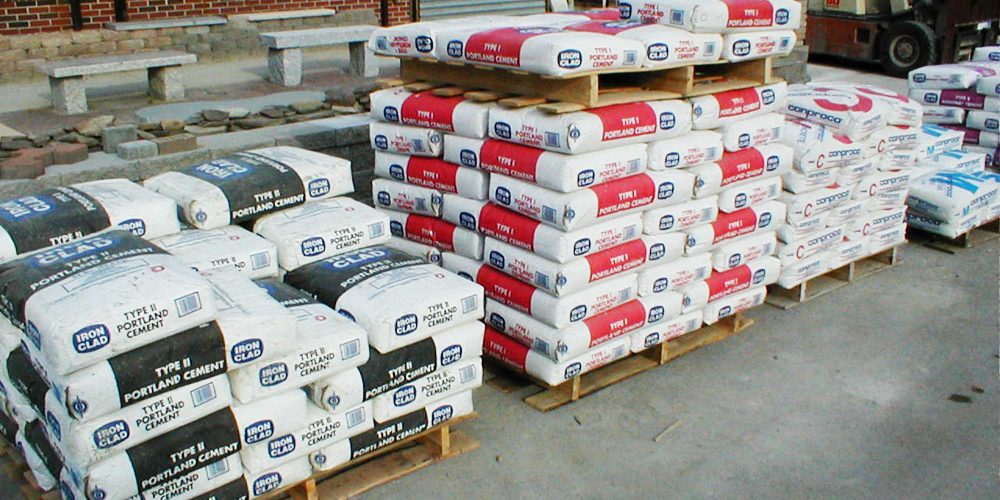
Основными характеристиками растворов, изготовленных на основе ЦПС, являются:
- набор эксплуатационной прочности в течение продолжительного времени;
- сохранение целостности в условиях перепада температур;
- пластичность, облегчающая выполнение работ;
- влагостойкость затвердевшего материала.
Виды сухих смесей на цементной основе состав и свойства
Показатели смеси зависят от ее назначения. Для придания материалу необходимых свойств в него могут быть введены различные добавки: пластификаторы, гидрофобизаторы, вещества для повышения морозостойкости и другие модификаторы. В качестве заполнителя может использоваться не только речной песок, но и минеральная крошка, перлит, волокна.
Для стяжки
Стяжка пола производится для придания ему необходимой ровности и водонепроницаемости. Эти свойства обеспечивают длительный срок эксплуатации финишного полового покрытия.
Готовые цементные стяжки различаются по составу и свойствам. Их можно разделить на следующие виды:
- Составы для чернового выравнивания. Их используют в ситуациях, когда основание пола имеет большие перепады по высоте. В этом случае толщина стяжки варьируется от 30 до 80 мм. Для изготовления смеси в данном случае применяются песок крупных фракций, мелкий керамзит, гранитная крошка. Непосредственно под половое покрытие такую стяжку использовать нельзя, поэтому приходится выполнять еще один слой — финишную стяжку.
- Финишная стяжка в составе содержит пластфикаторы и мелкий песок (до 0,6 мм). Это позволяет создать ровное и гладкое основание для пола. Толщина стяжки составляет не более 4 — 10 мм. При повышенных нагрузках на пол лучше сочетать стяжку с армирующей сеткой или приобрести смесь, в составе которой имеется армирующее фиброволокно.
- Самовыравнивающиеся стяжки. В их составе используется наполнитель с размерами частиц не более 0,3 мм и дополнительные добавки. Благодаря им, смесь имеет высокую текучесть и выравнивается на основании под воздействием силы тяжести. Толщина такой стяжки составляет не более 5 мм.
- Составы для теплых полов. Для их производства используются пластификаторы, способствующие удалению из смеси воздушных пузырьков, снижающих теплопередачу. Поэтому стяжка имеет высокую теплопроводность и не препятствует передаче тепла.
Гидроизоляция на основе цемента
Изоляция объекта от влаги является важной частью строительного процесса. Существуют следующие виды гидроизолирующих смесей на цементной основе:
- Цементно-песчаная гидроизоляция используется для защиты монолитных оснований. Промышленность выпускает смеси для ручного и машинного нанесения. В их состав нередко включают уплотняющие добавки. При слишком быстром испарении влаги из раствора нанесенный слой изоляции может деформироваться.
- Гидроизоляция цементная с добавлением латекса. Этот компонент позволяет получить раствор, по свойствам напоминающий жидкую резину. Наносится в горячем виде путем торкретирования. Надежно защищает поверхности от влаги и механических воздействий.
- Изоляция на основе цемента с добавлением жидкого стекла. Применяется для защиты фундаментов и цокольных этажей. Придает поверхности водонепроницаемость, огнеупорность, антисептические свойства. Имеет высокую адгезию к основной поверхности.
Материалы данного типа имеют невысокую стоимость, прочное сцепление с поверхностью и безопасны для здоровья.
Штукатурные смеси
В их основе такие вещества, как портландцемент, промытый и высушенный песок, вода. Для улучшения таких параметров, как эластичность, декоративность, прочность и стойкость могут использоваться дополнительные примеси.
Прочность штукатурной смеси зависит от марки вяжущего и составляет М25 — М100.
Готовые ЦПС бывают немодифицированными и модифицированными. Первые используются по бетону и кирпичу в качестве грунта и основного слоев и могут иметь достаточно большую толщину — до 50 мм. Вторые применяют как накрывочный слой, а также для оштукатуривания легких бетонов и в качестве тонкослойной штукатурки.
Декоративные штукатурки могут иметь в составе минеральные зерна и пигменты.
Шпаклевки
Шпаклевочные составы на основе цемента по назначению делятся на 2 вида:
- Стартовые — используются как базовый слой, способный устранить крупные дефекты основания стены. Растворы крупнозернистые, грубые, плохо шлифуются. Но при этом создают прочную основу. Толщина нанесения составляет не более 20 мм.
- Финишные — используются как чистовой слой. Структура раствора эластичная, заполнитель мелкий. Наносят слоем не более 1-4 мм. Обеспечивают гладкую поверхность, пригодную для обработки отделочными материалами.
Цвет смеси может быть белым, супербелым или серым. Стоимость последних ниже.
Плиточный клей
Основой плиточного клея является песчано-цементная смесь. Ее объем составляет 95% объема клея. Остальные 5 % приходятся на различные присадки:
- гидрофобизаторы;
- антисептики;
- катализаторы для замедления или ускорения схватывания клея;
- пластификаторы;
- противоморозные добавки.
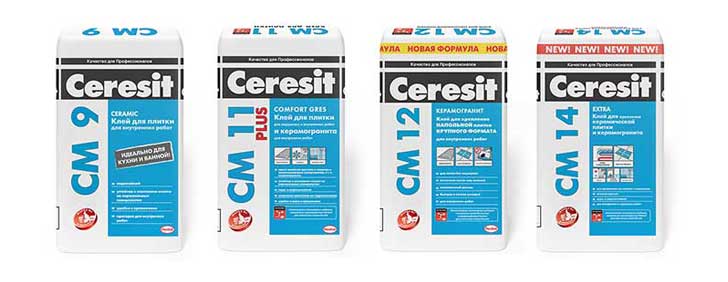
В зависимости от вида наклеиваемой плитки меняется и состав клея. Некоторые виды клеев можно использовать только для мелкоразмерной легкой плитки.
Для крупноразмерных элементов и плит из натурального камня производят смеси со специальными присадками.
Выпускается 2 вида клеев:
- только для внутренних работ;
- для внутренних и наружных работ.
Как приготовить песчано цементную смесь своими руками
Для приготовления смеси необходимо знать, в какой пропорции закладываются компоненты.
Это зависит от ее назначения.
Порядок действий следующий:
- Песок просеивают, причем для сухого песка используется сито с ячейкой 2 мм, а для сырого — 4 мм.
- В чистую емкость наливают 2-3 л воды.
- Затем добавляют цемент и тщательно перемешивают миксером или лопатой до тех пор, пока материал не станет однородным.
- Согласно пропорции, в емкость добавляют подготовленный песок и другие наполнители и модификаторы.
- Смесь снова вымешивают до однородной консистенции. При необходимости добавляют чистую воду или небольшое количество песка.
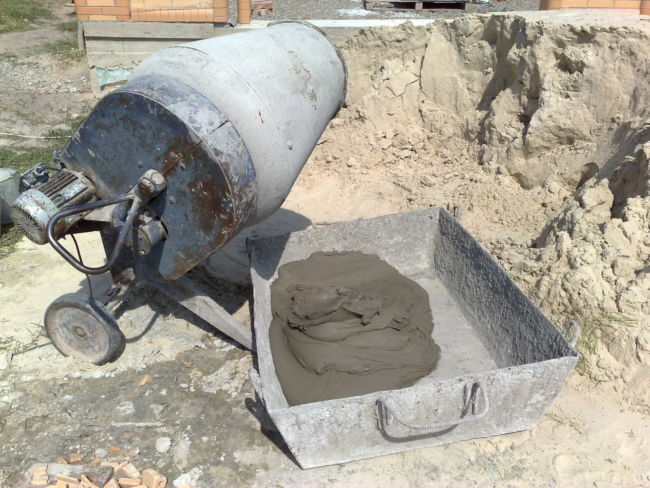
Нормы расхода
Расход ЦПС зависит от нескольких факторов:
- ее назначения;
- качества базовой поверхности.
Но есть усредненные нормы:
Наименование ЦПС | Единица измерения | Расход |
Плиточный клей | 1 м2 | 10 кг при толщине слоя 10 мм |
Клей для керамогранита | 1 м2 | 10 кг при толщине слоя 10 мм |
Клей для пенобетона | 1м3 уложенных блоков | 40 кг |
Клей для газосиликата | 1м3 уложенных блоков | 40 кг |
Наливной пол | 1 м2 | 10 кг при толщине слоя 10 мм |
Самовыравнивающийся пол | 1 м2 | 6 кг при толщине слоя 5 мм |
Пескобетон | 1м3 готового раствора | 1400 кг сухой смеси |
Штукатурка | 1 м2 | 10 кг при толщине слоя 10 мм |
Шпаклевка | 1 м2 | 1 кг |
Смесь М150 | 1м3 готового раствора | 1450 кг сухой смеси |
Монтажно-кладочная смесь М 200 | 1м3 кладки | 350 кг сухой смеси |
Гидроизоляция | 1 м2 поверхности | 0,7 кг сухой смеси |
Затирка для кафельной плитки | 1 м2 уложенной плитки | 0,12 кг при толщине шва 2 мм |
Средняя величина расхода материала указана на каждой упаковке.
Маркировка цементно-песчаных составов
Марка смеси зависит от соотношения в ее составе песка и цемента. Определяющим фактором здесь является назначение ЦПС, которое диктует требования к ее прочностным характеристикам.
Часто используемые марки ЦПС и типы работ, для которых они применяются:
- М100 — раствор, приготовленный из нее, используется для выполнения черновой штукатурки стен, заделки небольших выбоин и трещин.
- М150 — универсальный вариант, широко применяемый в строительстве. Смесь можно использовать для стяжки, штукатурки, в качестве кладочного раствора при возведении стен из кирпича и блоков.
- М200 — мало отличается от М100, имеет примерно ту же сферу применения, но быстрее схватывается и обладает большей твердостью готовой поверхности.
- М300 — пескобетон, именуемый как «фундаментная марка». Незаменим при повышенных требованиях к твердости и прочности поверхности — для фундаментов, толстых стяжек, кладки из блоков. Непригодна для оштукатуривания.
- М400 — применяют для создания конструкций повышенной прочности: фундаментов, износостойких стяжек в местах с высокой проходимостью. Быстро твердеет, требует быстрой выработки.
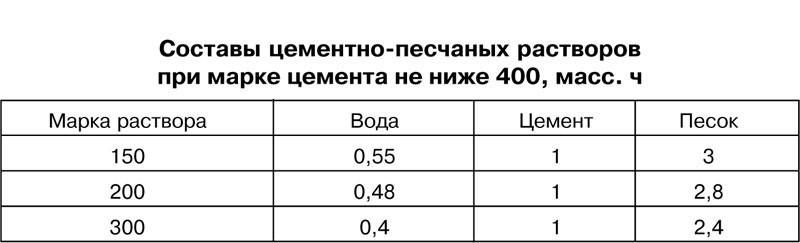
Популярные производители сухих смесей
Сухие смеси пользуются большим спросом как в частном малоэтажном, так и в промышленном строительстве. Их производят как зарубежные, так и российские предприятия.
Наиболее надежными считаются следующие компании: Церезит, Юнис, Кнауф, МКУ, Волма, Русеан.
1beton.info
технологические отличия и показатели. Какой метод получения цемента выбрать?
Существует несколько методов изготовления цемента: мокрый, полусухой, комбинированный и сухой. Основными способами, которые применяются на ведущих заводах, являются сухой и мокрый.
Мокрый способ производства цемента
Схема изготовления цемента мокрым методом представлена на рисунке ниже.
Производство начинается с извлечения из карьеров твердого известняка, который впоследствии дробится на куски различного размера. Затем куски измельчаются в дробильных агрегатах, пока размеры частей известняка не будут превышать 8-10 мм.
Затем на мини-завод транспортируют глину из карьера и обрабатывают ее в вальцевых дробилках до той степени, пока размер кусочков будет достигать от 0 до 100 мм.
Далее измельченную смесь отмачивают в болтушках. В результате получается шлам из глины, влажность которого составляет до 70 %.
Затем он поступает в мельницу, где происходит процесс смешивания и размалывания с известняковой массой.
После этого шлам влажностью около 40 % направляется в вертикальный бассейн, в котором выполняется окончательный процесс корректировки. Эта операция имеет исключительное значение, так как на этом этапе обеспечивается химическая формула состава произведенного шлама.
Только после того как шлам пройдет контроль качества, он допускается к последующим этапам. Далее цементная масса транспортируется из вертикального оборудования (бассейна) в горизонтальный, в котором происходит хранение смеси перед поступлением в печь обжига. В горизонтальном бассейне сырьевая масса постоянно помешивается механическим путем с применением сжатого воздуха. Благодаря этому шлам не выпадает в осадок и полностью гомогенизируется. Если в процессе изготовления цемента применяются сырьевые компоненты, что имеют неизменный химический состав, то корректировка химического состава шлама осуществляется в горизонтальном бассейне.
Затем шлам направляется в печь для обжига, в которой он превращается в клинкер. Полученная клинкерная основа цемента поступает в промышленный холодильник для охлаждения. После этого клинкер подвергается дроблению и подается в бункеры мельниц. Там клинкерная масса повторно измельчается.
Если для процесса обжига шлама используется твердое топливо, то возникает необходимость в строительстве дополнительного помещения для хранения и подготовки угля. Когда в производственном процессе применяется жидкое или газообразное топливо, то схема обжига клинкерной смеси имеет упрощенный вид.
В завершение цемент перенаправляется из бункеров мельниц в специальные помещения для хранения. На этом производственном этапе лаборанты осуществляют контроль качества продукции и определяют марку цемента. Только после этого продукция направляется в упаковочные аппараты.
Сухой способ производства цемента
Схема изготовления цемента сухим методом представлена на рисунке ниже.
Во время производства цемента сухим методом используется другая технологическая схема. Глина и известняк, добытые из карьера, после дробления направляются в сепараторную мельницу, где осуществляется помол, смешивание и сушка сырьевых компонентов. Полученная смесь направляется к смесительным аппаратам, где выполняется окончательное смешивание с применением сжатого воздуха. На данном этапе осуществляется корректировка химического состава цементной смеси.
Если применяется глинистый компонент, то сырьевая смесь подается для смешивания в шнеки, в которых происходит частичное увлажнение водой. На этом этапе образуются прочные гранулы, что имеют влажность не более 14 % — далее они поступают в печь для обжига.
При сухом методе производства процесс обжига сырья может выполняться в различных печах, здесь особое внимание уделяется приготовлению сырьевой массы. Дальнейшие этапы технологического процесса осуществляются так же, как и при мокром методе производства.
Особенности полусухого способа производства
Схема изготовления цемента полусухим методом представлена на следующем рисунке.
Полусухой метод производства цемента очень похож на сухой, но отличия все же есть.
Размер муки, что проходит стадию гранулирования, составляет 10-20 мм, а влажность 11-16 %. Сырье обжигается в печах Леполь и после этого образовавшиеся гранулы направляются на конвейерный кальцинатор.
Из печки выделяются газы, что проходят сквозь гранулы на решетке. В результате этого происходит их нагрев до 900 ºС и они полностью высушиваются. Во время такой термообработки выполняется декарбонизация смеси на 22-30 %, что важно для производства. По завершению этих процессов сырье направляется в печь, где и завершается процесс изготовления цемента. Обжиг гранулированного цемента может происходить в шахтных печах. При этом гранулирование выполняется с частицами угля, после этого цемент направляется на хранение.
Комбинированный метод производства цемента
Схема изготовления цемента комбинированным методом отображена на рисунке ниже.
Этот метод основывается на подготовке сырьевых компонентов по мокрому способу, а их обжиге – по схеме полусухого способа. Полученный в сырьевой мельнице шлам влажностью 30-45 % поступает в специальный фильтр, в котором он обезвоживается до влажности 15-20 %. Далее сырьевая смесь смешивается с пылью, что снижает влажность до 12-14 %.
Затем смесь поступает на обжиг, который выполняется в печах полусухого метода изготовления цемента. Остальные операции комбинированного метода не отличаются от этапов мокрого способа производства.
Методы производства выбирают исходя из технико-экономических и технологических факторов: свойств сырьевых компонентов, однородности и влажности смеси, наличия мощной топливной базы и других.
Полезное и важное по теме:
Поделитесь статьей с друзьями:
vproizvodstvo.ru
Сухая цементная смесь: состав, особенности и виды применения
Для чего может употребляться сухая цементная смесь в мешках? Из каких компонентов она состоит? Какие конкретно виды сухих смесей возможно встретить в продаже? Как обрабатывается приготовленный на их базе бетон до полного комплекта марочной прочности? Позволяйте разбираться.
Легко добавь воды
Считается, что приготовить бетон на протяжении строительства несложно своими руками. Компоненты общеизвестны — портландцемент в качестве связующего, щебень и песок в качестве заполнителя.
Уточним: при необходимости получения материала с улучшенными тепло- и шумоизоляционными свойствами употребляются пористые заполнители (керамзит, перлит и т.д.). Попадаются они и среди готовых смесей: так, сухая смесь Полистиролбетон в качестве заполнителя применяет… пенопластовые шарики.
В зависимости от соотношения компонентов возможно взять бетон с различными свойствами. Посильнее всего пропорции воздействуют на марочную прочность.
Марка по прочности | Соотношение цемента, щебня и песка |
М100 | 1 : 4,6 : 7 |
М150 | 1 : 3,5 : 5,7 |
М200 | 1 : 2,8 : 4,8 |
М250 | 1 : 2,1 : 3,9 |
М300 | 1 : 1,9 : 3,7 |
М400 | 1 : 1,2 : 2,7 |
При независимом приготовлении, но, полученный продукт будет неизбежно иметь громадный разброс свойств от партии к партии.
Обстоятельства?
- При замешивании вручную тяжело выдержать правильную дозировку и пропорции.
- Цемент из различных партий владеет заметно отличающимися вяжущими свойствами.
- На прочность бетона очень сильно воздействует количество прочих загрязнений и пыли, неизбежно попадающих в него при замешивании.
К счастью, имеется предельно несложный метод упростить себе задачу. Сухие смеси для бетона содержат совершенно верно дозированные компоненты без посторонних примесей. В их составе не достаточно только затворяющей смесь воды.
Приготовление
Инструкция по приготовлению бетона из сухой смеси не отличается сложностью.
В качестве примера давайте узнаем, как готовится к применению сухая смесь Пескобетон М300.
- В чистую емкость заливается вода комнатной температуры в количестве 1,5 — 1,6 литра на 10 килограммов смеси.
- После этого засыпается фактически смесь.
Обратите внимание: в случае если сделать напротив — добавить воду в сухой продукт — на дне емкости образуются плотные комки, каковые будет достаточно тяжело разбить.
- Раствор перемешивается до однородной консистенции строительным миксером либо дрелью с соответствующей насадкой. По окончании 5-повторного перемешивания и минутной выдержки он готов к применению. Срок жизнеспособности — 120 мин..
Типы смесей
Сухие смеси из цемента для бетона классифицируются в первую очередь по области применения.
Штукатурные
blog-oremonte.ru
Способы производства цемента
Процесс производства цемента состоит из следующих основных технологических операций: добычи сырьевых материалов; приготовления сырьевой смеси, обжига сырьевой смеси и получения цементного клинкера; помола клинкера в тонкий порошок с небольшим количеством некоторых добавок.
В зависимости от способа подготовки сырья к обжигу различают мокрый, сухой и комбинированный способы производства цементного клинкера.
При мокром способе производства измельчение сырьевых материалов, их перемешивание, усреднение и корректирование сырьевой смеси осуществляется в присутствии определенного количества воды. А при сухом способе все перечисленные операции выполняются с сухими материалами. Мокрый способ приготовления сырьевой смеси применяют, когда физические свойства сырьевых компонентов (пластичной глины, известняка, мела с высокой влажностью и т.д.) не позволяют организовывать экономичный технологический процесс производства сырьевой смеси по сухому способу производства. При комбинированном способе сырьевую смесь приготовляют по мокрому способу, затем ее максимально обезвоживают (фильтруют) на специальных установках и в виде полусухой массы обжигают в печи. Каждый из перечисленных способов имеет свои достоинства и недостатки.
Способ производства цемента выбирают в зависимости от технологических и технико-экономических факторов: свойств сырья, его однородности и влажности, наличия достаточной топливной базы и др.
Мокрый способ производства цемента.
Сухой способ производства цемента.
Комбинированный способ производства цемента.
Производство цемента складывается в основном из следующий операций: добыча сырья; приготовления сырьевой смеси, состоящего из дробления и ее гомогенизации; обжига сырьевой смеси; помола обожженного продукта (клинкера) в тонкий порошок.
Существуют два основных способа производства – мокрый и сухой. При мокром способе производства сырьевую смесь измельчают и смешивают сырьевые материалы с водой. Получаемая сметанообразная жидкость – шлам – содержит 32-45% воды. По сухому способу сырьевые материалы предварительно высушивают, а затем измельчают и смешивают. Полученный тонкий порошок называют сырьевой мукой.
В зависимости от физических свойств исходных материалов и ряда других факторов при получении цемента по мокрому способу применяют разные схемы производства. Схемы эти отличаются одна от другой только способом приготовления сырьевой смеси. Приводим схему производства цемента по мокрому способу из твердого материала — известняка — и мягкого — глины.
При трехкомпонентной сырьевой смеси корректирующую добавку дробят, после чего она попадает в бункер, откуда вместе с известняком поступает в мельницу. Глину до болтушки пропускают через валковую дробилку. Сырьевые материалы дозируют перед мельницей специальными питателями.
Если при производстве по мокрому способу сырьевую смесь составляют из одних твердых материалов — известняка, мергелей и глинистых сланцев, то их дробят в дробилках без добавки воды и размалывают совместно в мельнице, куда добавляют воду. В том случае в схеме отсутствует болтушка. При изготовлении цемента из одних мягких материалов (мела, глины, мягких мергелей) сырье измельчают в болтушках, после чего размалывают в более коротких шаровых мельницах. В этом случае воду добавляют в первой стадии процесса и материалы дозируют перед ,поступлением в болтушки.
При сухом способе производства выбор схемы зависит от рода поставляемого топлива, физических свойств сырья, мощности завода и ряда других факторов. При использовании для обжига клинкера угля с большим содержанием летучих обжиг ведут во вращающихся печах, — если же применяют топливо с малым содержанием летучих — то в шахтных.
Так как при соприкосновении мелкого порошка, образующегося при помоле, с влагой материала образуется пластичная масса, которая налипает на внутреннюю поверхность агрегата и препятствует дальнейшему помолу, то дробленые сырьевые материалы с естественной влажностью размалывать нельзя. Поэтому после выхода из дробилки сырьевые материалы высушивают и затем направляют в мельницу, где перемалывают в тонкий порошок. Однородные по физическим свойствам материалы можно дробить и сушить в одних и тех же аппаратах. В случае применения гранулированного шлака его подсушивают без предварительного дробления. Помол и сушку сырьевой смеси целесообразно вести одновременно в одном аппарате-мельнице — в том случае, если влажность сырьевых материалов не превышает 8-12%, например, при использовании известняков и глинистых сланцев. Если в качестве сырья используется непластичный глинистый компонент, то при сухом способе производства обжиг ведут только во вращающихся печах. При пластичном глинистом компоненте можно вести обжиг, как во вращающихся печах, так и в шахтных печах. В последнем случае сырьевую смесь вначале увлажняют в смесительных шнеках водой до 8-10%-ной влажности. Затем массу подают в грануляторы, где она вместе с дополнительно подводимой водой превращается в гранулы с влажностью 12-14%. Эти гранулы и поступают в печь.
При обжиге клинкера на газообразном или жидком топливе схема производства упрощается, так как отпадает необходимость в приготовлении угольного порошка.
В ряде случаев может оказаться целесообразным комбинированный способ производства, при котором сырьевая смесь в виде шлама, полученного при обычном мокром способе производства, подвергается обезвоживанию и грануляции, а затем обжигается в печах, работающих по сухому способу.
Выбор сухого или мокрого способа производства зависит от многих причин. Как тот, так и другой способ имеют ряд преимуществ и недостатков. При мокром способе легче получить однородную (гомогенизированную) сырьевую смесь, обуславливающую высокие качества клинкера. Поэтому при значительных колебаниях в химическом составе известнякового и глинистого компонента он целесообразнее. Этот способ используется и тогда, когда сырьевые материалы имеют высокую влажность, мягкую структуру и легко диспергируются водой. Наличие в глине посторонних примесей, для удаления которых необходимо отмучивание, также предопределяет выбор мокрого способа. Размол сырья в присутствии воды облегчается, и на измельчение расходуется меньше энергии. Недостаток мокрого способа — больший расход топлива. Если используют сырьевые материалы с большой влажностью, то расход тепла, затрачиваемого на сушку и обжиг, при сухом способе будет мало отличаться от расхода тепла на обжиг шлама при мокром способе. Поэтому сухой способ производства целесообразнее при сырье со сравнительно небольшой влажностью и однородным составом. Он же практикуется в случае, если в сырьевую смесь вместо глины вводят гранулированный доменный шлак. Его же применяют при использовании натуральных мергелей и тощих сортов каменного угля ,с малым содержанием летучих, сжигаемых в шахтных печах.
При изготовлении сырьевой смеси по любому способу необходимо стремиться к наиболее тонкому помолу, теснейшему смешению сырьевых материалов и к возможно большей однородности сырьевой смеси. Все это гарантирует однородность выпускаемого продукта и является одним из необходимых условий нормальной эксплуатации завода. Резкие колебания химического со·става сырьевой смеси нарушают ход производственного процесса. Высокая тонкость помола и совершенное смешение необходимы для того, чтобы химическое взаимодействие между отдельными составными частями сырьевой смеси прошло до конца в возможно более короткий срок.
При выборе той или другой схемы производства особое внимание следует обращать на рентабельность работы предприятия и возможность снижения себестоимости продукции. Основными мероприятиями, ведущими к снижению себестоимости являются: интенсификация производственных процессов, повышение коэффициента использования оборудования, рост выпуска цемента, повышение его качества (марки), снижение расхода топлива и электроэнергии, механизация производственных процессов и всех вспомогательных работ, автоматизация управления производственными процессами и некоторые другие.
Мощность цементных заводов устанавливают в зависимости от сырьевой базы и потребности района в цементе. На новых заводах она равна обычно 1-2 млн. т цемента в год. Характерным показателем производительности труда на цементных заводах является выпуск цемента на одного рабочего в год, который в 1963 г. составил 915 т. Выработка на одного работающего была 7-62 т. На заводах, оснащенных высокопроизводительным оборудованием, выработка цемента достигла соответственно 2000 и 1600 т.
На цементных заводах, а также на заводах по производству других вяжущих материалов приходится перемещать от одного аппарата к другому большие массы кускового порошкообразного и жидкого материала. Для транспортирования их применяют ковшовые элеваторы, шнеки, ленточные, пластинчатые и скребковые транспортеры, транспортные желоба, насосы, краны с грейферами. Для транспортирования порошкообразных материалов широко используют пневмовантовые и камерные насосы, а также пневмотранспортные желоба.
Транспортирование шлама имеет ряд особенностей, так как он представляет собой сметанообразную текучую массу, содержащую 32-45% воды. Чтобы уменьшить расход топлива на обжиг, стремятся снизить влажность шлама, а чтобы улучшить его транспортабельность, необходимо увеличить содержание воды. По условиям транспортабельности шлам должен течь по желобу, имеющему уклон в 2-4 %. Чем пластичнее сырьевые материалы, тем больше приходится добавлять воды для получения шлама нужной текучести. Обычно шлам транспортируется центробежными насосами.
На заводы сырьевые материалы доставляют из карьера в виде кусков размерами до 1000-1200 мм. Иногда сырьевые отделения расположены непосредственно на карьерах, откуда шлам поступает на заводы. Так, на Балаклейском цементном заводе отделение болтушек размещено на карьере. Сырьевые материалы в виде мела и глины поступают в дробилки, а затем в болтушки. Полученный глиняно-меловой шлам нормальной влажности перекачивается по шламопроводам на завод.
При выпуске цемента обычных марок сырьевые материалы и клинкер размалываются до остатка на сите №008 порядка 8-10%. Для получения цемента более высоких марок материалы размалываю тоньше — до остатка на том же сите около 5% и даже меньше. Измельчать сырьевые материалы до получения тонкого порошка в одном аппарате невозможно. Поэтому сначала материал подвергают в дробилках двyx — тpex стадийному дроблению до величины кусков, не превышающей 8-20 мм, а затем измельчают в мельницах в гонкий порошок с размерами зерен не более 0,06-0,10 мм, глину поступающую из карьера в кусках размером до 500 ММ, измельчают в валковых дробилках до кусков не больше 100 мм, а затем отмучивают в болтушках до получения глиняного шлама с влажностью 60-70%. Этот шлам и подают в сырьевую мельницу.
Удельный расход сырья зависит от его химического состава и зольности топлива и составляет 1,5-2,4 т на 1 т клинкера. Расход электроэнергии на 1 т выпускаемого цемента составляет 80-100 квт/ч.
www.voscem.ru
Сравнительный анализ затрат электроэнергии и топлива при сухом и мокром способах производства цемента
ВОПРОС: Виктор Иванович Хлудеев, генеральный директор, ЗАО «Белгородский цемент», Россия:Приведите сравнительный анализ энергоемкости (расхода электроэнергии и топлива) сухого и мокрого способов производства цемента с учетом расхода электроэнергии на общую выработку сжатого воздуха, добычу и подготовку сырья, обжиг клинкера и помол цемента.
ОТВЕТ: Виктор Корнеевич Классен, д-р техн. наук, проф., БГТУ им В.Г. Шухова, Россия:
Удельный расход топлива и электроэнергии, как известно, зависит от вида сырья и оборудования, способа производства и технологической дисциплины. Поэтому приведем наилучшие результаты, полученные в отечественной и зарубежной промышленности при применении новейших технологий и использовании традиционного сырья, состоящего из карбоната кальция, глины и железосодержащей добавки. В связи с тем, что затраты энергии на помол цемента практически не зависят от способа производства, сравнение показателей приведено в основном для получения клинкера.
1. Удельный расход тепла на обжиг цементного клинкера
1.1. Расход тепла при мокром способе. При мокром способе производства расход тепла, естественно, определяется влажностью шлама и видом оборудования. При использовании традиционного способа с современными длинными вращающимися печами зависимость удельного расхода условного топлива от влажности шлама показана на рис. 1, кривая 1. Приведенные результаты свидетельствуют, что при влажности шлама, равной 39 %, удельный расход условного топлива может составлять 200 кут/т клинкера, что соответствует 1400 ккал/кг или 5860 кДж/кг.
При влажности 33 % эти значения будут равны соответственно ~175 кут/т, 1225 ккал/кг, 5130 кДж/кг
клинкера.
При мокром способе с дробилкой-сушилкой и современной печной системой с декарбонизатором (рис. 2) удельный расход тепла может быть снижен несколько более чем на 10 %, и при влажности шлама W=39 % расход условного топлива будет составлять 175 кут/т клинкера, а при 33 % — 155 (рис. 1, кривая 2). Подобная схема реализована немецкой фирмой Polysius на заводе Rugby в Великобритании (рис. 2).
1.2. Расход тепла при комбинированном и сухом
способах производства. При комбинированном (когда шлам частично обезвоживается на фильтр-прессах до влажности ~20 %) или сухом способе производства наиболее рациональной является современная схема с декарбонизатором и многоступенчатым циклонным теплообменником. Зависимость расхода тепла от влажности исходной сырьевой смеси показана на рис. 3. Для обеспечения сушки сырья соответствующей влажности необходимая температура отходящих из теплообменника газов достигается изменением числа ступеней циклонов. Так, при влажности исходного сырья до 5 % удельный расход топлива может составлять 100 кут/т клинкера (кривая 1) при установке пяти—шести циклонов и температуре за теплообменником 300—250 °С. При дополнительном использовании избыточного воздуха из холодильника эта величина снизится до 95 кут/т (рис. 3, кривая 2). Если же влажность сырьевой смеси составит примерно 20 %, то при трех ступенях циклонов эти значения будут соответственно равны ~125 кут/т и ~118 кут/т клинкера (рис. 3, кривые 1, 2).
2. Удельный расход электроэнергии для производства клинкера
2.1. Расход электроэнергии при использовании легко размалываемого сырья повышенной влажности. При использовании легко размалываемых сырьевых компонентов повышенной влажности, например, мела, мергеля и глины, расход электроэнергии на производство клинкера принят по данным передовых российских и зарубежных заводов.
Результаты по мокрому способу приняты по данным заводов «Осколцемент», «Белгородский цемент» и «Себряковцемент» для вращающихся печей размерами 5 × 185 и 4,5 × 170 м при влажности шлама 38—40 %.
Комбинированный способ представлен заводом Lägerdorf, Германия, где он реализован фирмой Polysius. Обезвоживание шлама на нем производится фильтр-прессами до влажности кека ~20 %, дальнейшая сушка и обжиг которого производится по схеме, приведенной на рис. 2, только не с двух-, а с трехступенчатым циклонным теплообменником.
Параметры для сухого способа при сырье с влажностью ~25 % и технологической схемы с вертикальной валковой мельницей, четырехступенчатым циклонным теплообменником, декарбонизатором и газотурбинной установкой (рис. 5) приняты по проектным данным немецкой фирмы KHD Humboldt Wedag для ОАО «Мордовцемент».
Результаты по отдельным переделам производства приведены в табл. 1 и свидетельствуют, что при использовании легко размалываемого сырья повышенной влажности и высокой организации технологического процесса удельный расход электроэнергии на производство клинкера составляет для традиционного мокрого способа ~42, для комбинированного ~52, для сухого ~66 кВт·ч/т.
2.2. Расход электроэнергии при использовании трудно размалываемого сырья пониженной влажности. При использовании трудно размалываемых сырьевых компонентов пониженной влажности, в частности известняка, расход электроэнергии на производство клинкера для традиционного мокрого способа принят по результатам работы передовых российских заводов и данным отечественных и зарубежных публикаций. Результаты по сухому способу с вертикальной валковой мельницей фирм Polysius и Gebr. Pfeiffer
, Германия, взяты из опыта работы многих зарубежных заводов. За основу расхода электроэнергии при использовании для помола сырья пресс-валкового измельчителя (роллер-пресса) приняты эксплуатационные параметры нового Новотроицкого цементного завода с учетом данных, полученных фирмами KHD Humboldt Wedag и Polysius на зарубежных заводах.
Результаты по отдельным переделам производства для мокрого и сухого способов при применении различного оборудования приведены в табл. 2 и свидетельствуют, что расход электроэнергии на производство клинкера составляет для традиционного мокрого способа около 62, сухого (1960-х годов) с шаровой мельницей ~82 кВт·ч/т, сухого с вертикальной валковой мельницей ~60, сухого с роллер-прессом ~56 кВт·ч/т.
Эти данные свидетельствуют, что для современного оборудования расход электроэнергии при сухом способе несколько ниже, чем при мокром. Для устаревшего оборудования 1960-х годов наблюдалась противоположная ситуация — потребление электроэнергии при сухом способе превышало его значение в сравнении с мокрым на 20 кВт·ч/т клинкера.
3. Анализ приведенных данных
3.1. Использование циклонных теплообменников с низким сопротивлением. Отметим, что существенное снижение расхода электроэнергии при сухом способе с циклонными теплообменниками по сравнению с подобными заводами 1960—1970-х годов обусловлено созданием новых циклонов, в которых газодинамическое сопротивление каждой ступени снизилось в 2 раза, с ~20 до ~10 мбар, и возросла степень очистки.
Принципиальная теоретическая основа полученного эффекта показана на рис. 4 и заключается в том, что в традиционном циклоне совмещены оси циклона и погружной трубы, поэтому по окружности сохраняется проходное сечение F. Так как газы постепенно уходят вверх через погружную трубу, уменьшается окружная скорость газа v и изменяется интенсивность осаждения пыли. Учитывая, что вначале скорость равна ~20 м/с, а в конце снижается до 5, активная область пылеулавливания будет составлять около 150° окружности циклона. При этом вследствие высокой входной скорости возникнет большое газодинамическое сопротивление ΔР, так как оно пропорционально квадрату скорости газового потока (ΔР~ k·v 2).
После реконструкции при смещении оси погружной трубы скорость пылегазового потока на входе в циклон, по данным фирмы KHD Humboldt Wedag, может быть снижена до 14 м/с. В этом случае сопротивление циклона уменьшится в 2 раза: ΔР1/ΔР2 = v1 2/v22 = 202/142 = 400/196 ≈ 2, и вследствие этого потребляемая дымососом электрическая мощность N = k·V·ΔР также снизится в 2 раза (здесь V — объемный расход газа). Кроме того, из-за уменьшения и выравнивания скорости по окружности циклона до 9—14 м/с активная зона пылеулавливания увеличивается до 270° и, следовательно, возрастает степень очистки циклонов до 0,90—0,96 %. Это снижает степень циркуляции пыли в системе теплообменников и, следовательно, приводит к дополнительной экономии электроэнергии и топлива.
3.2. Применение рациональной схемы сухого способа с газотурбинной установкой. Если при использовании сырья с повышенной влажностью применить схему, представленную на рис. 2, то необходимые газы на сушку поступают через декарбонизатор и все циклоны. Так, например, при влажности сырья 25 % объем избыточного газа, просасываемого через теплообменник, составит 0,56 нм3/кг, или 29 %. Так как расход электроэнергии на транспортировку газа вентилятором, согласно выражению N = k·V·ΔР, пропорционален объемному расходу газа V и напору ΔР, то на 29 % увеличится нагрузка на печной дымосос. В этих условиях, чтобы сохранить сопротивление системы, следует увеличить сечение газоходов и циклонов на те же 29 %. Поэтому целесообразно независимо от влажности исходного сырья устанавливать пятиступенчатый теплообменник и газотурбинную установку (ГТУ) для выработки электроэнергии с использованием отходящих из нее газов для сушки сырья (рис. 5). При этом сушильный агент напрямую подается в сушильный агрегат и, следовательно, циклоны разгружаются от избыточного газового потока. Такая схема обеспечивает экономию электроэнергии и снижает расход топлива вследствие утилизации тепла отходящих газов из ГТУ. При этом можно получить электроэнергию, достаточную для покрытия собственных нужд цементного производства.
3.3. Энергосберегающие способы измельчения. Эксплуатационные параметры, достигнутые на многих передовых цементных заводах (табл. 3), свидетельствуют, что наряду с экономией электроэнергии за счет применения новых циклонных теплообменников значительное снижение энергозатрат достигается путем использования более совершенных помольных агрегатов. Так, применение вертикальных валковых мельниц (ВВМ) и пресс-валков высокого давления (роллер-прессов РП) позволило в сравнении с шаровыми мельницами снизить расход электроэнергии на помол сырья при использовании твердых компонентов с 22—24 до 13—15 кВт·ч/т, т. е. в среднем примерно на 9 кВт·ч/т сырья. В пересчете на тонну клинкера экономия составит примерно 9 × 1,54 ≈ 14 кВт·ч, причем расход электроэнергии при сухом способе существенно ниже, чем при мокром. Для легко размалываемого сырья с влажностью ~25 % значительное преимущество в сравнении с сухим способом имеет мокрый помол — затраты энергии соответственно равны 21 и 7 кВт·ч/т сырья, или 32 и 11 кВт·ч/т клинкера. В этом случае основные затраты электроэнергии (более 75 %) связаны с работой вентилятора, транспортирующего повышенный объем пылегазового потока через помольный агрегат, сепаратор, циклоны и электрофильтр.
Помол цемента преимущественно осуществляется в шаровых мельницах. При использовании современных замкнутых схем помола цемента расход электроэнергии на работу мельницы, динамического сепаратора с вентилятором, элеватора, аспирационной системы и питателей может достигать ~33 кВт·ч/т при удельной поверхности 3000 см2/г по Блейну. В случае применения пневмотранспорта на него дополнительно требуется еще ~12 кВт·ч/т. Таким образом, сумма затрат на помол бездобавочного портландцемента составит около 45 кВт·ч/т. В случае замены пневмотранспорта на механический расход электроэнергии на транспорт снижается практически в 10 раз и, следовательно, составит всего около 1,2 кВт·ч/т. В этом случае суммарные затраты на помол цемента снизятся примерно до 34 кВт·ч/т. Дополнительно уменьшить расход электроэнергии можно путем предварительного измельчения клинкера роллер-прессом. При этом в зависимости от применяемой схемы обеспечивается снижение расхода электроэнергии на 15—30 %.
На хранение, упаковку и отгрузку цемента расходуется ~3 кВт·ч/т.
4. Заключение
Таким образом, на основании опыта работы передовых отечественных и зарубежных предприятий можно сделать обоснованное заключение о реальном достижении следующих результатов:
• расход условного топлива на тонну клинкера в зависимости от способа составляет:
– для традиционного мокрого ~200 кг;
– для мокрого с теплообменниками и декарбонизатором ~175 кг;
– для комбинированного ~120 кг;
– для сухого ~100 кг;
• расход электроэнергии может составлять ниже 100 кВт·ч/т цемента.
jcement.ru
Как изготовить цемент: технология, структура, состав
Дата: 9 января 2019
Просмотров: 2790
Коментариев: 0

Сложно найти человека, который не знаком с таким востребованным строительным материалом, как цемент. Ни одна стадия возведения объекта, начиная с закладки фундамента и заканчивая отделочными работами, не обходится без применения этого вяжущего вещества. При промышленном и гражданском строительстве используются кирпич, фундаментные блоки, стеновые панели. Но как добиться того, чтобы эти составляющие образовали единую конструкцию, прочную, долговечную. Вот тут на помощь приходит цемент. На сегодняшний день – это единственное вещество, способное создать из любого набора материалов монолитное изделие, которое на протяжении десятков и сотен лет только увеличивает прочностные характеристики.
Но какой процент людей задавался вопросом, из чего получают цемент, какие компоненты делают этот материал незаменимым? Наверно, немногие. Попробуем вкратце разобраться с этим вопросом, опишем, как происходит изготовление цемента.
Общие сведения
Цемент относится к неорганическим веществам. Вяжущие свойства он приобретает при взаимодействии с водой или водными растворами солей. Отметим, что это единственный вяжущий материал, который повышает прочностные характеристики при влажных условиях. В этом его отличие от гипса, который твердеет на воздухе.

Сегодня большая часть многоэтажных зданий выстроена именно благодаря бетонным конструкциям и заливке цемента
Так, что же такое – цемент? Это измельченное минеральное сырье со специальными модифицирующими добавками. В зависимости от наполнителя, выделим следующие виды:
- Портландцемент. Наиболее широко распространенный вид, включающий до 80% силиката кальция. Сфера применения не ограничена. Используется как при основных работах, так и при отделочных, поскольку возможно добавление красителей, повышающих декоративные свойства.
- Глиноземистый. Отличительная черта – ускоренное твердение, что дает возможность применять на объектах, требующих срочной реставрации (ликвидация разрушений после аварий, пожаров, затоплений).
- Магнезиальный. Главный элемент – оксид магния, добавляющий прочность, повышающий адгезионные свойства по отношению к древесине. К недостаткам относится повышенная вероятность коррозии, сужающая сферу применения.
- Кислотоупорный. В качестве наполнителя выступает гидросиликат натрия, который затворяется жидким стеклом. Служит основой для кислотостойких бетонов, растворов. Актуален при обустройстве объектов химической отрасли.
Структура
Изготовление цемента осуществляется на базе следующих компонентов:
- клинкера, основа которого – глина и известняк. Клинкер определяет прочность материала, производится при обжиге глиносодержащего и известнякового сырья. При нагреве плавится, образуя гранулированный состав с повышенной концентрацией кремнезёма, измельчается, повторно подвергается обжигу;

Цемент изготавливают на заводах, в промышленных масштабах
- гипса, влияющего на продолжительность процесса твердения цементного состава. Вводится, согласно рецептуре, как камни или готовый порошок, концентрация которого не превышает 5%;
- модифицирующих добавок, расширяющих область использования материала за счет приобретения специальных эксплуатационных свойств.
Используемое сырье
Массовое производство материала осуществляется на специализированных предприятиях. Можно попытаться изготовить цемент самостоятельно, так сказать, для личных нужд. Но работа эта неблагодарная, требующая специальных знаний технологии производства, точного соблюдения пропорций, чего сложно добиться в домашних условиях.
Лучше воспользоваться продуктом, изготовленным под наблюдением специалистов на высокопроизводительном оборудовании. Для изготовления цементного состава необходимы следующие специальные компоненты:
- природное карбонатное сырье (известняк-ракушечник, известковый туф, мел). Доля в суммарном объеме продукта составляет 74-82%. Структура исходного материала определяет степень эффективности взаимодействия используемых ингредиентов при обжиге;
- глинистые породы (глинистый сланец, суглинки, лесс). Процентное содержание глиносодержащей породы составляет 26-18%.

Для производства цемента применяют:смесь из известняка и глины – клинкер
Специальные добавки
При изготовлении применяются и другие компоненты (соли, окислы кальция, магния, фосфора), но их концентрация незначительна. Добавки вносятся для получения каких-либо определенных свойств – жаропрочности, кислотоустойчивости и пр. Чтобы получить возможность регулировать время схватывания цементного раствора, при изготовлении добавляют гипс.
Изготавливают материал с обязательным введением специальных добавок, повышающих эксплуатационные характеристики состава. Технология производства предусматривает применение следующих корректирующих компонентов:
- Добавок на базе ископаемого сырья с высокой концентрацией глинозема.
- Улучшителей, содержащих кремнезем.
- Ингредиентов, полученных из глинистых пород.
- Компонентов, полученных из апатитов и плавикового шпата.
Однозначно квартира! Комфорт, уют и тепло, вокруг люди и инфраструктура 812 ( 7.63 % )
Только частный дом! Вокруг тишина, покой, много места и мало людей! 4842 ( 45.48 % )
Зачем выбирать что-то одно? В городе квартира, а за городом — частный дом. 4529 ( 42.54 % )
Я — свободный Гражданин Планеты Земля! Мне не нужна рукотворная клетка! 464 ( 4.36 % )
Назад
Введение пластификаторов, предусмотренных спецификой технологического процесса, позволяет обеспечить следующие эксплуатационные характеристики состава:
- способность оказывать сопротивление проникновению воды в массив;
- сокращение продолжительности затвердевания состава;
- повышенную прочность монолитного массива;
- устойчивость к длительным, многократным стадиям замораживания с последующим оттаиванием;
- стойкость к влиянию жидких, газообразных агрессивных сред;

При замешивании раствора своими руками необходимо строго соблюдать пропорции компонентов и позаботиться об их качестве
- улучшенную адгезию с арматурой, надежно защищенной бетонным массивом от отрицательного воздействия коррозии;
- вязкость и подвижность бетонного раствора, облегчающие выполнение кладки, заливку монолитных конструкций за счет эластичности смеси.
Особенности состава
Независимо от того, по какой технологии изготавливают цемент, клинкер включает следующие ингредиенты:
- Силикаты кальция, играющие ключевую роль для обеспечения прочностных характеристик при изготовлении цементных составов. Согласно рецептуре, применяют в составе клинкера алит, доля которого составляет 50-70%, или белит с уменьшенной до 30% концентрацией.
- Кальциевые алюминаты, быстро реагирующие с водой, влияющие на процесс твердения цементного состава. Их количество составляет от 5 до 10% общего объема клинкера.
- Ферритные компоненты, в виде кальциевого алюмоферрита, вводимого в объеме 10-15% от общей массы.
- Различные соединения кальциевых оксидов, сульфатов щелочного типа, концентрация которых незначительна.
Концентрация компонентов зависит от специфики технологического процесса, вида производимого материала. Основными составляющими при изготовлении цемента являются известняковые, глинистые материалы, определяющие качество клинкера, применяемого в процессе производства.

Наиболее сложно сделать цемент для кладки камня и штукатурных работ
Специфика производства
Изготовление цемента предусматривает выполнение следующих производственных стадий:
- добычу сырья, содержащего гипс, глину, известняк;
- дробление добытого известняка, обеспечение требуемой влажности полученного продукта;
- измельчение известняковой массы, смешивание с глиной. Соотношение известняка и глины изменяется в зависимости от особенностей используемого сырья, ориентировочно соответствует пропорции 3:1. Результат – получение комбинированного, сухого или мокрого шлама;
- обжиг сырьевой массы при температуре до 1,5 тысячи градусов Цельсия, при котором происходит спекание шлама. Состав при этом превращается в гранулированную фракцию, называемую клинкером;
- измельчение до порошкообразной фракции клинкера с использованием специальных мельниц;
- дозирование и смешивание ингредиентов согласно марке будущего цемента. Процесс смешивания предусматривает введение до 5% гипса и специальных минеральных добавок.
Нюансы технологии
В зависимости от особенностей используемого сырья, изготавливают цементный состав по проверенным технологиям, которые предусматривают различные способы подготовки исходных компонентов.
Применяемый шлам может быть получен следующим образом:
- Сухим способом, значительно снижающим затраты на изготовление цемента. Особенностью сухого метода является сокращенный цикл производства, объединяющий ряд технологических стадий. Процесс измельчения и сушки ингредиентов осуществляется одновременно в специальной мельнице, куда подаются нагретые до высокой температуры газы. Полученная шихтовая фракция представляет порошкообразный состав необходимой влажности.
- По мокрой технологии, согласно которой мел применяется вместо извести. Мел смешивается с предусмотренными рецептурой компонентами, измельчается во влажной среде. Результат – получение шихты, влажность которой составляет до 50%. Шихтовая масса подвергается обжигу с последующим измельчением полученного клинкера.
- По комбинированной технологии, объединяющей элементы сухого и мокрого метода. Процесс предусматривает как увлажнение сухого состава, последующее гранулирование, отжиг, так и высушивание полусухого шихтового состава, произведенного мокрым способом.
Производственные предприятия осуществляют изготовление цемента с учетом особенностей имеющегося оборудования, близости к месту добычи сырья. При этом учитываются потребности на конкретные марки продукции.
Итоги
Материал статьи дает специальную информацию, как и из чего, осуществляется изготовление цемента, какие сырьевые материалы, технологические решения используют при изготовлении. Все тонкости знают профессионалы, работающие на предприятиях, производящих цемент.

На сайте: Автор и редактор статей на сайте pobetony.ru
Образование и опыт работы: Высшее техническое образование. Опыт работы на различных производствах и стройках – 12 лет, из них 8 лет – за рубежом.
Другие умения и навыки: Имеет 4-ю группу допуска по электробезопасности. Выполнение расчетов с использованием больших массивов данных.
Текущая занятость: Последние 4 года выступает в роли независимого консультанта в ряде строительных компаний.
pobetony.ru